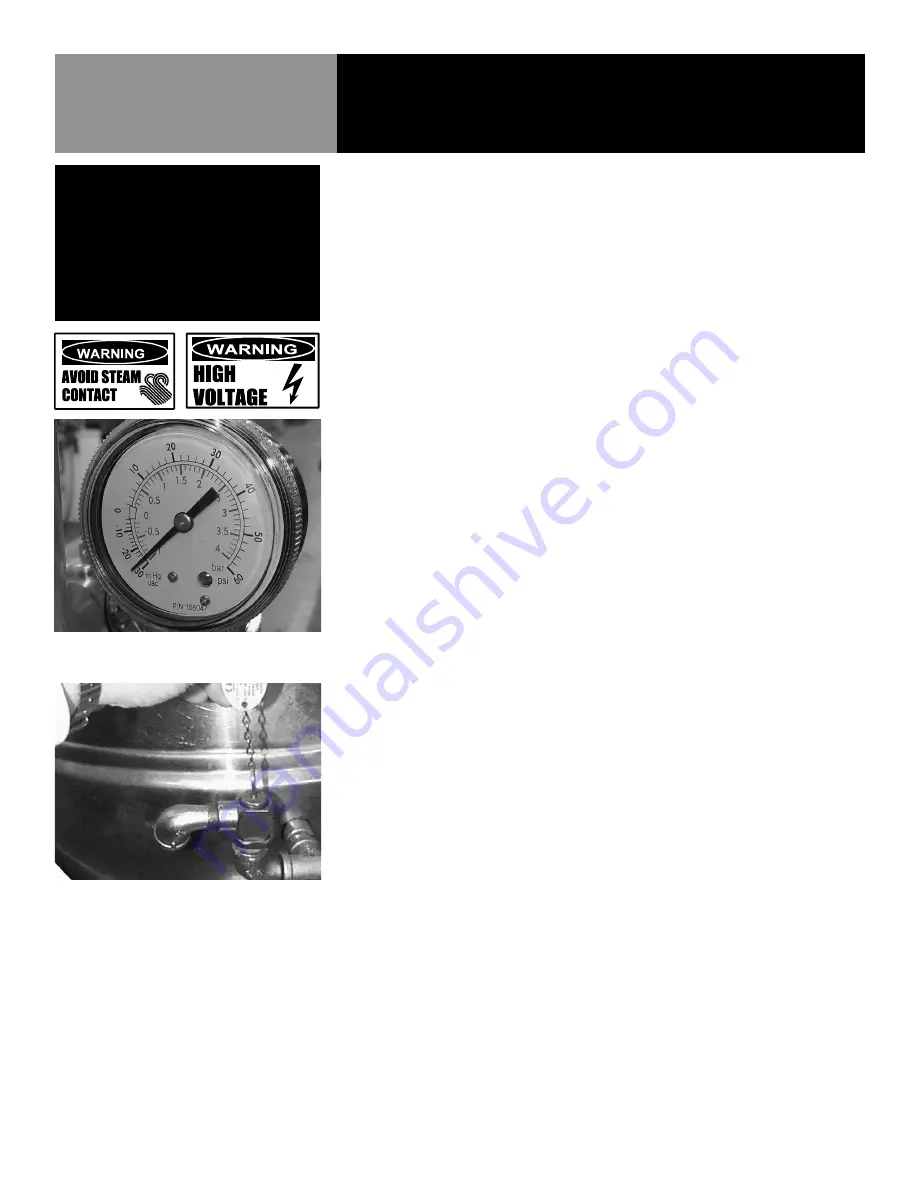
12 OM-TDB/TDBC-CE
Maintenance
NOTICE: Contact an authorized representative when repairs are required.
A Maintenance & Service Log is provided at the back of this manual. Each time
maintenance is performed on your kettle, enter the date on which the work was done,
what was done, and who did it. Keep this manual on file and available for operators to
use. Periodic inspection will minimize equipment down time and increase the efficiency
of operation. The following points should be checked:
1. Periodic Maintenance
BY OPERATOR
a.
Check the pressure/vacuum gauge every day. The gauge should show a
vacuum of 20 to 30 inches of Mercury or a range of -0.7 to -1.0 Bar, when
the kettle is cold. If it does not, see “Jacket Vacuum” on page 12.
b. Also check the jacket water level each day. It should be above mid point
of the round sight glass. If the level is low, see “Jacket Filling and Water
Treatment” on page 13.
BY SERVICE TECHNICIAN
c. Test the safety valve at least twice each month. Test the valve with the kettle
operating at 15 PSI (1 Bar/105 kPa), by pulling up the test chain for at least
five seconds. Then release the chain and let the valve snap shut. If the valve
does not activate, (there is no evidence of discharge, or the valve leaks)
stop using the kettle immediately and contact a qualified Groen service
representative.
d. The inside of the support housing should be kept clean.
e. At least twice a year, grease the two trunnion bearings. The bearings are
located within the kettle support housing. Remove the access panels from
the support housing with a screwdriver to gain access to the grease fittings.
Use a lithium-based, multi-purpose grease. When the access panels are
removed, the mounting bolts for the trunnion bearings and tilt switch can also
be checked for tightness.
f. On the crank-tilt models, the gear housing has fittings for proper lubrication
of moving parts. Because the gears do not run in oil, periodic lubrication
with grease is necessary. Frequency of lubrication will depend on operating
conditions, but the service should be performed at least once every six
months.
Add grease through the Zerk fittings on the gear housing until you see
grease flow out of the bearings around the trunnion shaft. Also place a liberal
amount of grease on the gear to cover the arc that is in contact with the
worm gear. When finished, reassemble access panels to support housing.
Electrical wiring should be kept securely connected and in good condition.
2. Jacket Vacuum
When the kettle is cold, a positive pressure reading or a reading around zero on
the pressure/vacuum gauge indicates the presence of air in the jacket. Air in the
jacket slows down the heating of the kettle.
TO REMOVE AIR:
a. Start the unit. (See the “Operation” section of this manual.) (Be sure there
is water or product in the kettle when heating).
WARNING
WHEN TESTING, AVOID ANY EXPOSURE TO
THE STEAM BLOWING OUT OF THE SAFETY
VALVE. DIRECT CONTACT COULD RESULT
IN SEVERE BURNS. DISCONNECT ELECTRICAL
POWER FROM THE KETTLE BEFORE
ATTEMPTING TO GREASE THE TRUNNION
BEARINGS.
Test the safety valve at least twice each month.
The pressure gauge should show a vacuum of
20 to 30 inches when the kettle is cold.