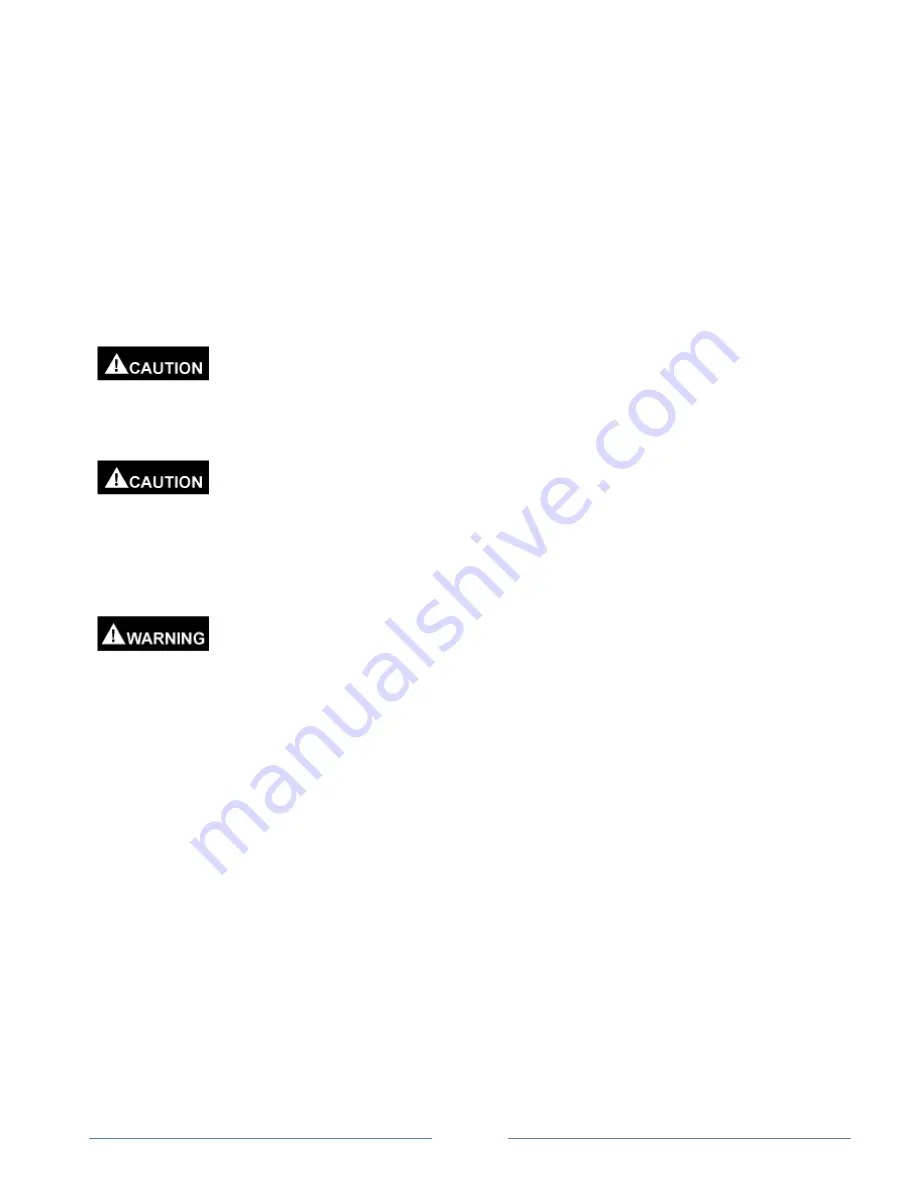
Page 23
o
Smoke Test – Place a source of smoke or other visible fumes below the opening of the draft
hood. If the fumes are all drawn up the draft hood opening, the appliance is drafting properly. If
any fumes roll outside of the vent hood there is a problem with the drafting or make-up air.
o
Draft Gauge – A draft pressure gauge can be inserted into the vent pipe directly above the draft
hood. The draft gauge must show a constant negative pressure.
Any improper operation of common venting systems should be corrected so the installation conforms to
the National Fuel Gas Code, ANSI-Z223.1, Latest Edition. When any portion of the venting system is
changed it must conform to the National Fuel Gas Code, ANSI-Z223.1, Latest Edition.
