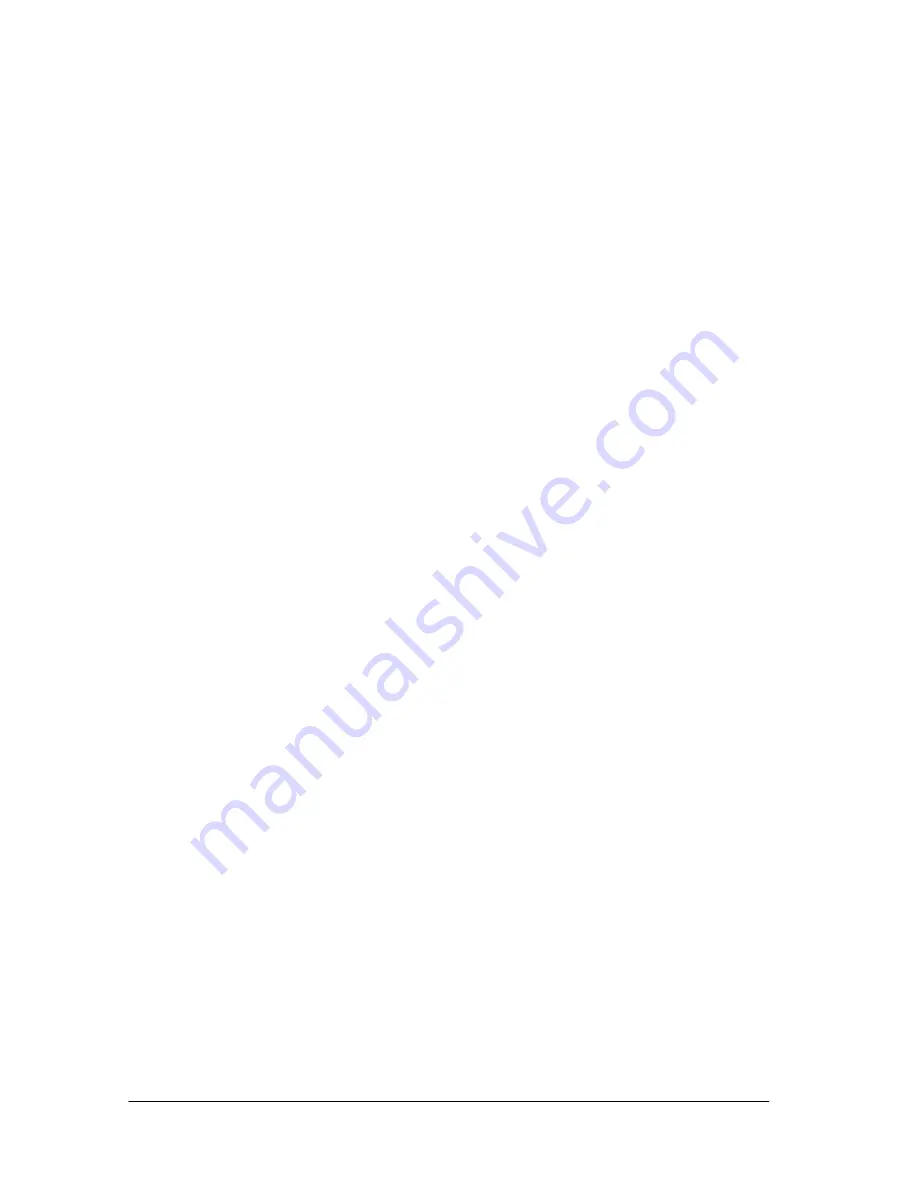
GRAUPNER GmbH & Co. KG D-73230 KIRCHHEIM/TECK GERMANY
Keine Haftung für Druckfehler. Technische Änderungen vorbehalten!
0058434
11/2007
15
Please note that all the windows and door sections must be an accurate fit over the openings in the
wheelhouse; aim to leave a projecting 1 mm flange of mahogany, in order to provide a support for the
glazing panels, parts 105.
26.
When this work is complete, the glazing panels, parts 105, and the window frames, parts 99 and
100, can be prepared and installed. The glazing panels are 46 x 28 mm in size, and should be
trimmed to fit individually. The window frames are cut from 1 x 5 mm and 2 x 3 mm mahogany strip
wood.
