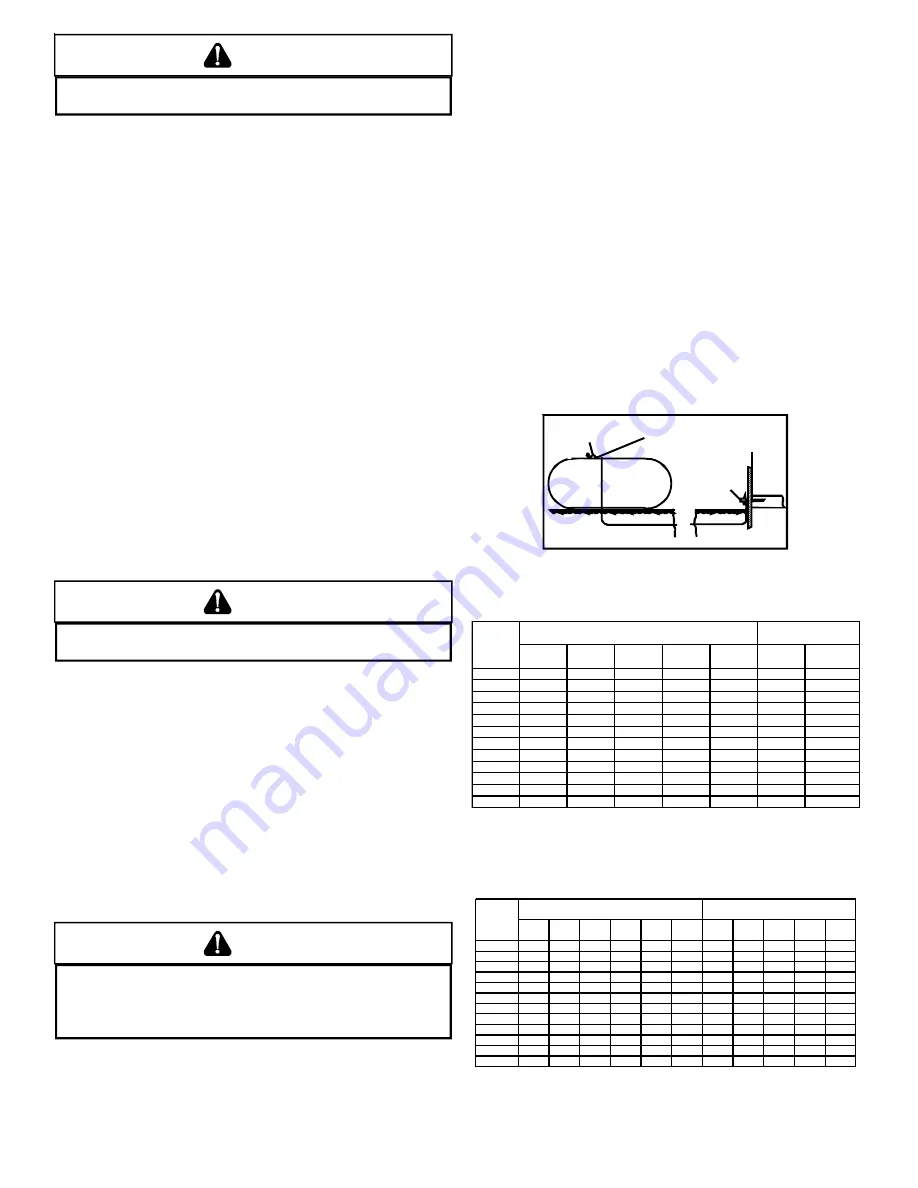
25
CAUTION
E
DGES OF SHEET METAL HOLES MAY BE SHARP.
U
SE GLOVES AS A
PRECAUTION WHEN REMOVING HOLE PLUGS.
D
IRECT
/S
TANDARD
I
NLET
P
IPING
When gas piping enters
directly
to the gas valve through the
stan-
dard
inlet hole, the installer must supply straight pipe with a ground
joint union to reach the exterior of the furnace. The rigid pipe must
be long enough to reach the outside of the cabinet to seal the
grommet cabinet penetration. A semi-rigid connector to the gas
piping can be used outside the cabinet per local codes.
I
NDIRECT
/A
LTERNATE
I
NLET
P
IPING
When gas piping enters
indirectly
to the gas valve through the
alternate
gas inlet hole the following fittings (starting from the gas
valve) to reach the outside of the cabinet must be supplied:
•
Coupling.
•
90 degree elbow.
•
2 inch close nipple.
•
90 degree elbow.
•
Straight pipe, with a ground joint union, to reach the exterior
of the furnace. The rigid pipe must be long enough to reach
the outside of the cabinet so as to seal the grommet cabinet
penetration. A semi-rigid connector to the gas piping can
be used outside the cabinet per local codes.
G
AS
P
IPING
C
HECKS
Before placing unit in operation, leak test the unit and gas connec-
tions.
WARNING
T
O AVOID THE POSSIBILITY OF EXPLOSION OR FIRE, NEVER USE A MATCH OR
OPEN FLAME TO TEST FOR LEAKS.
Check for leaks using an approved chloride-free soap and water
solution, an electronic combustible gas detector, or other approved
testing methods.
NOTE:
Never exceed specified pressures for testing. Higher
pressure may damage the gas valve and cause subsequent
overfiring, resulting in heat exchanger failure.
