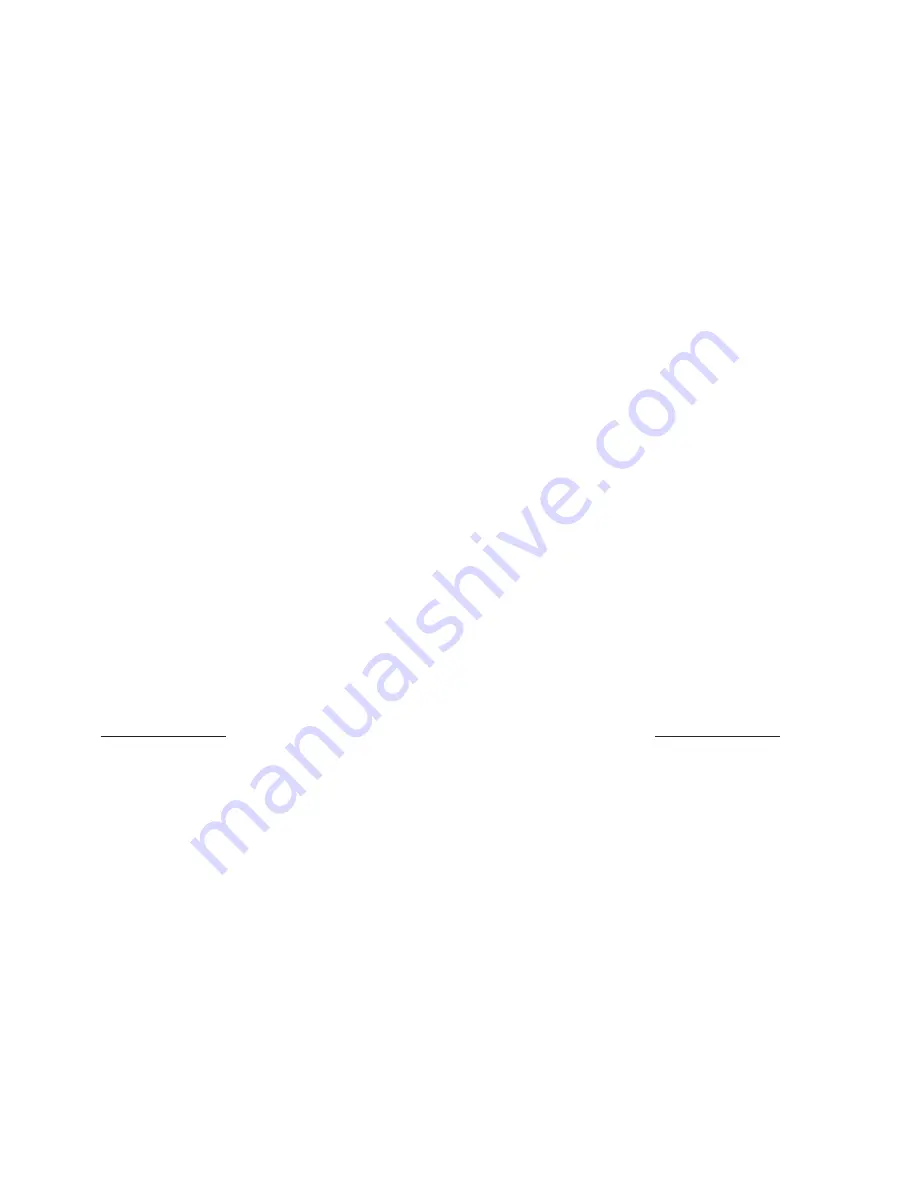
Camshaft timing pulley is also made from die-casting of powder metallurgy with 48 teeth in total. Two dowel pin slots.
During assembly, it is proper to encase the dowel pin slot on the side with “K” mark into the camshaft dowel pin. The
round-hole made in the center of lateral rib with “K” mark should be aligned with the “U” marking on the camshaft bearing
cap when calibrating valve-timing with the camshaft timing belt pulley axially fastened by bolts.
