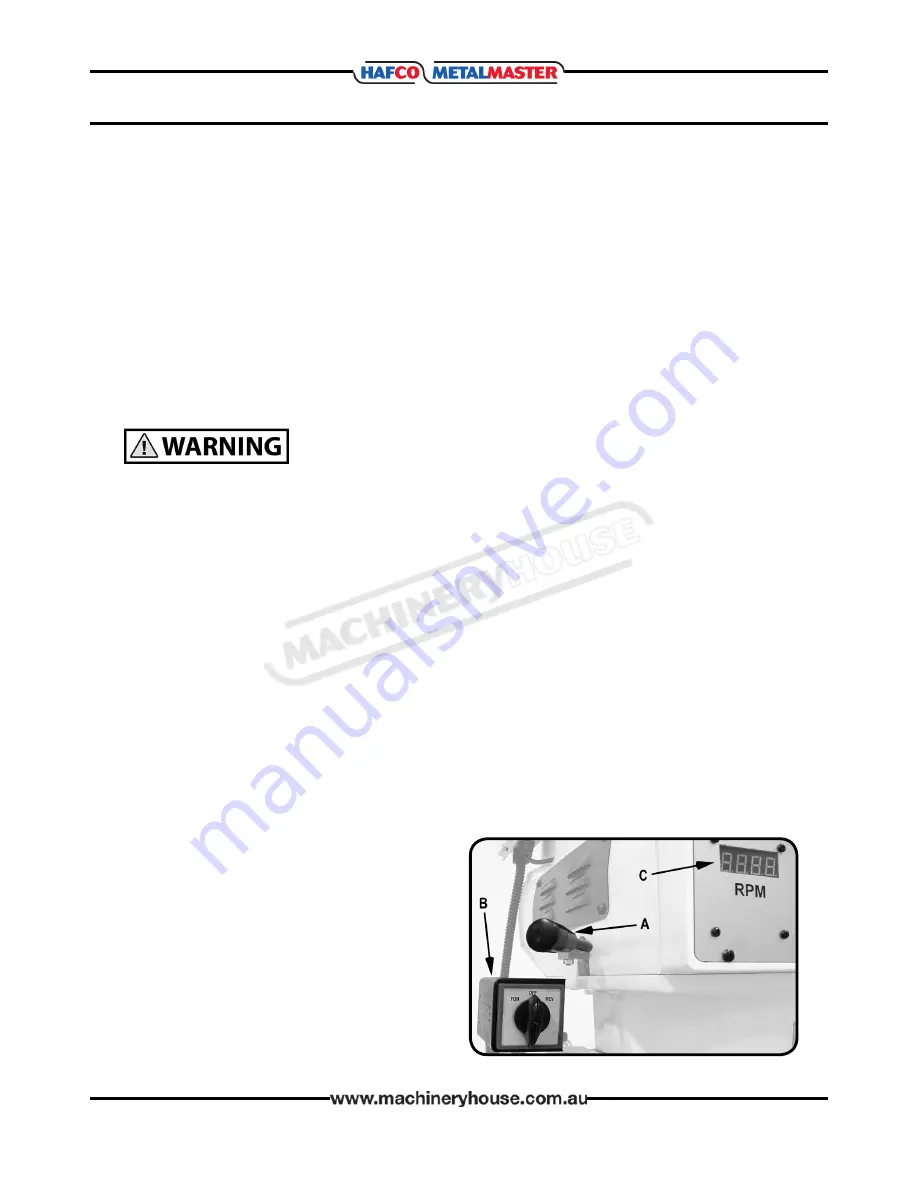
14
OPERATION MANUAL
Removal Of Mill Head Block
Before shipment, the mill head is rotated to the
side to lower the machine center of gravity. A
wooden block is placed between the mill head
and the worktable to support the head. The block
is removed by raising the mill head. Before at-
tempting to raise the mill head, refer to Mill Head
– Left/Right Adjustment in the Setup section(Page
22) for procedures to safely raise and setup the
mill head.
All electrical connections must be made by a
qualified electrician! Failure to comply may
cause serious injury!
Confirm power at the site matches the power
requirements of the mill before connecting to
the power source.
Electrical Requirement
BM-23V Single Phase 240Volt 15amp
BM-53V 3 Phase 415 Volt 20 amp.
BM-63V 3 Phase 415 Volt 20 amp
Before connecting to the power source, make sure
that the switch is in the off position.
The mill must be properly grounded in accordance
with electrical standards.
Check for proper spindle rotation in the high-
speed range. The spindle should rotate clockwise
when viewed from the top of the machine. If the
spindle rotates counter-clockwise, advise the qual-
ified electrician to chang
e
the rotation.
OPERATING INSTRUCTIONS
Operating Controls
The lubrication system is a manually operated,
one-shot system requiring operator intervention.
The operator must lower the one-shot lever to lu-
bricate the machine ways and lead screw or balls-
crews. The one-shot lubrication system reservoir
is located on the left side of the machine.
The position of the milling machine mill head can
be set up to accommodate the work piece being
machined. The mill head can be set up for angles
to the left or right and for fore and aft angles. The
mill head can also be rotated on its turret. The
ram can be moved back and forth to reach work
piece locations at the fore and aft extremes of
worktable travel. Refer to the Adjustments sec-
tion. (Page 22)
Motor Switch
The Motor Switch is on the upper left-hand side
of the mill head (B, Fig 4.1). The switch has three
positions: FWD (forward), OFF, and REV (reverse).
Setting the switch to FWD will provide clockwise
spindle rotation. Use FWD for normal, right-had
tooling
When the gearbox is in the low speed position
the motor switch must be in the REV position for
clockwise operation to occur. When the gearbox
is in high-speed position, the motor switch must
be in the FWD position to provide right-hand or
clockwise rotation. Refer to Fig. 5 for a chart of
required switch positions.
The motor switch controls the motor. The motor
can be switched from FWD to REV when the mo-
tor has stopped, and will reverse direction when
the switch setting is changed.
Fig. 4.1
Electrical Connection
Extension Cords
We do not recommend using an extension cord
with this machine. If you must, only use it if abso-
lutely necessary and only on a temporary basis.
Extension cords cause voltage drop, which can
damage electrical components and shorten motor
life. Voltage drop increases as the extension cord
size gets longer.
SET-UP AND INSTALLATION
Page 14
Instructions Manual for BM-23A (M595D)
12/02/2018
Содержание BM-23A
Страница 30: ...30 OPERATION MANUAL BM 23A BELT DRIVE HEAD Page 30 Instructions Manual for BM 23A M595D 12 02 2018 ...
Страница 33: ...33 OPERATION MANUAL Spindle Assembly Page 33 Instructions Manual for BM 23A M595D 12 02 2018 ...
Страница 37: ...37 OPERATION MANUAL BM 53VE Upper Head Parts List Page 37 Instructions Manual for BM 23A M595D 12 02 2018 ...
Страница 41: ...41 OPERATION MANUAL Base Assembly Page 41 Instructions Manual for BM 23A M595D 12 02 2018 ...
Страница 44: ...44 OPERATION MANUAL Lead Screw Assembly Page 44 Instructions Manual for BM 23A M595D 12 02 2018 ...