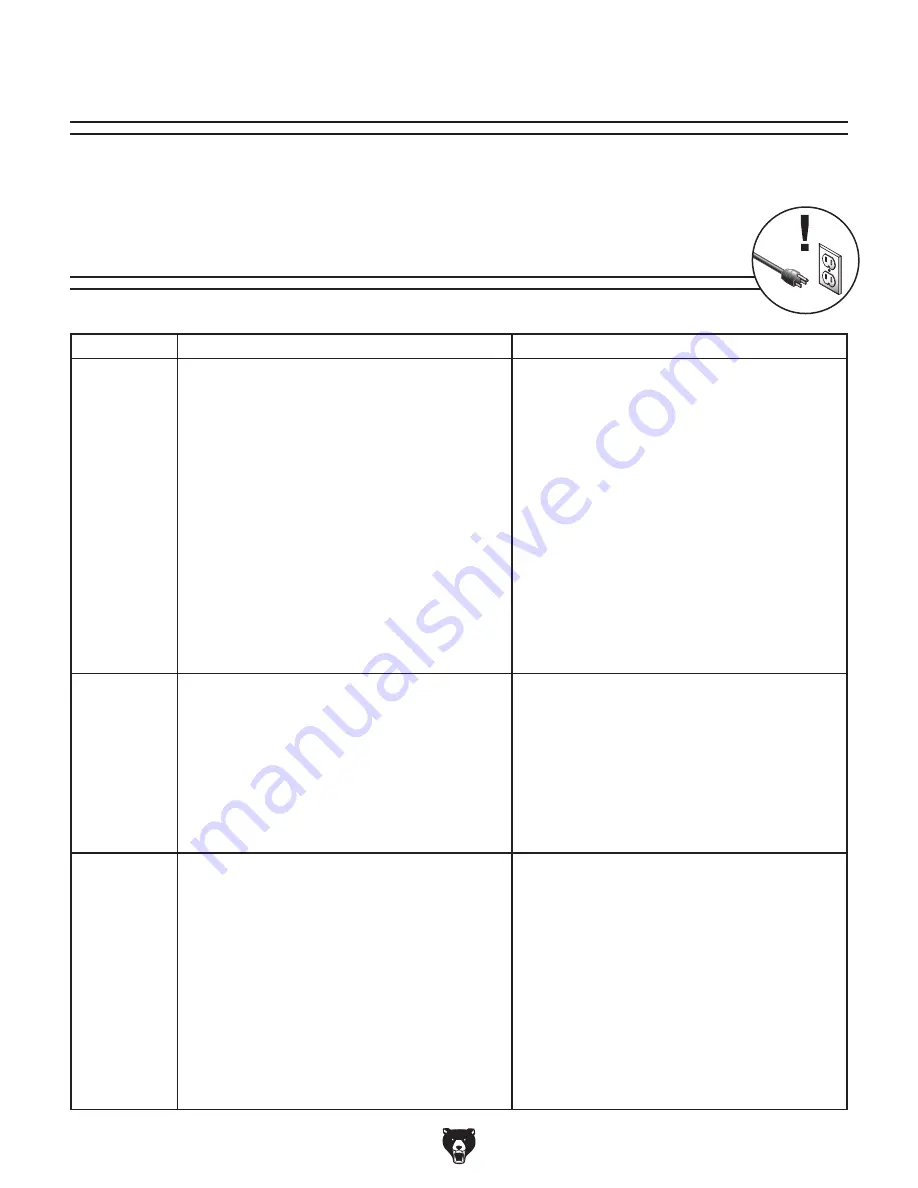
-56-
Model G0911–G0914 (Mfd. Since 05/21)
Review the troubleshooting procedures in this section if a problem develops with your machine. If you need
replacement parts or additional help with a procedure, call our Technical Support.
Note: Please gather the
serial number and manufacture date of your machine before calling.
SECTION 7: SERVICE
Troubleshooting
Motor & Electrical
Symptom
Possible Cause
Possible Solution
Machine does
not start, or
power supply
breaker
immediately
trips after
startup.
1. Emergency Stop button depressed/at fault.
2. Machine circuit breaker tripped or at fault.
3. Blown fuse.
4. Incorrect power supply voltage or circuit size.
5. Power supply circuit breaker tripped or fuse
blown.
6. Auxiliary system(s) has a short.
7. Control/ground wiring broken, disconnected, or
corroded.
8. Control panel/controller at fault.
9. Laser tube at fault.
10. Power supply at fault.
11. Motor or motor bearings at fault.
1. Rotate Emergency Stop button head to reset.
Replace if at fault.
2. Reset circuit breaker.
3. Replace fuse/ensure no shorts.
4. Ensure correct power supply voltage and circuit
size (
Page 16).
5. Ensure circuit is sized correctly and free of shorts.
Reset circuit breaker or replace fuse.
6. Inspect/test/replace if at fault.
7. Fix broken control/ground wires or disconnected/
corroded connections.
8. Inspect/test/replace if at fault.
9. Inspect for arcing at laser tube connections. Verify
wire insulation is preventing discharge to frame.
10. Inspect/test/replace if at fault.
11. Replace motor.
Machine
stalls or is
underpowered.
1. Laser beam path not aligned.
2. Machine undersized for task.
3. Pulley slipping on shaft.
4. One or more synchronous belt(s) are damaged,
binding, or slipping.
5. Stepper motor at fault.
1. Properly align laser beam path (
Page 71).
2. Increase power settings/decrease speed/use
thinner workpiece (
Page 40).
3. Tighten/replace loose pulley.
4. Inspect synchronous belt(s) on each axis for
damage or debris. Adjust belt(s) (
Page 59).
5. Test wire continuity between stepper motor and
stepper driver; repair/replace if at fault. Verify
stepper driver DIP switch configuration (
Page 82).
Machine
has vibration
or noisy
operation.
1. Guideway(s) contaminated or damaged.
2. Stepper motor or component loose.
3. Machine incorrectly supported.
4. Synchronous belt(s) worn, loose, pulleys loose/
misaligned, or belt slapping component.
5. Workpiece loose.
6. Stepper motor bearings at fault.
7. Stepper driver(s) at fault.
8. Incorrect value(s) in RDWorks Vendor Settings.
9. Auxiliary system(s) contacting machine frame.
1. Clean and lubricate guideways (
Page 48). Inspect
guideway(s) for damage, replace if at fault.
2. Replace damaged or missing bolts/nuts or tighten.
3. Adjust feet, shim, or tighten mounting hardware.
4. Inspect/replace synchronous belt(s) (
Page 59).
Secure pulley on shaft; realign if necessary.
5. Use holding fixture/secure workpiece with clamps.
6. Test by rotating shaft; rotational grinding/loose
shaft requires bearing replacement.
7. Verify stepper driver DIP switch configuration
(
Page 82).
8. Contact Grizzly Tech Support.
9. Secure auxiliary system(s) off of machine frame.
Содержание G0911
Страница 100: ......