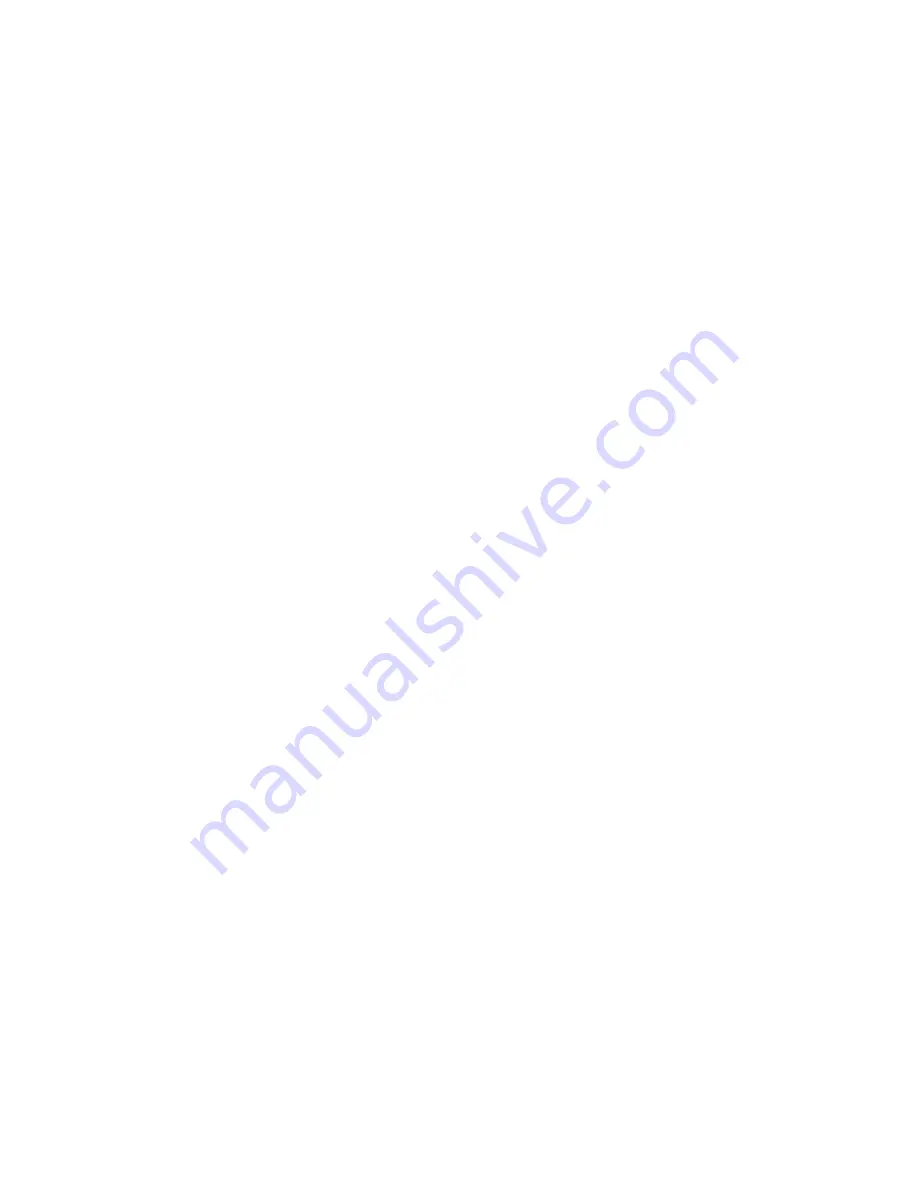
26
Interrupt error
An unused interrupt has occurred
Switch off the drive and restart
If still unsuccessful, the fault is probably internal. Contact your service office
Module overtemp
(For sizes from 1 Hp to 20 Hp). Temperature of the IGBT module is too high
Failure of drive fan
Failure in the IGBT module in the power section.
Fast overload current duty cycle.
Output stages
Internal Overcurrent failure of IGBT power section
Switch off drive and restart
If unsuccessful, contact your service office
Overcurrent
Overcurrent in the motor circuit
Short-circuit or ground fault at the output of the drive
Current regulator tuned incorrectly
Message appears when switching on the drive: drive is connecting to a motor
that is running. Auto capture function must be activated
Switch off drive and restart
If unsuccessful, contact your service office
Overvoltage
Overvoltage on the DC Bus due to energy regenerated from motor
Lengthen deceleration ramp. If not possible:
Use a BU... braking unit to increase the energy absorption capability
Overtemp Motor
Overtemperature of the motor (indicated via thermistor on terminals 78/79)
Cable between thermistor in motor and terminals 78 and 79 interrupted
Overheating of motor:
- Load cycle too extreme
- Ambient temperature at motor location too high
- Motor has an external blower and it has failed
- Motor does not have an external blower: load too large at low speeds. The cooling effect
of the fan on the motor shaft is inadequate for this load cycle. Change cycle or install an
external blower
Regulation ot
Temperature of the drive regulator card is too high
Ambient temperature too high
Speed fbk loss
Speed feedback loss
Encoder not connected, or incorrectly connected or not supplied:
Select the
Enc 1 speed
parameter in the MONITOR\ Measurement \ Speed \ Speed in rpm
menu.
- With the drive disabled, manually turn the motor clockwise (viewed from the front of the
shaft). The value indicated must be positive.
- If the indicated value does not change or random values are shown, check the power
supply and the cabling of the encoder.
- If the indicated value is negative, reverse the encoder connections. Exchange channel
A+ and A- or B+ and B-
Содержание AV-300i
Страница 1: ...1 GE Industrial Systems AV 300i AV 300i Quick Start Up Guide TM...
Страница 16: ...16 Moving inside a menu...