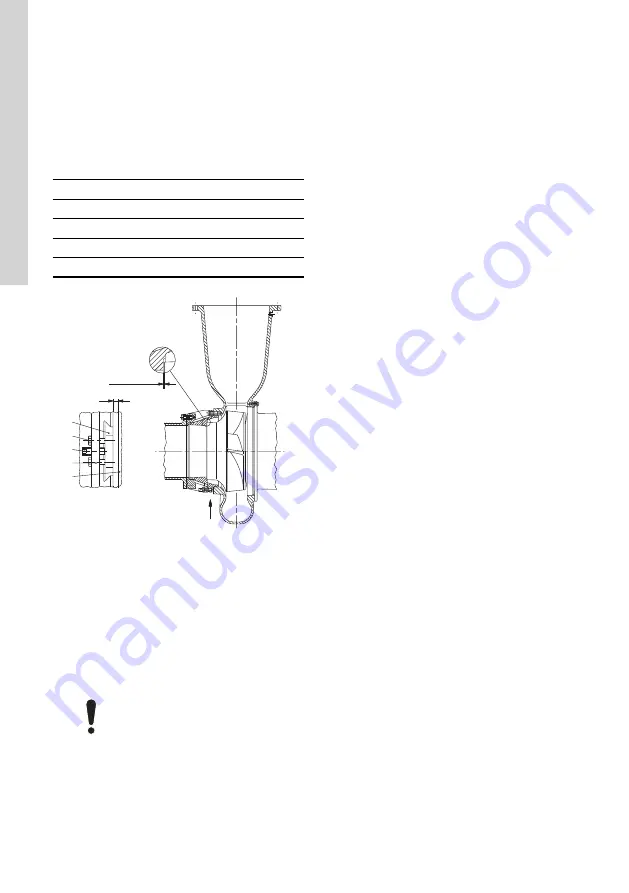
3. Loosen the fastening screws and draw back the
inlet cover by 1.3 mm ± 0.2 mm using the three
set screws (approximately one 150° turn with an
M27 set screw) and the distance "L" as reference.
4. Tighten all fastening screws and check that the
distance "L" at the three reference points is stable
at the new value.
Method 2
Pump types
Ranges 72 and 74
S3.110.xxx.xxxx.x.xxx.
S3.120.xxx.xxxx.x.xxx.
S3.135.500.xxxx.x.xxx.
50
35
12
12c
12a
L
S = 1.3 ± 0.2
A-A
A-A
TM033074
Impeller clearance, installation type D and H,
method 2
These pump types have threaded holes in the inlet
cover (12a) for the fastening screws (35). Set the
impeller clearance as follows:
1. Loosen the six fastening screws (35) and close
the impeller clearance "S" by tightening the three
set screws (12c). Tighten the screws diagonally to
move the inlet cover evenly.
Do not use undue force when tighten-
ing the fastening screws as this may
damage the bearings. The movement
is usually 1 to 3 mm.
2. Measure the distance "L" between the inlet cover
and the pump housing at three points next to the
set screws, using feeler gauges or calipers, then
note the distance.
3. Loosen the set screws and draw back the inlet
cover by 1.3 mm ± 0.2 mm using the six fastening
screws (approximately one 270° turn of an M12
fastening screw) and the distance "L" as
reference.
4. Tighten all set screws and check that the distance
"L" at the three reference points is stable at the
new value.
8.5 Pump cleaning and inspection
Clean the pumps regularly. Lift the pumps out of the
wet pit and clean them on site. Hose down the pump
externally with a high-pressure jet cleaner at a
maximum of 100 bar. Remove caked dirt from the
motor to ensure proper heat conductivity. A mild
detergent approved for disposal into the sewage
system may be used. The pumps may be scrubbed
with a soft brush, if necessary.
Inspection of the pump must include the following:
•
Search for cracks or other external damage.
•
Check the lifting bracket and lifting chain for wear
and corrosion.
•
Make sure the power cables and cable entries are
not damaged.
•
Check that the cables are firmly connected to the
motor top cover.
•
Check all visible screws for self-loosening and
tighten, if necessary.
The pumps are fitted with a vent valve at the top of
the cooling jacket. The valve may be removed and
cleaned, if necessary. Clean the vent hole before
refitting the valve after cleaning.
8.6 Power cables
Use manufacturer-approved and suitable cables only.
8.6.1 Cable entries
Secure the cable entries to the motor top cover by
tightening the screws evenly one by one until the
cable entries are lying flat against the top cover.
The minimum bending radius for cables is indicated in
the following table:
36
English (GB)
Содержание ST-55-520
Страница 2: ......