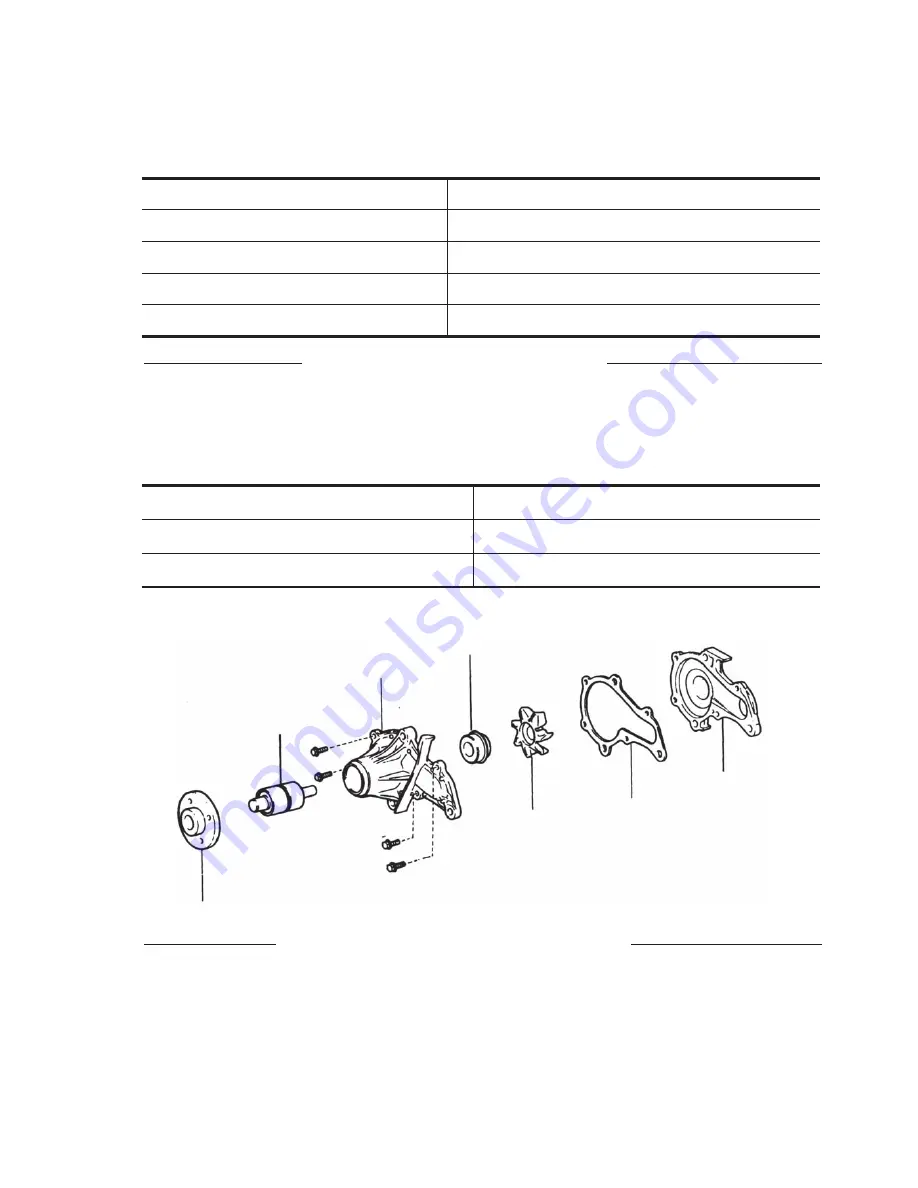
Bearing
pullry
Pump body
Water-sead compo
Rotor
Gacket
Cover of intake valve
The water pump of engine is a centrifugal vane one. The pump pressurizes the coolant and makes coolant circulatied in
line of the system design.
The pump body is made of aluminum alloy, aimed to be more corrosion-proof. The pump is driven by belt connected with
crankshaft pulley. The size of pump is shown on Table 17.
The pump is composed of pulley seat, bearing, pump body, water-seal compo, rotor, gasket, cover of suction port (Fig.
317), etc.
II. Structure & Features of Water Pump
Engine adopts wax-type single valve thermostat. Its size is shown on Table18, while its structure is shown on Fig. 318 and
319.
The thermostat is located inside the body of water intake end, interconnected with cylinder’s jacket. The upper end of rod
4 is fixed on support 3, while its lower end is inserted into rubber boot 5. Both rubber sheet 5 and body1 is filled with wax
7. If coolant temperature is lower than 80°C, wax will be solidified and valve 6 will be pressed to close via spring 2.Thus
coolant will directly flow into cylinder’s cooling jacket via bypass valve 10
III. Structure & Features of thermostat
Fig. 317 Pump Assy.
Table 16
Table 17
Centrifugal
100 (pump speed 3000r/min)
60
MR479Q engine
5.3 (total volume of coolant, 0.9 of which is
the capacity of radiator)
158 (when the fan power is 1kw)
5.5
388 x 350 x 32
Item
Water capacity of radiator (L)
Radiation efficiency (kJ/h)
Radiation area (m2)
Size of the radiator core (W X H X T) (mm)
Model
Output volume (L/min)
Vane diameter (mm)
Specification of MR6370
Specification of water pump
144
Содержание JL481Q
Страница 1: ......
Страница 9: ...5 Fig 3 Components Assembly Drawing of MR479Q MR479QA Engine ...
Страница 10: ...6 Fig 4 MR479Q MR479QA Engine and Its Power System ...
Страница 11: ...7 Fig 5 Assembly Drawing of Engine and Its Auxiliaries MR479Q MR479QA ...
Страница 12: ...8 Fig 6 Electronic Control Fuel Injection System in Engine MR479Q MR479QA ...
Страница 13: ...9 Fig 7 Front view of Engine JL481Q MR481QA ...
Страница 14: ...10 Fig 8 Sectional elevation of Engine JL481Q MR481QA ...
Страница 15: ...11 Fig 9 Electronic Control Fuel Injection System in Engine JL481Q MR481QA ...
Страница 21: ...17 Fig 13 Exterior Feature of JL481Q Engine Power Me N m Torque Pe Kw ge g kwh Fuel Consumption Ratio ...