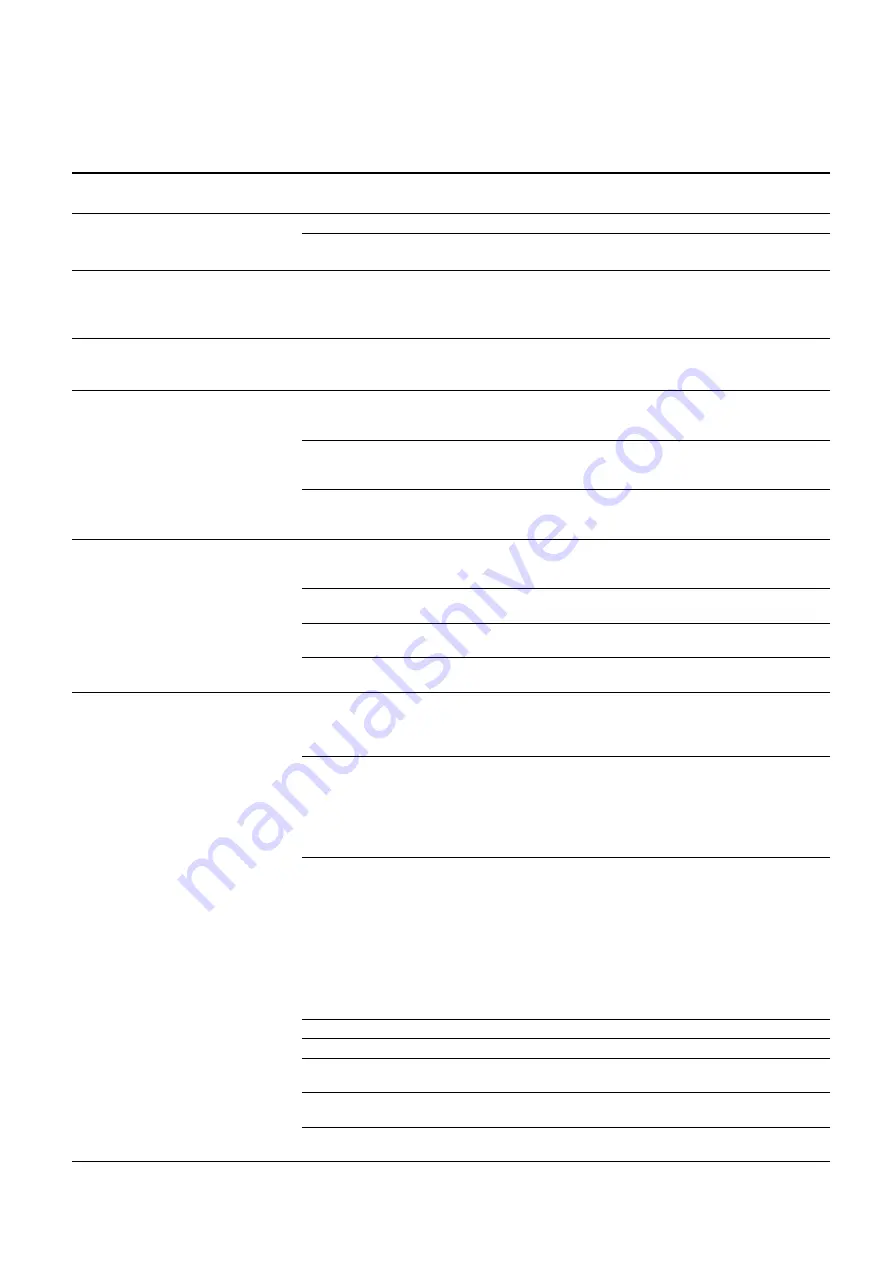
31
5.12 Fault finding
Activated relays can be deactivated using the [Esc] key. An
exception is the warning
relay, which is activated using
the signal
"reservoir tank empty". This relay is only deactivated, if the fault is
removed.
For trouble-free operation of the system, eliminate the cause of
the faults.
5.12.1 Faults
with error message
Error message if applicable
system reaction
Cause
Remedy
1. Pre-empty signal HCl/NaClO
2
:
a) Chemical container almost empty.
Change the chemical container.
– ClO
2
production proceeds.
– Warning
relay activated.
b) Floater on suction lance has wrong
orientation.
Call Service. Turn the floater upside down.
2. Empty signal HCl/NaClO
2
:
– ClO
2
production stops, continues
after fault elimination.
– Alarm relay activated.
Chemical container empty.
Change the chemical container.
3. Check ClO
2
batch:
– ClO
2
production proceeds.
– Warning
relay activated.
Warning message, undefined contents in the
reservoir tank after power supply failure.
Drain the reservoir tank manually, and
dispose of the content.
4. Level reservoir tank:
– ClO
2
production is aborted.
– Alarm relay activated.
Too much water is flowing into the reservoir
tank. The ClO
2
solution in the reservoir tank is
too diluted.
Stop the system.
a) Solenoid valve leaking.
Check the solenoid valve.
Call Service to clean or replace the filter in
the solenoid valve.
b) Faulty float switch in the reactor or too
much HCl and/or too much NaClO
2
flowing
into the reservoir tank.
Call Service to replace the float switch in
the reactor.
5. Timeout H
2
O supply 1:
– ClO
2
production is aborted.
– Alarm relay activated.
Level in the reactor increased too slowly
during the first water addition (after process
start). K1 not reached in time.
Call Service. Check the solenoid valve in the
TEST RELAY menu.
a) Filter in solenoid valve clogged or faulty
solenoid valve.
Check the solenoid valve. Replace the filter, if
necessary, or replace the solenoid valve.
b) Dilution water tap not sufficiently open.
If necessary, open the dilution water tap
further.
c) Float switch in the reactor damaged.
Call Service to replace the float switch in the
reactor.
6. Timeout HCl pump:
– ClO
2
production is aborted.
– Alarm relay activated.
Level in the reactor increased too slowly
during HCl supply between contacts K1 and
K2. K2 was not reached in time.
Check assembly faults of the hose from pump
to reactor.
Service: In TEST RELAY, check the HCl
pump.
a) Insufficient performance from the HCl
pump
– Air in suction line and/or dosing head.
– Pump not dosing.
– Leaking, clogged, porous or bent
discharge line.
Check the discharge line.
Call Service to replace.
b) HCl pump not sucking in
– Leaking, clogged, porous or bent suction
line.
– Deposits at the foot valve.
– Valve not installed correctly or clogged.
– Crystalline deposits in the valves.
– Diaphragm broken (leaking).
– Valve tappet torn out.
– Chemical container empty.
• Check the suction line and the suction
lance.
• Call Service to clean or replace the foot
valve.
• Call Service to clean the valves.
• Call Service to replace the diaphragm.
• Check the fill level of the chemical
container.
• If "HCl empty" signal is indicated, replace
the chemical container.
c) Flow in the pump not OK.
Ventilate the system.
d) Pump not running at all.
Call Service.
e) Cable breakage at the control system.
Check the cable from pump to control
system. Call Service.
f)
Faulty control system.
Check the control system.
Call Service to replace.
g) Float switch in the reactor damaged.
Call Service to replace the float switch in the
reactor.