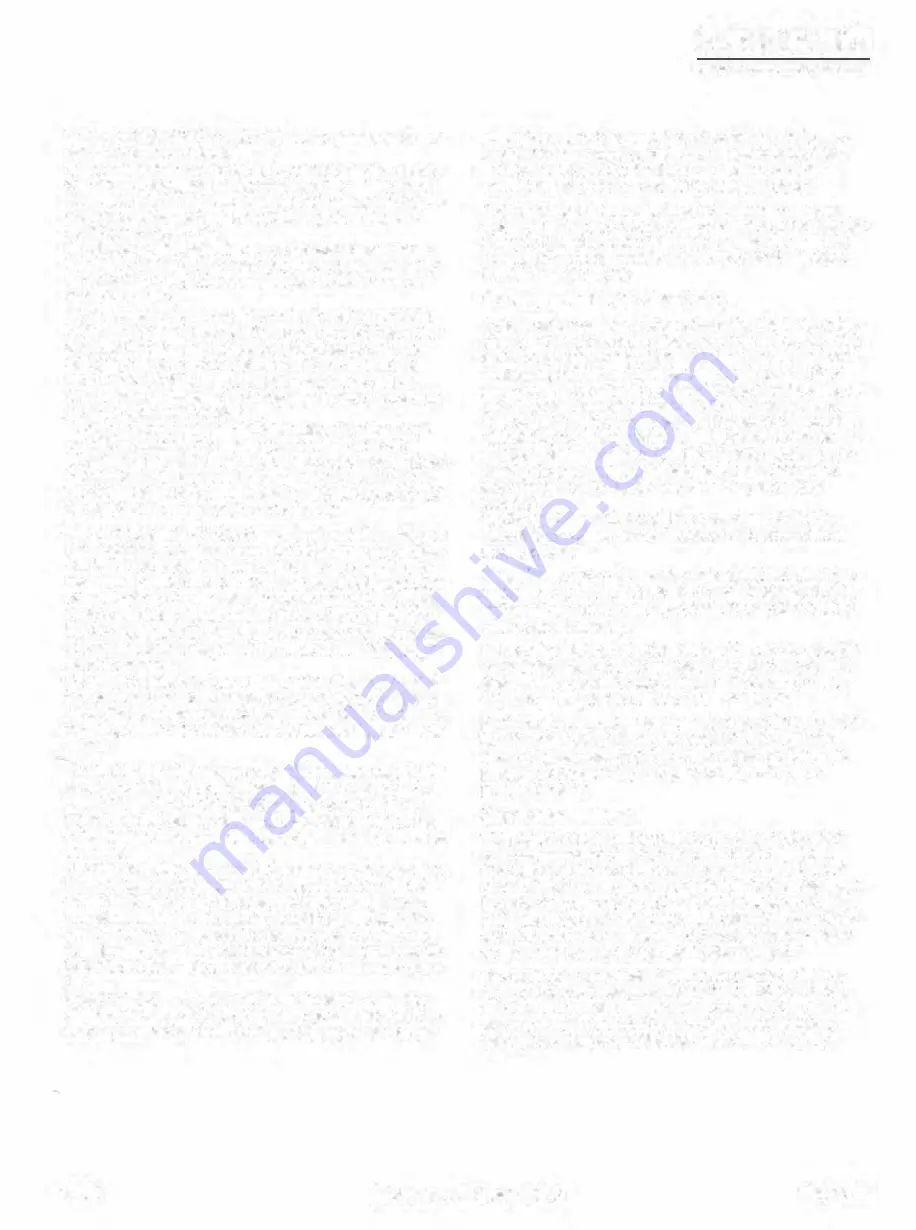
Oonsequently refay K17 A {line 17) is energized and ils con
tact K17 A in line 13 cfoses.
By pressing stop/reset button S10, relay Kt0A (line 1) is en
-ergized and energizes on its turn relays K11A, K14A, and
K1 SA in lin-e 3, 6 and 7 respectlvely; théir contacts in line 8
will close and signaJ lamp Ht 0 ("Bearing Jubrication too
low") în line 4 goes out.
As all safety switches in lîne
9
are normally closed (includ
ing S7 and S8, but only when the power suppfy is switched
on) relay
Kt GA
becomes energized as welf and its contact
in lfne 13 closes.
The compressor package can now be started by pressing
button S11 (fine 14), causing the oil pump motor relay
K2M
and time lag relay KH to be energized. Also signal lamp
H21 (oll pump in operation) lfgh1s up. Three contacts of
K2M
in line 19 wlll switch on the oil pump motor
and
an
other contact
K2M
(fine 15} shunts start button S11, sa that
the latter can naw be relea
s
ed.