Disconnect this unit and shutoff valve from the gas supply piping
system before pressure testing the supply piping system with pres-
sures in excess of 1/2 psig (3.48 kPa).
Isolate this unit from the gas supply piping system by closing its
external manual gas shutoff valve before pressure testing supply
piping system with test pressures equal to or less than 1/2 psig
(3.48 kPa).
P
ROPANE
G
AS
T
ANKS
AND
P
IPING
WARNING
P
ROPANE GAS IS HEAVIER THAN AIR AND ANY LEAKING GAS CAN SETTLE IN
ANY LOW AREAS OR CONFINED SPACES.
T
O PREVENT PROPERTY DAMAGE,
PERSONAL INJURY, OR DEATH DUE TO FIRE OR EXPLOSION CAUSED BY A
PROPANE GAS LEAK, INSTALL A GAS DETECTION WARNING DEVICE.
A gas detecting warning system is the only reliable way to detect a
propane gas leak. Rust can reduce the level of odorant in propane
gas. Do not rely on your sense of smell. Contact a local propane
gas supplier about installing a gas detecting warning system. If
the presence of gas is suspected, follow the instructions on Page
4 of this manual.
All propane gas equipment must conform to the safety standards
of the National Board of Fire Underwriters, NBFU Manual 58.
For satisfactory operation, propane gas pressure must be 11 inch
w.c. at the furnace manifold with all gas appliances in operation.
Maintaining proper gas pressure depends on three main factors:
1.
Vaporization rate, depending on temperature of the liquid,
and “wetted surface” area of the container or containers.
2.
Proper pressure regulation. (Two-stage regulation is
recommended for both cost and efficiency).
3.
Pressure drop in lines between regulators, and between
second stage regulator and the appliance. Pipe size will
depend on length of pipe run and total load of all appliances.
Complete information regarding tank sizing for vaporization, rec-
ommended regulator settings, and pipe sizing is available from
most regulator manufacturers and propane gas suppliers.
Since propane gas will quickly dissolve white lead and most stan-
dard commercial compounds, special pipe dope must be used.
Shellac-based compounds resistant to the actions of liquefied
petroleum gases such as Gasolac
®
, Stalactic
®
, Clyde’s
®
or John
Crane
®
are satisfactory.
Refer to the following illustration for typical propane gas installa-
tions.
200 PSIG
Maximum
5 to 15 PSIG
(20 PSIG Max.)
Continuous
11" W.C.
Second Stage
Regulator
First Stage
Regulator
Propane Gas Installation (Typ.)
Sizing Between First and Second Stage Regulator*
Maximum Propane Capacities listed are based on 2 psig pressure drop at 10 psig setting.
Capacities in 1,000 BTU/hour.
Pipe or
Nominal Pipe Size
Tubing
Tubing Size, O.D. Type L
Schedule 40
Length,
3/8"
1/2"
5/8"
3/4"
7/8"
1/2"
3/4"
Feet
10
730
1,700
3,200
5,300
8,300
3,200
7,500
20
500
1,100
2,200
3,700
5,800
2,200
4,200
30
400
920
2,000
2,900
4,700
1,800
4,000
40
370
850
1,700
2,700
4,100
1,600
3,700
50
330
770
1,500
2,400
3,700
1,500
3,400
60
300
700
1,300
2,200
3,300
1,300
3,100
80
260
610
1,200
1,900
2,900
1,200
2,600
100
220
540
1,000
1,700
2,600
1,000
2,300
125
200
490
900
1,400
2,300
900
2,100
150
190
430
830
1,300
2,100
830
1,900
175
170
400
780
1,200
1,900
770
1,700
200
160
380
730
1,100
1,800
720
1,500
To convert to capacities at 15 psig settings - multiply by 1.130
To convert to capacities at 5 psig settings - multiply by 0.879
Propane Gas Piping Chart I
Sizing Between Single or Second Stage Regulator and Appliance*
Maximum Propane Capacities Listed are Based on 1/2" W.C. pressure drop at 11" W.C. setting.
Capacities in 1,000 BTU/hour.
Pipe or
Nominal Pipe Size
Tubing
Tubing Size, O.D. Type L
Schedule 40
Length,
3/8"
1/2"
5/8"
3/4"
7/8"
1-1/8"
1/2"
3/4"
1"
1-1/4" 1-1/2"
Feet
10
39
92
199
329
501
935
275
567
1,071
2,205
3,307
20
26
62
131
216
346
630
189
393
732
1,496
2,299
30
21
50
107
181
277
500
152
315
590
1,212
1,858
40
19
41
90
145
233
427
129
267
504
1,039
1,559
50
18
37
79
131
198
376
114
237
448
913
1,417
60
16
35
72
121
187
340
103
217
409
834
1,275
80
13
29
62
104
155
289
89
185
346
724
1,066
100
11
26
55
90
138
255
78
162
307
630
976
125
10
24
48
81
122
224
69
146
275
567
866
150
9
21
43
72
109
202
63
132
252
511
787
200
8
19
39
66
100
187
54
112
209
439
665
250
8
17
36
60
93
172
48
100
185
390
590
*Data in accordance with NFPA pamphlet NO. 54
Propane Gas Piping Chart II
Содержание GMS95
Страница 34: ...34...