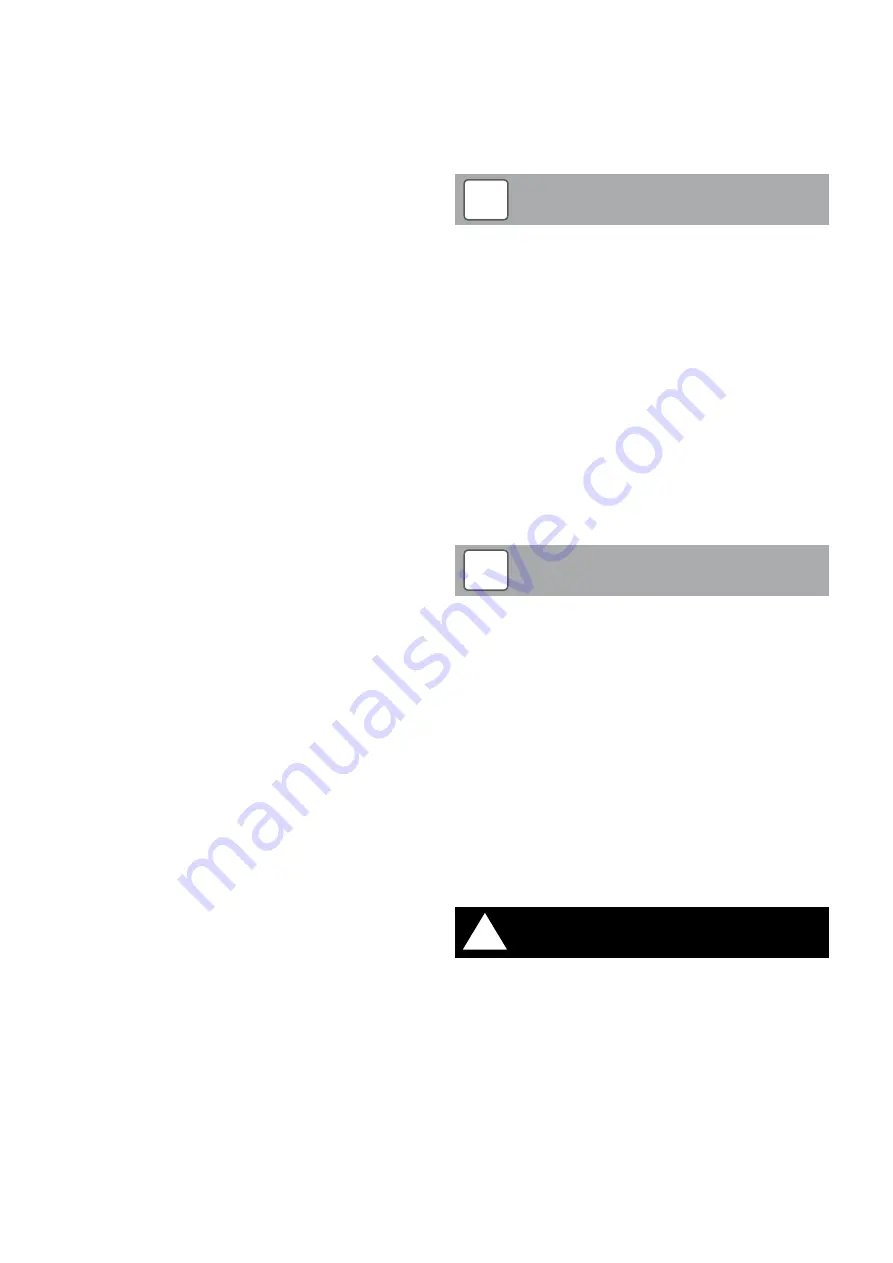
Section 4: Installation Information
Page 17
Grant Engineering (UK) Limited strongly recommends that
a Grant MagOne in-line magnetic filter/s (or equivalent*)
is fitted in the heating system pipework. This should be
installed and regularly serviced in accordance with the filter
manufacturer’s instructions.
* As measured by gauss. The MagOne magnetic filter has a gauss
measurement of 12000.
We recommend that both antifreeze and corrosion inhibitor
be used in the primary water system.
NOTE
!
4.7 Heating System Design Considerations
To achieve the maximum efficiency possible from the Grant
VortexAir, the heating system should be designed to the following
parameters:
Radiators:
•
Flow temperature 70°C, return temperature 50°C, differential
20°C
Underfloor:
•
Flow temperature 50°C, return temperature 40°C, differential
10°C
Size radiators with a mean water temperature of 60°C.
