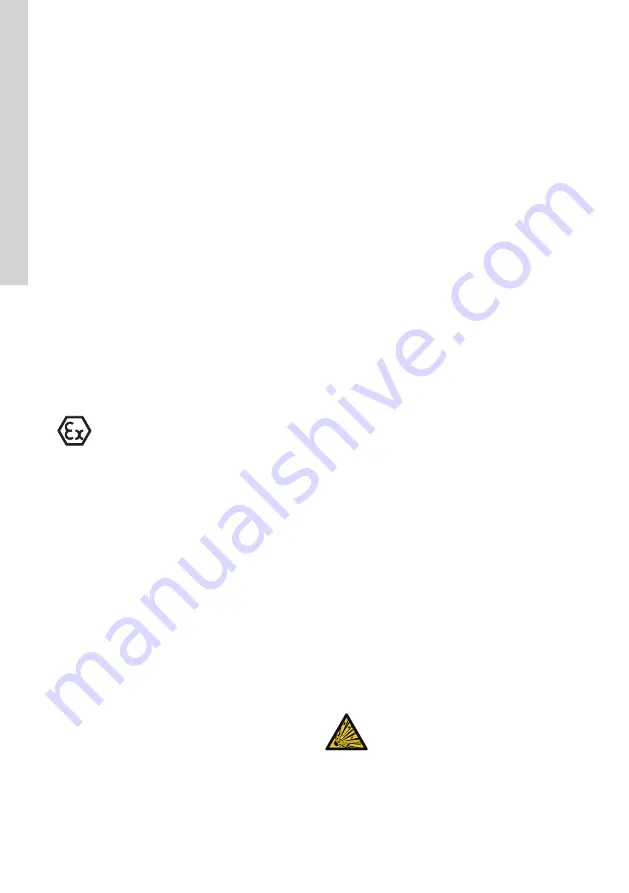
Special conditions for safe use of explo-
sion-proof pumps:
1. Make sure the moisture switches, wa-
ter-in-oil (WIO) sensor and thermal
switches are connected in separate cir-
cuits and have separate alarm outputs
(motor stop) in case of high humidity or
high temperature in the motor.
2. Bolts used for replacement must be
class A4-80 or A2-80 according to
EN/ISO 3506-1.
3. The flame path gaps of the motor are
specified by the manufacturer and are
more narrow than standard.
WARNING:
In case of repairs, always
use original service parts from the
manufacturer to ensure the correct di-
mensions of the flame path gaps.
4. During operation, the cooling jacket,
when fitted, must be filled with the
pumped liquid.
5. The level of the pumped liquid must be
controlled by level switches connected
to the motor control circuit. The mini-
mum level depends on the installation
type and is specified in this installation
and operating instructions. Use two in-
dependent stop level switches to avoid
hazardous situations.
6. Dry-running is not allowed.
7. Make sure the permanently attached
cables are mechanically protected and
terminated in a suitable terminal board.
8. The sewage pumps have an ambient
temperature range of -5 to +40 °C
(S72) or 0-40 °C (S74-78) and a maxi-
mum operating temperature of 40 °C.
The minimum ambient temperature for
a pump with a WIO sensor is 0 °C.
9. If a WIO sensor is installed, the control
unit must protect it against short circuit
current. The maximum current from the
control unit must be limited to 350 mA.
10. The maximum submersion depth is 20
m.
11. The customer must inform Grundfos if
the pump has been exposed to any
harmful external effects or aggressive
substances.
12. Dry installed pumps often have a high-
er temperature at the cable entries
than submerged ones. This may re-
duce the lifetime of the Ex-protection
equipment. According to EN/IEC
60079-14, it is a user responsibility to
regularly inspect the permanently at-
tached cables and cable entries for any
visual damage, cracks or embrittlement
caused by rubber aging.
13. For the level monitoring system, it is a
user responsibility to comply with the
requirements of part ’b’ of EN ISO
80079-37.
14. To prevent potential electrostatic dis-
charges from the pumped liquid, make
sure to comply with CLC/TR
60079-32-1.
15. The thermal protection of the stator
windings is rated for a 150 °C cut-out
temperature, ensuring the disconnec-
tion of the power supply. The power
supply must be reset manually.
16. Thermal protectors inside the pump
are critical to limit the surface tempera-
ture. Follow the electrical connection
instructions to avoid hazardous situa-
tions. The thermal protection of the
motor is ensured through a 150 °C
thermistor or a 150 °C thermal switch
per phase in the stator winding. The
protection circuit is set to limit the sta-
tor temperature to 150 °C. In this ar-
rangement, the temperature classifica-
tion is T3.
17. The temperature class for the product
is T4 (135 °C). T3 temperature class
applies only when a frequency convert-
er is used. The motor can be connec-
ted to a non-sinusoidal and/or variable
frequency power supply with a maxi-
mum frequency of 60 Hz.
18. For painted pumps, minimise the risk
of electrostatic discharge in the follow-
ing way:
• Earthing is mandatory.
• In dry installations, keep safety dis-
tance between pumps and walking
paths.
• Use wet fabric for cleaning.
19. The WIO sensor must always be com-
pletely submerged in the oil if the pow-
er is on.
DANGER
Explosive environment
Death or serious personal injury
‐
Make sure the cable entries are not
damaged to avoid sparks that may
cause explosion.
12
English (GB)
Содержание ST-55-520
Страница 2: ......