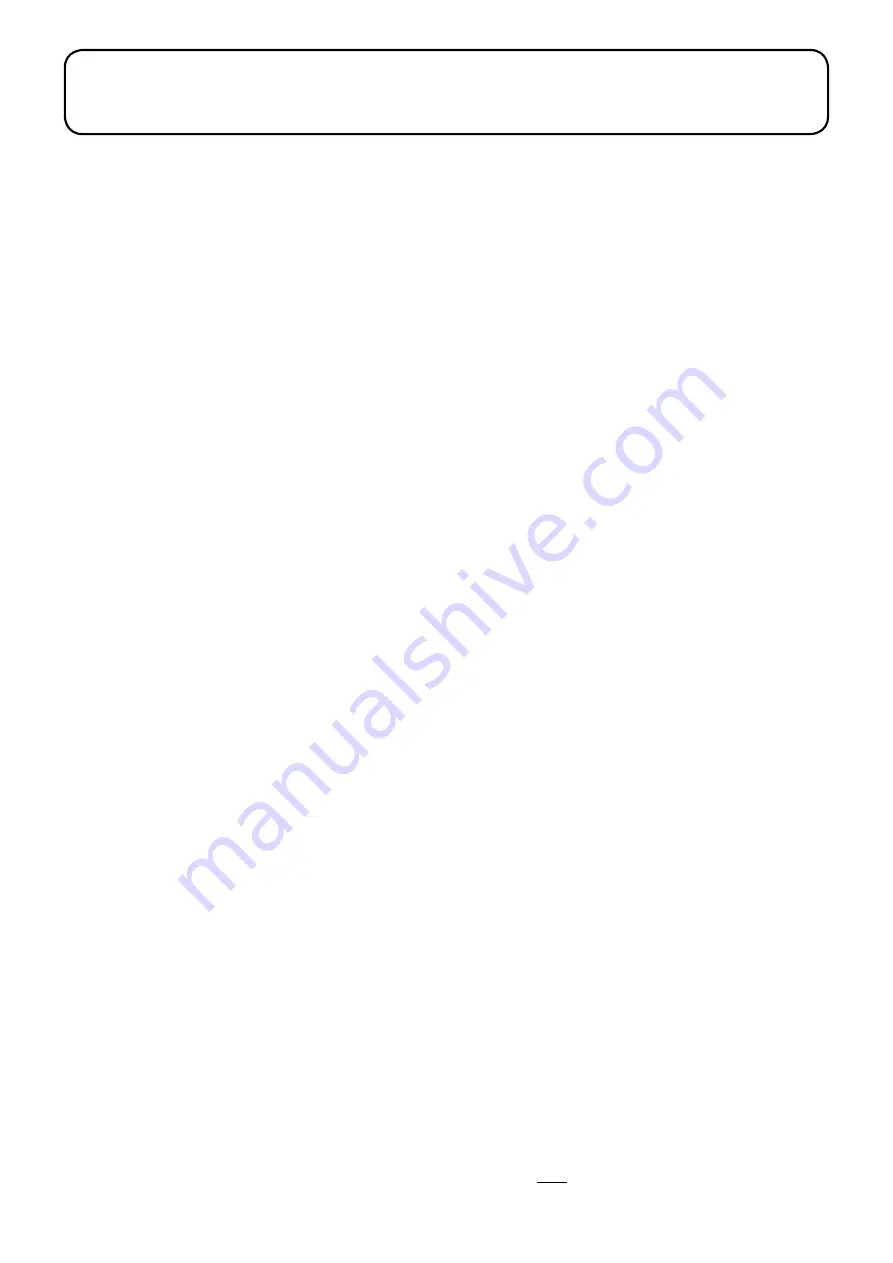
Section 24: Guarantee
Page 82
You are now the proud owner of a Grant Vortex condensing boiler
from Grant Engineering (UK) Limited which has been designed to
give years of reliable, trouble free, operation.
Grant Engineering (UK) Limited guarantees the manufacture of
the boiler including all electrical and mechanical components for a
period of
twelve months from the date of installation
4
, provided
that the boiler has been installed in full accordance with the
installation and servicing instructions issued.
This will be extended to a total period of
two years
if the boiler is
registered with Grant Engineering (UK) Limited
within thirty days
of installation
4
and serviced at twelve monthly intervals
3
. See main
Terms and Conditions below.
Registering the product with Grant Engineering (UK) Limited
Please register your Grant Vortex condensing boiler with Grant
Engineering UK Limited
within thirty days of installation
. To do
so visit www.grantuk.com and follow the links to the ‘Homeowners
Zone’, where you can register your boiler for a further
twelve
months
guarantee (giving
two years
from the date of installation
4
).
This does not affect your statutory rights
1
.
