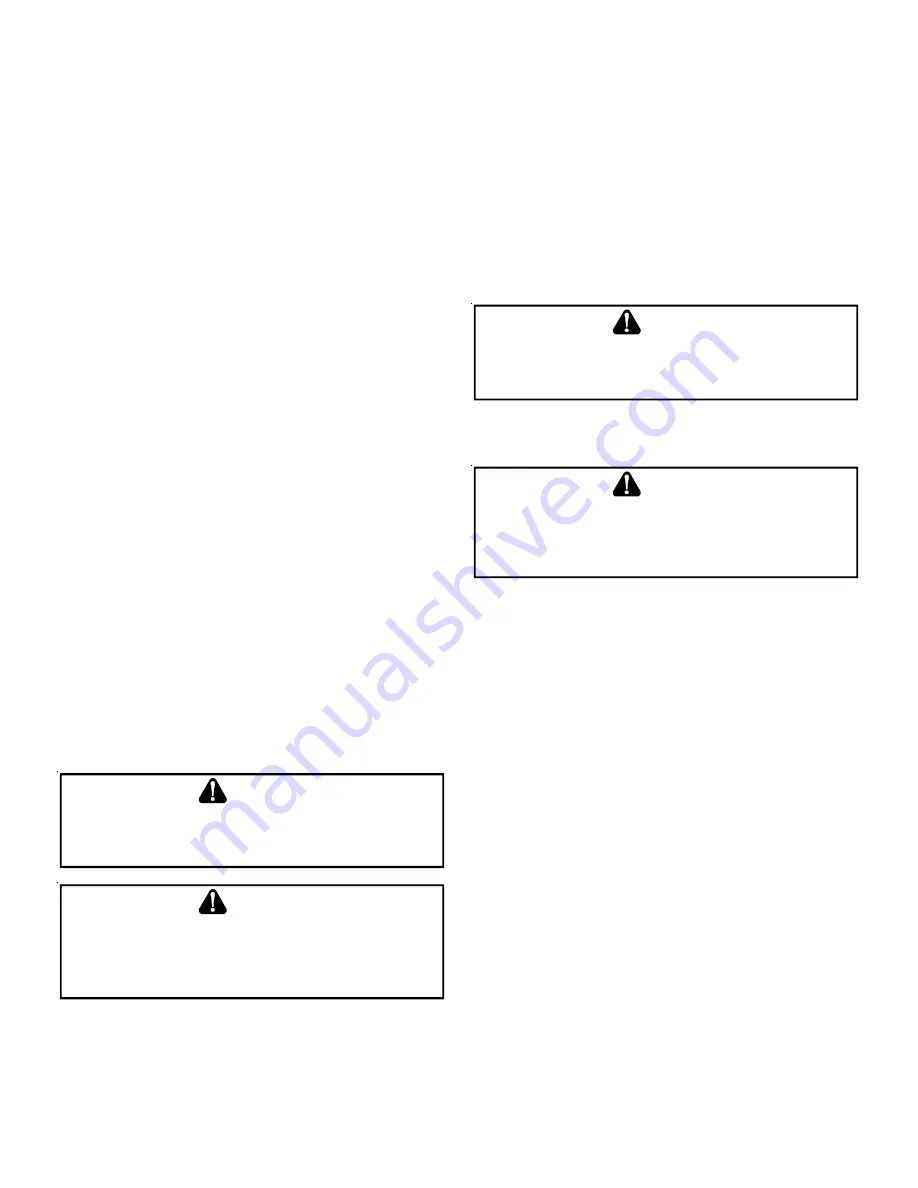
4
Torch heat required to braze tubes of various sizes
is proportional to the size of the tube. Tubes of
smaller size require less heat to bring the tube to
brazing temperature before adding brazing alloy.
Applying too much heat to any tube can melt the
tube. Service personnel must use the appropriate
heat level for the size of the tube being brazed. NOTE:
The use of a heat shield when brazing is
recommended to avoid burning the serial plate or
the finish on the unit.
1. The ends of the refrigerant lines must be cut square,
deburred, cleaned, and be round and free from nicks or
dents. Any other condition increases the chance of a
refrigerant leak.
