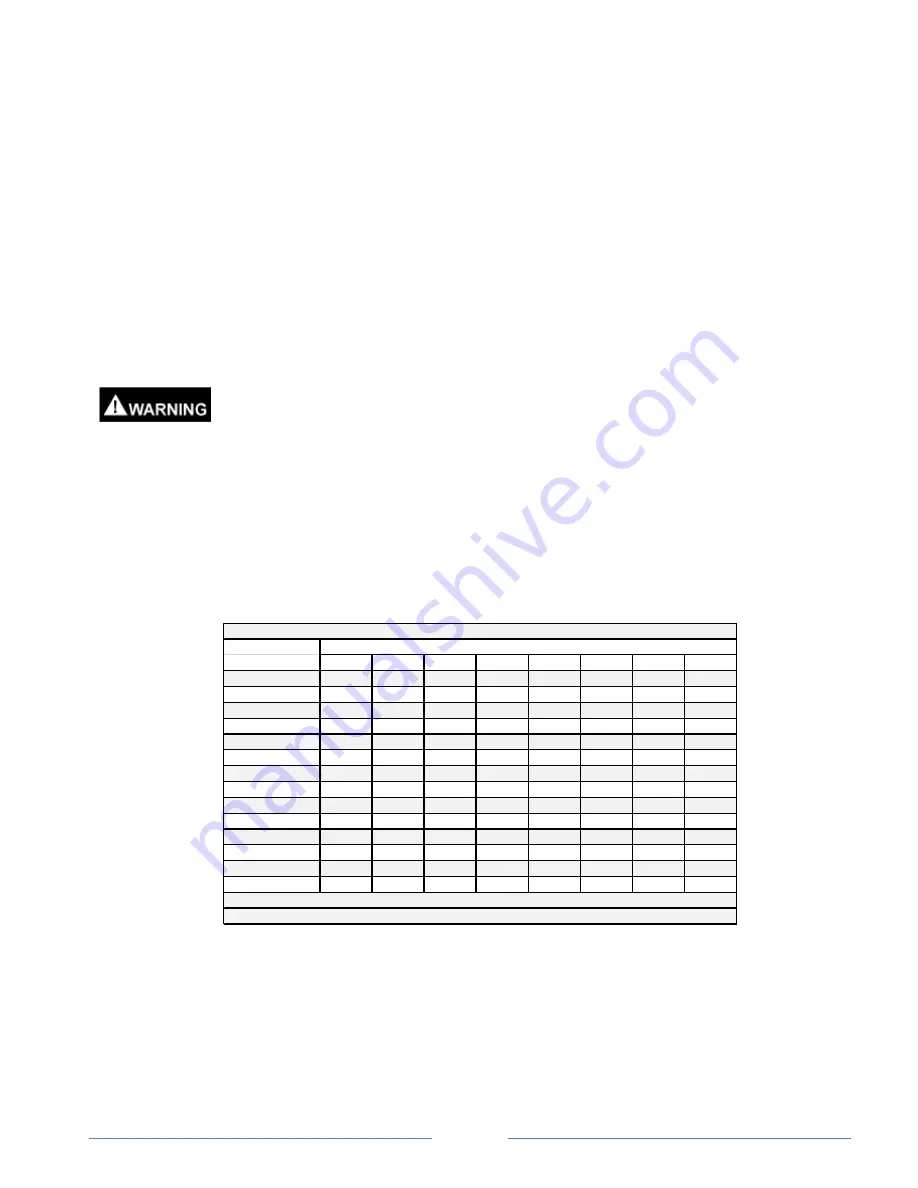
Page 8
mounted in the lower half of the storage tank. Boiler temperature controls are typically mounted in the primary
loop. If the temperature control sensor is mounted directly on the heater/boiler water piping, the sensor must be
installed on the inlet water piping to prevent short cycling of the appliance.
