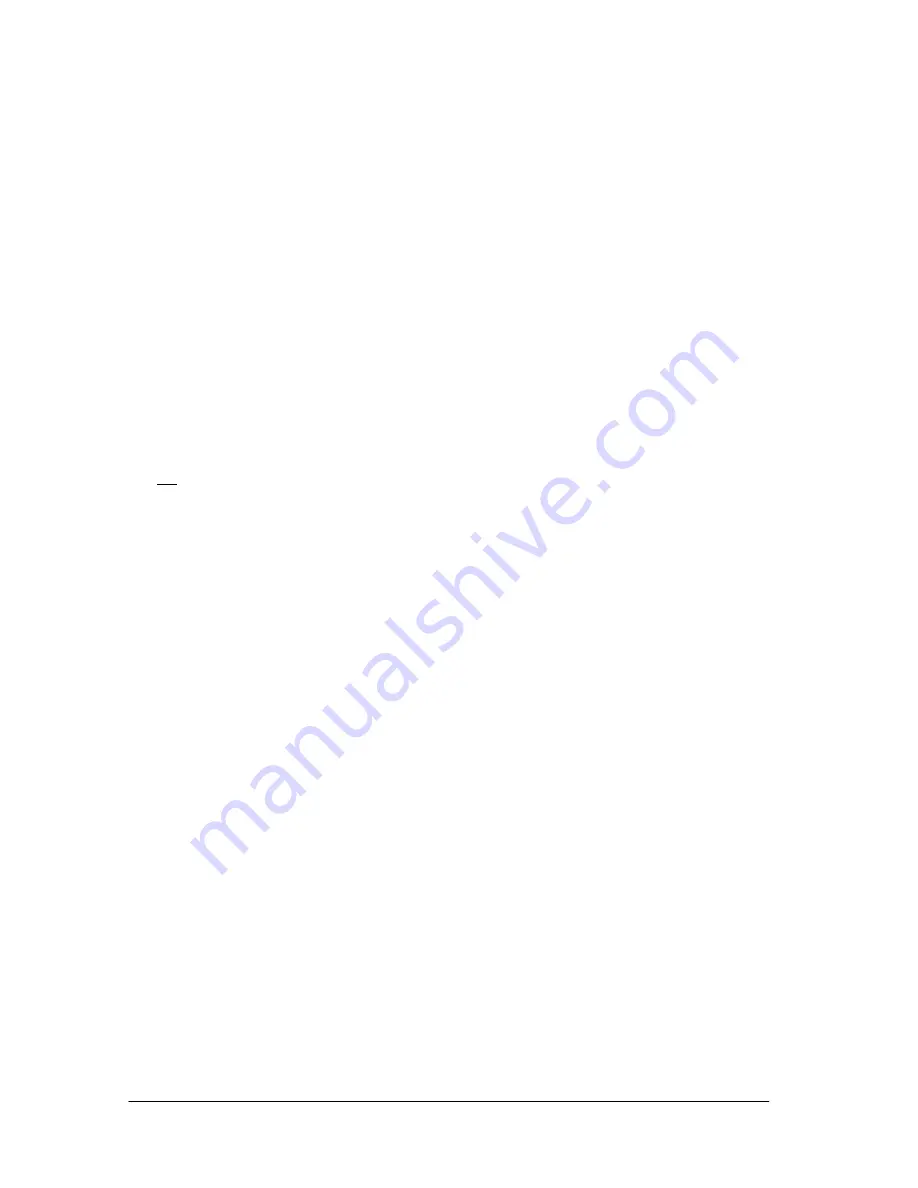
GRAUPNER GmbH & Co. KG D-73230 KIRCHHEIM/TECK GERMANY
Keine Haftung für Druckfehler. Technische Änderungen vorbehalten!
0058434
11/2007
14
6.
If you wish to remove the propeller shaft, please note that it can only be withdrawn forward,
because the rudder can no longer be removed. This applies unless you come up with a different
method of securing the rudder.
7.
The mounting blocks can now be glued securely in place, reinforcing the joints with glass cloth
and resin. We suggest that you attach the base plate to the blocks using wood-screws, so that it can
be removed again at any time if necessary. However, you may prefer to glue it in place permanently.
8.