2. “Sweep” the refrigerant line with nitrogen or inert gas
during brazing to prevent the formation of copper-oxide
inside the refrigerant lines. The POE oils used in R-
410A applications will clean any copper-oxide present
from the inside of the refrigerant lines and spread it
throughout the system. This may cause a blockage or
failure of the metering device.
3. After brazing, quench the joints with water or a wet cloth
to prevent overheating of the service valve.
4. Ensure the filter drier paint finish is intact after brazing.
If the paint of the steel filter drier has been burned or
chipped, repaint or treat with a rust preventative. This is
especially important on suction line filter driers which
are continually wet when the unit is operating.
NOTE:
Be careful not to kink or dent refrigerant lines. Kinked
or dented lines will cause poor performance or compressor
damage.
Do NOT make final refrigerant line connection until plugs
are removed from refrigerant tubing.
NOTE:
Before brazing, verify indoor piston size by checking
the piston kit chart packaged with indoor unit.
L
EAK
T
ESTING
(N
ITROGEN
OR
N
ITROGEN
-T
RACED
)
T
O
AVOID
THE
RISK
OF
FIRE
OR
EXPLOSION
,
NEVER
USE
OXYGEN
,
HIGH
PRESSURE
AIR
OR
FLAMMABLE
GASES
FOR
LEAK
TESTING
OF
A
REFRIGERATION
SYSTEM
.
WARNING
T
O
AVOID
POSSIBLE
EXPLOSION
,
THE
LINE
FROM
THE
NITROGEN
CYLINDER
MUST
INCLUDE
A
PRESSURE
REGULATOR
AND
A
PRESSURE
RELIEF
VALVE
.
T
HE
PRESSURE
RELIEF
VALVE
MUST
BE
SET
TO
OPEN
AT
NO
MORE
THAN
150
PSIG
.
WARNING
Pressure test the system using dry nitrogen and soapy water
to locate leaks. If you wish to use a leak detector, charge the
system to 10 psi using the appropriate refrigerant then use
nitrogen to finish charging the system to working pressure then
apply the detector to suspect areas. If leaks are found, repair
them. After repair, repeat the pressure test. If no leaks exist,
proceed to system evacuation.
S
YSTEM
E
VACUATION
Condensing unit liquid and suction valves are closed to contain
the charge within the unit. The unit is shipped with the valve
stems closed and caps installed.
Do not open valves until
the system is evacuated.
REFRIGERANT
UNDER
PRESSURE!
F
AILURE
TO
FOLLOW
PROPER
PROCEDURES
MAY
CAUSE
PROPERTY
DAMAGE
,
PERSONAL
INJURY
OR
DEATH
.
WARNING
NOTE:
Scroll compressors should never be used to evacuate
or pump down a heat pump or air conditioning system.
P
ROLONGED
OPERATION
AT
SUCTION
PRESSURES
LESS
THAN
20
PSIG
FOR
MORE
THAN
5
SECONDS
WILL
RESULT
IN
OVERHEATING
OF
THE
SCROLLS
AND
PERMANENT
DAMAGE
TO
THE
SCROLL
TIPS
,
DRIVE
BEARINGS
AND
INTERNAL
SEAL
.
CAUTION
1. Connect the vacuum pump with 250 micron capability
to the service valves.
2. Evacuate the system to 250 microns or less using
suction
and
liquid service valves. Using both valves is
necessary as some compressors create a mechanical
seal separating the sides of the system.
3. Close pump valve and hold vacuum for 10 minutes.
Typically pressure will rise during this period.
•
If the pressure rises to 1000 microns or less and remains
steady the system is considered leak-free; proceed to
startup.
•
If pressure rises above 1000 microns but holds steady
below 2000 microns, moisture and/or noncondensibles
may be present or the system may have a small leak.
Return to step 2: If the same result is encountered check
for leaks as previously indicated and repair as necessary
then repeat evacuation.
•
If pressure rises above 2000 microns, a leak is present.
Check for leaks as previously indicated and repair as
necessary then repeat evacuation.
Содержание CONDENSING UNITAIR CONDITIONING
Страница 23: ...23 THISPAGELEFTINTENTIONALLYBLANK...