Design system controls with programmable room thermostats or
use weather compensating controls to maintain return temperatures
below 55°C.
The boiler should not be allowed to operate with return
temperatures of less than 40°C when the system is up to
operating temperature.
NOTE
!
The use of a pipe thermostat is recommended to control the return
temperature when using weather compensating controls.
4.8 Underfloor Heating Systems
In underfloor systems it is essential that the return temperature must
be maintained above 40°C to prevent internal corrosion of the boiler
water jacket.
4.9 Pipework Materials
Grant VortexAir units are compatible with both copper and plastic
pipe. Where plastic pipe is used it must be of the oxygen barrier
type and be of the correct class (to BS 7291-1:2010) for the
application concerned.
The first metre of pipework connected to both the heating
flow and return connections of the boiler must be made in
copper.
!
WARNING
4.10 Underfloor Pipework
Plastic pipe may be used on underfloor systems where the plastic
pipe is fitted after the thermostatic mixing valve.
Copper tube must be used for at least the first metre of flow and
return primary pipework between the boiler and the underfloor
mixing/blending valves.
•
BS 4543:3 Factory made insulated chimneys for oil fired
appliances.
•
BS 4876 Performance requirements for oil burning appliances
•
BS 5410:1 Code of Practice for oil firing appliances.
•
BS 5449 Forced circulation hot water systems.
•
BS 7593 Code of Practice for treatment of water in heating
systems.
•
BS 7671 Requirements for electrical installations, IET Wiring
Regulations.
For a list of recommendations and regulations to the heat pump,
refer to the Installation and Servicing Instructions supplied with the
heat pump.
4.5 Completion
Please ensure that the OFTEC CD/10 installation completion report
(provided with the boiler) is completed in full.
Leave the top copy with the User.
Retain the carbon copy.
Ensure that:
a. The User Information pack (supplied with the boiler) is handed
over to the Householder.
b. The householder is aware of how to use the product.
c. The householder is aware of the need to refer to the online
calculator and change the stat.
d. The product is registered for the Grant product guarantee.
4.6 Before you Commission
4.6.1 Flushing and Corrosion Protection
To avoid the danger of dirt and foreign matter entering the VortexAir
the complete heating system should be thoroughly flushed out
– both before the VortexAir is operated and then again after the
system has been heated and is still hot.
This is especially important where the VortexAir is installed as a
replacement for a boiler on an existing system.
In this case the system should be first flushed hot, before the old
boiler is removed and replaced by the VortexAir.
For optimum performance after installation, this VortexAir and the
central heating system must be flushed in accordance with the
guidelines given in BS 7593:2006 ‘Treatment of water in domestic
hot water central heating systems’.
This must involve the use of a proprietary cleaner, such as Sentinel
X300 or X400, or Fernox Restorer.
After flushing, a suitable thermal fluid should be used (such as
Sentinel R600) specifically designed for use in air source heat pump
installations. This provides long term protection against corrosion
and scale as well as the risk of the freezing in the external section of
the heating system (i.e. the flexible hoses, condenser and circulating
pump within the heat pump casing) in the event of power failure
during winter months.
In order to avoid bacterial growth, due to the lower system operating
temperatures, a suitable Biocide (such as Sentinel R700) should
also be used in conjunction with the thermal fluid.
Both the thermal fluid and biocide should be added to the system
water when finally filling the heating system.
Alternatively, Fernox HP5C can be used (or HP15C for greater frost
protection).
This is a suitable thermal fluid that already contains a suitable
biocide.
Full instructions on the correct use of thermal fluids and biocides are
supplied with the products, but further information can be obtained
from either www.sentinel-solutions.net or www.fernox.com.
Failure to implement the above guidelines by fully flushing the
system and using a suitable thermal fluid and biocide corrosion
inhibitor will invalidate the heat pump product guarantee.
Содержание Aerona3 Series
Страница 57: ...Section 13 Flue System and Air Supply Page 57 Figure 13 8 Flue clearances...
Страница 77: ...Section 19 Spare Parts Page 77 Figure 19 4 15 21kW baffles Figure 19 5 21 26kW baffles...
Страница 84: ...Appendix A Page 84 Appendix A...
Страница 85: ...Appendix A Page 85...
Страница 86: ...Appendix A Page 86...
Страница 87: ...Appendix A Page 87...