-
, the oil pump is in operation lubricatîng oil pressure will
� built-up, causing the differenttal pressure switch S13
{line 15) to close and compressor drive motor refay Kt M, au
xiliary relay
K18A
and time lag relay K2T to be energized.
Also signa! lamp H20 ("Package in operation") lights up and
the service hours counter Pt starts running.
One of the contacts of K1 M in line 16 will switch on the com
pressor drive motor via a motor star/delta switch Q2 {if pres
ent) in fine 19; a second contact K1 M (fine 2) switches off
the heating element E1 and de-energizes the solenoid pilot
valve Y1 of the by-pass valve (by-passvalve closes) and a
third contact K1M shunts contact K17A (line 13). By open•
ing a fourth contact K1 M in line 14, time lag refay K1 T is de
energized, causfng relay K11 A (via contact K1T in line 3) to
remain energized.
Contact K1M (line 14) shoufd open within 80 seconds after
time lag relay K1T has been energized (therefore sufficient
lubricating oif pressvre should have been built up) otherwise
the compressor dnve motor will stop (contact K11A in line 8
opens).
imuttaneously with starting relay K1 M auxiliary relay K18A
,., energized. Two contacts of aux. relay K18A shunts con•
tact K1T (line 3) and differential pressure switch S13
(line
15) respectively and
by
closing a third contact
K18A
in line
5, the maximum suction pressure safety switch S3 becomes
operative.
The two remaining contacts
K18A
in fine 17 closes, causing
the automatic capacity controller/compressor ddve rnotor
current limiting unit S24 (if present) to become operative.
Also simultaneously with starting relay K1 M time lag relay
K2T is energized. Contact K2T (line 7) opens 30 seconds
after time lag relay K2T has been energrzed, so that the dif
ferential pressure safety switch S4 in line 7 becomes opera
tive.
Dlfferential pressure safety switéh S4 closes as soon as a
sufficient pressure difference between oil pressure and dis
charge pressure has been built up, whereby a new current
GRBSSa
8,EDIE"NBCSVOORSOiR'I-T4ETRIEBS&HlJ!ff\JNG
IIISlRUCTIONIIANl.\WIIMll.lfËLJ;n�
circuit is tormed. This current circuit enabfes to open con•
taci K2T in line 7 approx. 30 seconds after time lag relay
K2T has been energized without the compressor drive
motor being stopped (contact K1 SA in line 8 opens).
As the package is operating now, max. suction pressure
safety switch S3 (llne 5) wïll close as a result of the rapid fall
in suction pressure and will energize auxiliary relay K12A,
causing the capaclty çontrol to become operative (contact
K12A in fine 17 opens}.
Capacity control of the compressor
As soon as the suction pressure has tallen below the value
preset on the rnax. suction pressure safety switch, the refrîg
erating capacity can be adapted steplessly to the required
cooling lead by means of the slide valve actuator on lhe
compressor. The adjusting motor of this slide valve actuator
{line 17) may be actuated rnanually by two push buttons
S14 and S15, which can be selected by selecter switch S21
included in the control current wiring diagram. In the reverse
position otselector switch S21, the adjusting motor is actu
ated by the pilot switch of an automatic capacity control
ler/compressor drive motor current limiting unit S24 (if
present).
In this way it is possible to set the capacity control slide
valve into any given position between minïmum and
maxi
mum capacity.
When the capacity controf slide valve reaches its minimum
or maximum position, the adjusting motor is sw1tched off by
limil switches SH or S16 respectively, !ocated In the slide
valve actuator housing.
For remote electric indication of the position ot the capacity
controf slide valve, a potentiometer (if present) mounted in
side the sfide valve actuator and an indicator S26 (if pres
ent) can be included In the control current circuit.
Furthermore, extra micro switches (if present) S18, S19 and
S20 (if present; line 18) can be mounted in the actuator
housing to serve any switch purpose in the installaUOn de
pending on the actual (part-lead) capacity of the com
pressor invo1ved.
Stopping the package
The package is stopped
by
pressing button S10, in which
event auxiliary sta.rting relays K18A, K1 Mand K2M and
time lag relays K1T and K2T are released. All contacts of
these refays return again to their lnitial position; consequent
ly the neating element becomes operative again, the sole
noid pilot valve is energized (by-pass valve opens) and the
adjustîng motor of the capacity control slïde valve actuator
automatically moves back to the minimum position.
The package automatically stops when unsafe conditions
arlse and in which case one of the aforement1oned safety
switches or thermal protections become operative. Any un
safe condition is indicated by
one
of the signaf (warning)
lig hts (H1 0 - H19) included in the contro( current circuit.
92.01
Compressor Package GSLP
Page3.15