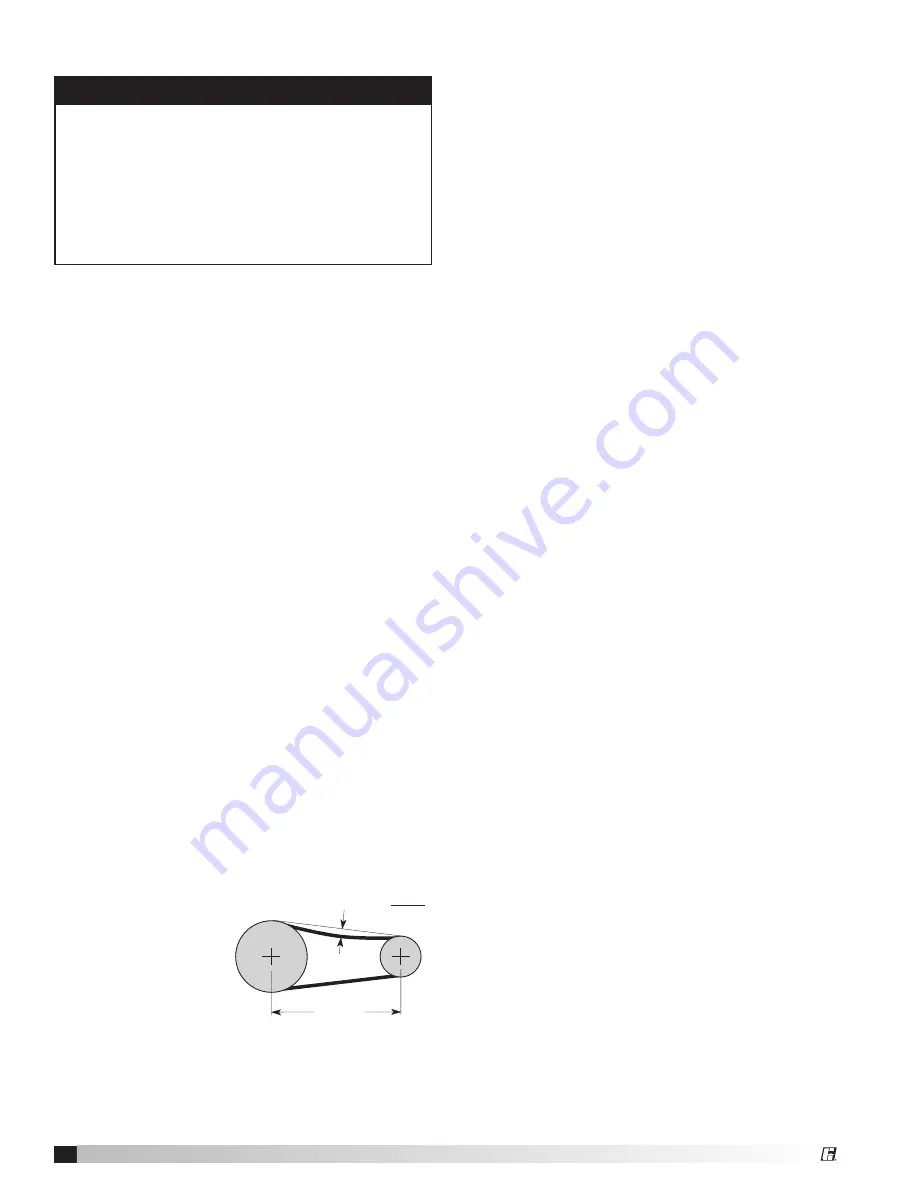
32
VersiVent Energy Recovery Ventilator
Maintenance Procedures
Lubrication
Check all moving components for proper lubrication.
Apply lubricant where required. Any components
showing excessive wear should be replaced to maintain
the integrity of the unit and ensure proper operation.
Dampers
Check all dampers to ensure they open and close
properly and without binding. Backdraft dampers can
be checked by hand to determine if blades open and
close freely. Apply power to motorized dampers to
ensure the actuator opens and closes the damper as
designed.