If a fault or defect occurs within the manufacturer’s
guarantee period
If your boiler should fail within the guarantee period, you must
contact Grant Engineering (UK) Limited who will arrange for the
repair under the terms of the guarantee, providing that the boiler
has been correctly installed, commissioned and serviced (if the
appliance has been installed for more than twelve months) by a
competent person and the fault is not due to tampering, running
out of oil, oil contamination, debris, system water contamination,
misuse, trapped air or the failure of any external components
not supplied by Grant Engineering (UK) Limited, e.g. fire valve,
motorised valve, etc.
This two year guarantee only applies if the boiler is registered
with Grant Engineering (UK) Limited within thirty days of
installation
4
and is serviced after twelve months
3
.
In the first instance
Contact your installer or commissioning engineer to ensure
that the fault does not lie with the system components or any
incorrect setting of the system controls that falls outside of the
manufacturer’s guarantee otherwise a service charge could result.
Grant Engineering (UK) Limited will not be liable for any charges
arising from this process.
If a fault covered by the manufacturer’s guarantee is found
Ask your installer to contact Grant Engineering (UK) Limited
Service Department on +44 (0)1380 736920 who will arrange for a
competent service engineer to rectify the fault.
Remember - before you contact Grant Engineering (UK)
Limited:
•
Ensure the boiler has been installed, commissioned and
serviced by a competent person in accordance with the
installation and servicing instructions.
•
Ensure there is oil to supply the burner.
•
Ensure the problem is not being caused by the heating system
or its controls. Consult the boiler handbook for guidance.
Free of charge repairs
During the
two year
guarantee period no charge for parts or
labour will be made, provided that the boiler has been installed and
commissioned correctly in accordance with the manufacturer’s
installation and servicing instructions, it was registered with Grant
Engineering (UK) Limited within thirty days of installation
4
and, for
boilers over twelve months old, details of annual service is available
3
.
24 Guarantee
The following documents must be made available to Grant
Engineering (UK) Limited on request:
•
Proof of purchase
•
CD10 Installation Completion Form (or equivalent document)
•
CD11 Commissioning Report Form (or equivalent document)
•
Service documents (CD11 or equivalent document)
Chargeable repairs
A charge may be made (if necessary following testing of parts) if the
breakdown is due to any fault(s) caused by the plumbing or heating
system, e.g. contamination of parts due to system contamination,
sludge, scale, debris or trapped air. See ‘Extent of manufacturer’s
guarantee’.
Extent of manufacturer’s guarantee:
The manufacturer’s guarantee does not cover the following:
•
If the boiler has been installed for over
two years
.
•
If the boiler has not been installed, commissioned, or serviced
by a competent person in accordance with the installation and
servicing instructions.
•
The serial number has been removed or made illegible.
•
Fault(s) due to accidental damage, tampering, unauthorised
adjustment, neglect, misuse or operating the boiler contrary to
the manufacturer’s installation and servicing instructions.
•
Damage due to external causes such as bad weather
conditions (flood, storms, lightning, frost, snow, or ice), fire,
explosion, accident or theft.
•
Fault(s) due to incorrectly sized expansion vessel(s), incorrect
vessel charge pressure or inadequate expansion on the
system.
•
Fault(s) caused by external electrics and external components
not supplied by Grant Engineering (UK) Limited.
•
Problems caused by lack of oil or faults with the oil storage and
supply system.
•
Fault(s) due to contamination of the oil storage and supply
system, e.g. water or debris.
•
Bleeding or removing oil storage tank contamination or
blockages from oil lines.
•
Problems due to the flue system being incorrectly fitted or not
installed to meet installation requirements.
•
Boiler servicing, de-scaling or flushing.
•
Cleaning out condensate traps/discharge pipes or thawing out
frozen condensate pipework.
•
Checking and replenishing system pressure.
•
Oil supply pipelines, electrical cables and plugs, external
controls not supplied by Grant Engineering (UK) Limited.
•
Heating system components, such as radiators, pipes, fittings,
pumps and valves not supplied by Grant Engineering (UK)
Limited.
•
Instances where the oil boiler has been un-installed and re-
installed in another location.
•
Use of spare parts not authorised by Grant Engineering (UK)
Limited.
•
Consumable items including, but not limited to, oil nozzles, oil
hoses, gaskets.
IMPORTANT
The nozzle and braided oil hose supplied with the boiler are only
covered for the period up to the time of the first service (twelve
months). Both
must
be changed on the first service and on every
annual service thereafter.
Содержание Aerona3 Series
Страница 57: ...Section 13 Flue System and Air Supply Page 57 Figure 13 8 Flue clearances...
Страница 77: ...Section 19 Spare Parts Page 77 Figure 19 4 15 21kW baffles Figure 19 5 21 26kW baffles...
Страница 84: ...Appendix A Page 84 Appendix A...
Страница 85: ...Appendix A Page 85...
Страница 86: ...Appendix A Page 86...
Страница 87: ...Appendix A Page 87...