The two doors, parts 103, are each assembled from two identical 2 mm laser-cut parts. Trim the
glazing panels to fit from the rear. Make the door window frames, parts 105, from 1 x 5 mm
mahogany strips, and trim them to fit from the front. The door should be slightly narrower than the
frame in order to leave space for the door hinges, parts 113a. The door frame, parts 101 and 102, is
made from 1 x 5 mm and 2 x 3 mm mahogany strip.
27.
The wheelhouse floor, part 109, can either be left loose, so that it can be removed from
underneath, or glued in place permanently. To dissipate the warm air and provide a supply of fresh
air to the burner, you may wish to install one or two cooling fans, Order No. 1950, in the wheelhouse
floor; this is left up to you. The fan(s) are powered by a 12 V / 0.5 Ah battery which can be installed in
the space forward of the wheelhouse. Fit a switch, e.g. Order No. 4160.1, in the circuit, and you can
switch the fans on manually when the steam boiler is heating up, and then again at the conclusion of
each run. Of course, the wheelhouse doors must be left open during all runs, otherwise the fans will
be unable to move air as required; as an alternative you could leave several windows open.
28.
Cut the openings in the toplight, part 51, for the toplight covers, parts 52, and glue them
permanently to the superstructure. Drill 12 mm Ø holes in the toplight covers for the portholes, parts
53.
If you are installing a steam engine, you should omit the porthole glazing to allow the warm air to
escape freely. For the same reason four or all six of the toplight covers should also be left open, as
shown in the drawing.
Make up the hinges, parts 54, from 0.5 mm ABS, and bend them to shape by hand. The toplight
covers should also be fitted with handles, parts 55, and struts, parts 56.
29.
Each of the companionways, parts 57, can now be assembled from five laser-cut ABS parts. In
the same way assemble the three-part sliding roof, part 58.
The two companionway doors, parts 59, are assembled from laser-cut parts and fitted with the
portholes, parts 60. Complete them by adding the door handles, parts 61, and the hinges, parts 62,
which are made up from brass wire as shown in the drawing.
30.
The pressure ventilators, parts 64, and the portholes, parts 65, are supplied as ready-made parts,
and should be fitted in the positions shown in the drawing.
31.
The pressure ventilators, parts 66, are supplied as vacuum-moulded ABS parts. Cut out the parts,
join them, fill the joint lines, and attach them to the bases, parts 67, which are cut from aluminium
tube. To ensure that the pressure ventilators are securely mounted, reinforce each one on the inside
of the superstructure with a mounting ring, part 68.
32.
The steps, parts 69, and the mounting brackets, parts 70, are supplied as laser-cut parts which
are glued to the superstructure as shown in the drawing.
33.
Make up the handrails, parts 71, 72 and 73, from 1.5 mm Ø brass rod as shown in the drawing.
34.
The sliding hatch, part 74, is a laser-cut part, and is designed to be mounted in guide rails, parts
75, made from channel-section brass strip. The hatch should be left open while the steam-powered
version is operating. Bend a handle, part 76, to shape from brass rod, and attach it to the sliding
hatch to enable it to be moved to and fro.
35.
The angled hatches, parts 77, and the latch levers, parts 78, should also present no problems.
They can also be fitted in the “open” position if you wish.
36.
The lifebelts, parts 79, are supplied as ready-made plastic components; mount them on the lifebelt
supports, parts 80. The latter are laser-cut ABS parts, and should be bent to final shape by hand to
allow the lifebelts to be fitted.
37.
Attach two portholes, parts 81, to the front face of the superstructure.
38.
The funnel, part 82, is supplied as a ready-made GRP moulding. Two threaded rods, parts 83,
have to be glued or glassed in on the inside, exactly in the centre, as shown in the drawing (see
section D-D). These make it possible to attach the funnel really securely to the superstructure using
two M2.5 nuts and two washers.
39.
Parts 84 to 90 are all made up from brass tube or 0.5 mm brass sheet, as shown in the drawing,
and require no further description.
40.
The flagstock, part 92, takes the form of a length of 4 mm Ø beech dowel, fitted with a truck (top
knob), part 95. Glue a mounting tube, part 93, in the base, part 94, at an angle to accept the
flagstock. The flag, part 97, is a ready-made item, and should be attached to the flagstock using a
lanyard, part 98, and two rings, parts 96, as this system allows the flag to be run up or down at will.