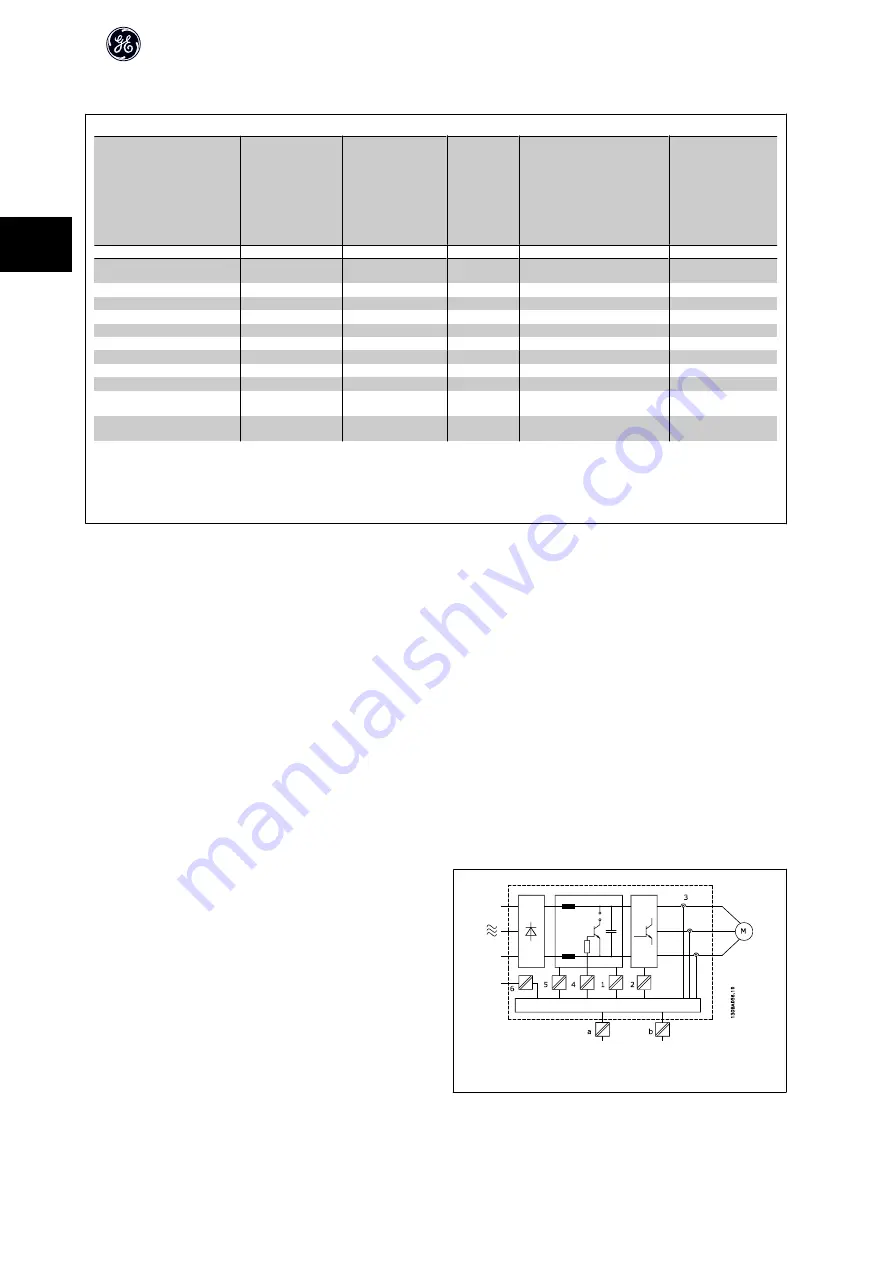
EMC immunity form
Voltage range: 200-240 V, 380-480 V
Basic standard
Burst
IEC 61000-4-4
Surge
IEC 61000-4-5
ESD
IEC 61000-4-2
Radiated electromagnetic field
IEC 61000-4-3
RF common
mode voltage
IEC 61000-4-6
Acceptance criterion
B
B
B
A
A
Line
4 kV CM
2 kV/2
Ω
DM
4 kV/12
Ω
CM
—
—
10 V
RMS
Motor
4 kV CM
4 kV/2
Ω
1)
—
—
10 V
RMS
Brake
4 kV CM
4 kV/2
Ω
1)
—
—
10 V
RMS
Load sharing
4 kV CM
4 kV/2
Ω
1)
—
—
10 V
RMS
Control wires
2 kV CM
2 kV/2
Ω
1)
—
—
10 V
RMS
Standard bus
2 kV CM
2 kV/2
Ω
1)
—
—
10 V
RMS
Relay wires
2 kV CM
2 kV/2
Ω
1)
—
—
10 V
RMS
Application and network options
2 kV CM
2 kV/2
Ω
1)
—
—
10 V
RMS
Keypad cable
2 kV CM
2 kV/2
Ω
1)
—
—
10 V
RMS
External 24 V DC
2 kV CM
0.5 kV/2
Ω
DM
1 kV/12
Ω
CM
—
—
10 V
RMS
Enclosure
—
—
8 kV AD
6 kV CD
10 V/m
—
AD: Air Discharge
CD: Contact Discharge
CM: Common mode
DM: Differential mode
1. Injection on cable shield.
Table 3.2: Immunity
3.6.1 PELV - Protective Extra Low Voltage
PELV offers protection by way of extra low voltage. Protection against electric shock is ensured when the electrical supply is of the PELV type and the installation
is made as described in local/national regulations on PELV supplies.
All control terminals and relay terminals 01-03/04-06 comply with PELV (Protective Extra Low Voltage) (Does not apply to grounded Delta leg above 400 V).
Galvanic (ensured) isolation is obtained by fulfilling requirements for higher isolation and by providing the relevant creapage/clearance distances. These require-
ments are described in the EN 61800-5-1 standard.
The components that make up the electrical isolation, as described below, also comply with the requirements for higher isolation and the relevant test as described
in EN 61800-5-1.
The PELV galvanic isolation can be shown in six locations (see illustration):
In order to maintain PELV all connections made to the control terminals must be PELV, e.g. thermistor must be reinforced/double insulated.
1.
Power supply (SMPS) incl. signal isolation of U
DC
, indicating the in-
termediate current voltage.
2.
Gate drive that runs the IGBTs (trigger transformers/opto-couplers).
3.
Current transducers.
4.
Opto-coupler, brake module.
5.
Internal inrush, RFI, and temperature measurement circuits.
6.
Custom relays.
Illustration 3.3: Galvanic isolation
The functional galvanic isolation (a and b on drawing) is for the 24 V back-up option and for the RS 485 standard bus interface.
AF-650 GP Design Guide
38
3
Содержание AF-650 GP Series
Страница 5: ...AF 650 GP Design Guide 4 1...
Страница 53: ...AF 650 GP Design Guide 52 4...
Страница 97: ...Please note airflow directions 6 1 5 Mechanical Dimensions AF 650 GP Design Guide 96 6...
Страница 98: ...Please note airflow directions AF 650 GP Design Guide 97 6...
Страница 99: ...Please note airflow directions AF 650 GP Design Guide 98 6...
Страница 100: ...Please note airflow directions AF 650 GP Design Guide 99 6...
Страница 173: ...Max cable length 150 m AF 650 GP Design Guide 172 9...
Страница 179: ...AF 650 GP Design Guide 178 9...