A water flow switch must be installed by the installer and wired to prevent the unit from firing if for any reason
there is an inadequate flow of water through the boiler/heater (see wiring diagrams for suggested location in the
electrical circuit).
NOTE: CSD-1 model boilers only, are equipped with a factory installed operating
aquastat.
Optional, circulation pumps can be supplied for single or three phase and 115 to 460 volts as required. The
pump power must be wired independently and should be adequate for the amp rating of the pump motor. Refer
to the Operating Instructions and Wiring Diagrams sections of this manual for more information regarding
pumps.
GAS REQUIREMENTS
Ensure the fuel the appliance will burn is the same as that specified on the boiler
rating plate. Conversions must be completed by a Qualified Service Agency or Gas
Provider. Call your Green Boiler Technologies Representative or Customer Service
for instructions and the proper conversion kit.
The gas supply meter, regulator, and piping must have sufficient capacity to supply all gas fired appliances they
feed without undue pressure loss. If the gas meter, regulator or piping is too small, request the gas company
install equipment with adequate capacity.
The allowable pressure loss in gas piping between the gas meter or service regulator and each appliance is
generally between 0.3 to 0.5 inches of water column. Refer to the National Fuel Gas Code, ANSI Z223.1, Latest
Edition, for sizing guidelines.
Example:
For 20 equivalent feet of 1-1/2 inch piping, the maximum cuft/hr gas flow with a 0.3 inch w.c.
pressure loss is 726. For natural gas at 1025 Btu/cuft, the maximum firing rate is 744,000 Btu/hr
[726 x1025]. For propane at 2500 Btu/cuft, the maximum firing rate is 1,815,000 Btu/hr [726 x
2500].
Maximum and minimum gas pressure delivered to the boiler/heater is shown below. If the gas supply line
pressure is greater than the maximum listed, a pressure regulator must be installed at least 10 pipe diameters
upstream of the boiler/heater.
Max Length
(Equivalent feet)
3/4
1
1-1/4
1-1/2
2
2-1/2
3
4
10
273
514
1060
1580
3050
4860
8580
17500
20
188
353
726
1090
2090
3340
5900
12000
30
151
284
583
873
1680
2680
4740
9660
40
129
243
499
747
1440
2290
4050
8270
50
114
215
442
662
1280
2030
3590
7330
60
104
195
400
600
1160
1840
3260
6640
70
95
179
368
552
1060
1690
3000
6110
80
89
167
343
514
989
1580
2790
5680
90
83
157
322
482
928
1480
2610
5330
100
79
148
304
455
877
1400
2470
5040
125
70
131
269
403
777
1240
2190
4460
150
63
119
244
366
704
1120
1980
4050
175
58
109
224
336
648
1030
1820
3720
200
54
102
209
313
602
960
1700
3460
Gas Pipe Sizing Chart: Cubic Feet of Gas Per Hour
Size Schedule 40 Metal l ic Pipe (i nches)
Ta bl e Va l ue s For Na tura l Ga s , Spe ci fi c Gra vi ty 0.60
Typical Natural Gas = 1025 Btu per cuft ; Typi cal Propane = 2,500 btu/cuft
Содержание A2-035
Страница 30: ...Page 29 DIAGRAMS...
Страница 31: ...Page 30...
Страница 33: ...Page 32 WIRING DIAGRAM A2000 Water Heater Models...
Страница 34: ...Page 33 WIRING DIAGRAM A2000 Boiler Models...
Страница 35: ...Page 34 WIRING DIAGRAM A2000 CSD 1 Boiler Models...
Страница 36: ...Page 35 A2000 WITH CONSTANT PUMP OPERATION A2000 WITH ON OFF PUMP OPERATION...
Страница 37: ...Page 36 A2000 WITH INFITEC PUMP DELAY...
Страница 38: ...Page 37 A2000 PARTS LIST 1 17 19 15 23 22 21 20 18 16 4 2 Gas Train Components Differ By Model 7 14 5...
Страница 44: ......