Gas Furnace
Maintain furnace in accordance with instructions in the
Indirect Gas-Fired Heat IOM shipped with this unit.
Fan Belts
Belts must be checked on a regular basis for wear,
tension, alignment, and dirt accumulation. Premature
or frequent belt failures can be caused by improper
belt tension (either too loose or too tight) or misaligned
sheaves. Abnormally high belt tension or drive
misalignment will cause excessive bearing loads and
may result in failure of the fan and/or motor bearings.
Conversely, loose belts will cause squealing on start-up,
excessive belt flutter, slippage, and overheated sheaves.
Both loose and tight belts can cause fan vibration.
When replacing belts on multiple groove drives, all belts
should be changed to provide uniform drive loading. Do
not pry belts on or off the sheave. Loosen belt tension
until belts can be removed by simply lifting the belts off
the sheaves. After replacing belts, ensure that slack in
each belt is on the same side of the drive. Belt dressing
should never be used.
Do not install new belts
on worn sheaves. If the
sheaves have grooves
worn in them, they must
be replaced before new
belts are installed.
The proper belt setting
is the lowest tension at which the belts will not slip
under peak load operation. For initial tensioning, set
the belt deflection at 1/64-inch for each inch of belt
span (measured half-way between sheave centers). For
example, if the belt span is 64 inches, the belt deflection
WARNING
REFER TO GENERAL SAFETY INFORMATION
Do not operate this unit without the filters and
birdscreen installed. They prevent the entry of foreign
objects such as leaves, birds, etc.
Do not remove access panels or other unit
components while standing on a ladder or other
unsteady base. Access panels and unit components
are heavy and serious injury may occur.
should be one inch (using moderate thumb pressure at
mid-point of the drive). Check belt tension two times
during the first 24 hours of operation and periodically
thereafter.
Fan Motors
Motor maintenance is generally limited to cleaning
and lubrication. Cleaning should be limited to exterior
surfaces only. Removing dust and grease buildup on
the motor housing assists proper cooling. Never wash-
down the motor with high pressure spray. Greasing
of motors is only intended when fittings are provided.
Fan motors typically have two grease fittings. Each
motor manufacturer has different lubrication schedules
for different models. Go to the motor manufacturer’s
website and download their maintenance requirements.
Do not over-lubricate motors or use an incompatible
grease. Many fractional motors are permanently
lubricated for life and require no further lubrication.
Fan Wheel and Fasteners
Wheels require very little attention when moving clean
air. Occasionally oil and dust may accumulate on the
wheel causing imbalance. When this occurs, the wheel
and housing should be cleaned to assure smooth and
safe operation. Inspect fan impeller and housing for
fatigue, corrosion, or wear.
Routinely check all fasteners, set screws and locking
collars on the fan, bearings, drive, motor base and
accessories for tightness. A proper maintenance
program will help preserve the performance and
reliability designed into the fan.
Bearings
Most bearings are permanently lubricated and require
no further lubrication under normal use. Normal use
being considered -20
°
to 120
°
F and in a relatively clean
environment. Some bearings are relubricatable and will
need to be regreased depending on fan use. Check your
bearings for grease zerk fittings to find out what type
of bearing you have. If your fan is not being operated
under normal use, bearings should be checked monthly
for lubrication.
Shaft bearings are the most critical moving part of a
fan. Therefore, special attention should be given to
keeping the bearings clean and well lubricated. Proper
lubrication provides for reduction in friction and wear,
transmission and dissipation of heat, extended bearing
life and prevention of rust.
In order for a lubricant to fulfill these tasks, the proper
grease applied at regular intervals is required.
If unusual conditions exist—temperatures below 32
°
F or
above 200
°
F, moisture or contaminants—more frequent
lubrication is required.
With the unit running, add grease very slowly with a
manual grease gun until a slight bead of grease forms at
the seal.
Belt Span
Deflection = Belt Span
64