Burner & Flue Passageway:
Do not allow the burner, burner orifices, or the floor shield to accumulate foreign
matter. Clean periodically by brushing or blowing any dust or debris from the area. Orifices should be checked
for size and reamed as required. The flue gas passageway can be cleaned by simply sliding the burner out and
flushing the finned tubing with water.
Before disconnecting the burner, be sure to shut off all gas valves and electrical
switches then let cool for 30 minutes. After cleaning, reinstall the burner. Water must
be circulating before turning on the gas valve to prevent heat exchanger damage.
Pressure Relief Valve:
A pressure relief valve is supplied on the outlet of the heat exchanger. The relief valve
should be tested at least annually by lifting the test handle.
When testing the valve extremely hot water and/or steam may be released.
High Temperature Switch:
The manual reset High Temperature switch, located in the water outlet piping,
should be checked annually for proper function. To test the switch, slowly close the valve in the water outlet
piping until the water temperature exceeds the set point of the switch. The temperature switch should open
before the water temperature reaches 210
o
F (99
o
C) for a water heater, and 250
o
F (121
o
C) for a boiler. Note:
The operating thermostat and/or flow switch may have to be temporarily by-passed in order to conduct this test.
Ensure all operating and safety controls are put back into proper operation before
putting the heater/boiler back into service.
Flow Switch:
The water Flow Switch should be checked annually for proper function. To test the Flow Switch,
slowly close the valve in the water outlet piping until the temperature rise through the heat exchanger
approaches 100
o
F (55
o
C). The Flow Switch should open before the temperature rise exceeds 105
o
F (58
o
C).
Refer to the OPERATION Section of this manual for more information regarding the water Flow Switch.
Heat Exchanger Protection:
Either very soft or very hard water will shorten the life of the heat exchanger. The
water to be heated should be between 5 and 15 grains per gallon. Harder water should be softened to prevent
scaling, reduced efficiency and ultimately melting the heat exchanger. Softer water must have buffers added to
prevent erosion of the heat exchanger.
NOTE: FAILURE TO PROPERLY OBSERVE THE ABOVE WILL VOID
THE WARRANTY AND MAY RESULT IN A VERY SHORT LIFE OF THIS BOILER/HEATER.
Condensation:
Condensation of the flue gas may result if the inlet water temperature is under 120° F.
Condensation will form on the outside of the heat exchanger and drip down onto the burner and possibly the
floor below the heater/boiler, often mistaken for a leaking coil. After the boiler has been in operation long
enough for the temperature of the water in the system to reach 120° F, the condensation will stop dripping from
the heat exchanger. The A2000 and the venting connected to it are not designed to withstand repeated
condensation. Low operating temperatures and frequent cold start-ups must be prevented. Frequent operation
below 120°F return water temperature will damage the heat exchanger and void the warranty. If low operating
temperatures cannot be avoided, a feedback loop (by-pass) must be installed as shown in the DIAGRAMS
section.
Noise During Operation:
Knocking sounds produced by the heater/boiler may indicate scale build-up in the
heat exchanger waterway. De-liming is recommended. Scale thickness as thin as 1/16 inch can increase fuel
consumption by 15%. Refer to procedure provided with de-liming kit part number W3700001. Extended
operation with a scaled heat exchanger may cause early heat exchanger failure and will void warranty.
Содержание A2-035
Страница 30: ...Page 29 DIAGRAMS...
Страница 31: ...Page 30...
Страница 33: ...Page 32 WIRING DIAGRAM A2000 Water Heater Models...
Страница 34: ...Page 33 WIRING DIAGRAM A2000 Boiler Models...
Страница 35: ...Page 34 WIRING DIAGRAM A2000 CSD 1 Boiler Models...
Страница 36: ...Page 35 A2000 WITH CONSTANT PUMP OPERATION A2000 WITH ON OFF PUMP OPERATION...
Страница 37: ...Page 36 A2000 WITH INFITEC PUMP DELAY...
Страница 38: ...Page 37 A2000 PARTS LIST 1 17 19 15 23 22 21 20 18 16 4 2 Gas Train Components Differ By Model 7 14 5...
Страница 44: ......