The RC installation plate, part 13, can now be fitted. We recommend that the receiving system,
i.e. the servos and pushrods, should be installed at this early stage, as shown in the drawing.
For the electric version you will need one servo (usually included in the set) and a speed controller.
For the steam-powered version you require an additional two servos to control the steam engine. If
you intend installing a steam engine, please bear in mind that the engine funnel must be located in
the exact centre of the boat’s funnel.
9.
Mount the servos on the RC plate using suitable servo mounts (not included in the kit).
When you have completed all the installation work inside the hull, you can glue the main deck, part
16, in place, taking care to make the joints completely sound and watertight.
10.
The openings for the hawse pipes, part 17, and the chain pipes, parts 18, are first drilled using a
small bit, then gradually opened up to an oval shape using a round file until the pipes are an exact fit.
Cut the pipes to follow the contours of the hull sides before gluing them in place.
11.
The next step is a little tricky: cutting the scuppers (oval openings which allow water to drain off
the deck) in the bulwark. Three holes should be drilled or machined out on each side, by drilling
downward at an angle from the inside of the hull, as shown in the cross-section on the plan. Three 5
mm Ø holes side by side produce an opening about 15 x 5 mm in size, which can then be opened up
to final shape using files or similar tools. Use a flat file to finish off the scuppers, trimming them to the
exact shape shown in the drawing.
Tip: it is easy to damage the deck when drilling the holes, so lay a piece of 0.5 mm brass sheet on
the deck and push it up against the bulwark; this acts as a support for the drill bit.
12.
The eight cable hawses, part 21, can now be made from ABS and trimmed to fit in the bulwark at
the marked points. File out oval openings in the bulwark, so that the outer and inner halves of the
cable hawses meet in the middle.
13.
The 46 bulwark stanchions, parts 19, and the reinforcements, parts 20, are supplied as slightly
overlength laser-cut parts. Trim each one individually to fit against the bulwark, as shown in the
drawing.
14.
Cut the bollards, parts 22, to length from 10 mm Ø tube. Cut the transverse bars, part 23, from 3
mm Ø aluminium rod, and glue them to the bollards together with the ABS caps, part 24, as shown in
the drawing. The support plates, parts 25, are laser-cut ABS parts, and should be glued to the
bulwark as shown in the drawing.
15.
Attach the bow bollard, part 27, and the transverse bar, part 28, to the bow section 26.
16.
Assemble the stern platform, part 29, and the stanchions, part 30, as shown in the drawing; these
parts are cut from 5 x 2 mm and 6 x 6 mm mahogany strip.
17.
Solder together the framework, part 33, for the awning, part 31, and attach it to the bulwark (do
not glue it). Secure the awning framework by soldering the washers, parts 34, to the framework as
shown on the plan.
18.
Glue the lamp platform, part 35, to the awning framework using cyano.
19.
Parts 36 to 41 are ready-made parts, and are included in the Fittings Set. The anchor winch is
slightly more difficult to make, but it is supplied with its own assembly instructions.
20.
The tyre fenders, parts 42, are assembled from pairs of vacuum-moulded ABS shells, which
should be cut out carefully and glued together. Attach them to the cleats, parts 43, on the bulwark
stanchions using the retaining lanyards, parts 44.
21.
Each of the seat benches, parts 45, is assembled from six laser-cut ABS parts, then clad with the
longitudinal mahogany strips, parts 46, and the transverse strips, parts 47.
22.
The final stage is to attach the propeller, part 48, to the propeller shaft.
23.
The hawsers, parts 49, should be coiled up neatly as shown in the drawing, and glued to the deck.
24.
The next step is to prepare the GRP superstructure, part 50, by cutting all the openings for the
portholes, the toplight, the pressure ventilators, the funnel, the windows, the doors and the sliding
hatch, as shown in the various sketches on the plan.
25.
At this point we recommend that you complete the internal cladding of the wheelhouse, using
parts 106 to 110. These parts are all supplied as slightly oversized laser-cut 2 mm mahogany panels,
to allow for the fact that the laminating process tends to produce a finished moulding of varying
thickness. There are only two means of compensating for the irregularity: you can either machine out
the corners using a rotary milling cutter, or trim the individual mahogany parts to fit. Neither solution is
exactly easy or pleasant work, but the result is worth it, because the finished wheelhouse looks very
impressive.