3. Timing belt
With 3-layer structure and 117 teeth in total, the belt is made of butadiene styrene rubber, the mid-layer being polyester
thread with low-expansion and low amount of distortion, and the canvas layer being the synthesis of cotton and synthetic
fiber. It has good heat resistance and abrasive resistance. With low transmit torque, the timing belt has a long life.Normally,
the timing belt shall be replaced after 120, 000 km of use. Meanwhile, in order to avoid teeth run-out in driving, there is a
tensioner on the back of the loosened part of the belt, which can provide a certain pre-tension to the belt. When adjusting
the deflection of toothed belt, it is possible to alter the pre-tension of tension spring by changing the position of tensioner
relative to tightening bolt. After adjustment, fasten the bolts.
4. Camshaft
Engine camshaft is made of the chilling alloy cast iron with an nitrogenized surface. It has high strength and good abrasion
resistance. The split bearing seat without lining is of full supporting structure, featuring good rigidity. On the intake and
exhaust camshaft there are 8 cams and 5 journals. The center to center spacing of intake and exhaust camshaft for each
cylinder is respectively 34mm and 36mm. Axially, It is positioned through single directional shoulder. As driven by bevel
gear, the exhaust camshaft is forced back and the intake camshaft is forced forward. The two forces are equal. The curve
in the section of cam lift consists of buffer and working section, in which wrap angle of exhaust cam buffer section is a little
larger than wrap angle of intake cam buffer, and the wrap angle of exhaust cam working section a little bigger than wrap
angle of intake cam working section. The MR479Q/MR479QA cam base circle is 34mm in diameter, intake cam lift is
7.81mm and exhaust cam lift 8.06mm. The center of camshaft is a main oil passage. Each journal has small holes leading
to the main oil passage so as to lubricate each camshaft journal and bearing seat. There is a groove on the back end of
exhaust camshaft, into which driveshaft of valve timing sensor can be inserted. It thus produces the signal for judgment of
cylinders and sends to ECU so as to carry out identification and control of two different TDC . The structure is simple and
reliable,.
II. Make-up of Valve Train Assembly and its Features
Valve train assy. is used to ensure the cylinder be well sealed.
1. Valve
Valve is one of the important elements to ensure the power, economy, reliability and durability of the engine. Intake valve
is of martensitic steel 4Cr9Si2, with good techniques, abrasion proof, anticorrosion and small expansion coefficient.
Exhaust valve is of austenite steel 5Cr21Mn98Ni4N, with good heat resistance. Its intake and exhaust valves are all
azotized. The intake and exhaust valve are shown as Fig. 200. The big end of intake valve head is 31mm in diameter and
the small end 27.372mm in diameter. The big end of exhaust valve head is 24.5mm in diameter and the small end
21.372mm in diameter. The ntake and exhaust valve employs a bigger Valve cone(45°) to provide a good airtightness. The
intake, valve neck bevel is 10°, with an arc of R6.5 for a transition. It has low intake resistance. Exhaust valve neck bevel
is 25°, and there is a big arc at the valve head and stem tip for a transition. It has a high rigidity.
The intake valve lift/diameter ratio is 0.252, the exhaust valve lift/diameter ratio is 0.329. The bottom of valve is flat and
valve stem is 6mm in diameter. The lateral force is large. The intake valve has a full length of 87.5±0.1mm and exhaust
valve has a full length of 87.5±0.15mm. Lock groove sinks in the form of arc. During assembly, keeper is embedded in form
of being raised on the stem lock groove. It can reliably lock the valve spring.
87
Содержание JL481Q
Страница 1: ......
Страница 9: ...5 Fig 3 Components Assembly Drawing of MR479Q MR479QA Engine ...
Страница 10: ...6 Fig 4 MR479Q MR479QA Engine and Its Power System ...
Страница 11: ...7 Fig 5 Assembly Drawing of Engine and Its Auxiliaries MR479Q MR479QA ...
Страница 12: ...8 Fig 6 Electronic Control Fuel Injection System in Engine MR479Q MR479QA ...
Страница 13: ...9 Fig 7 Front view of Engine JL481Q MR481QA ...
Страница 14: ...10 Fig 8 Sectional elevation of Engine JL481Q MR481QA ...
Страница 15: ...11 Fig 9 Electronic Control Fuel Injection System in Engine JL481Q MR481QA ...
Страница 21: ...17 Fig 13 Exterior Feature of JL481Q Engine Power Me N m Torque Pe Kw ge g kwh Fuel Consumption Ratio ...