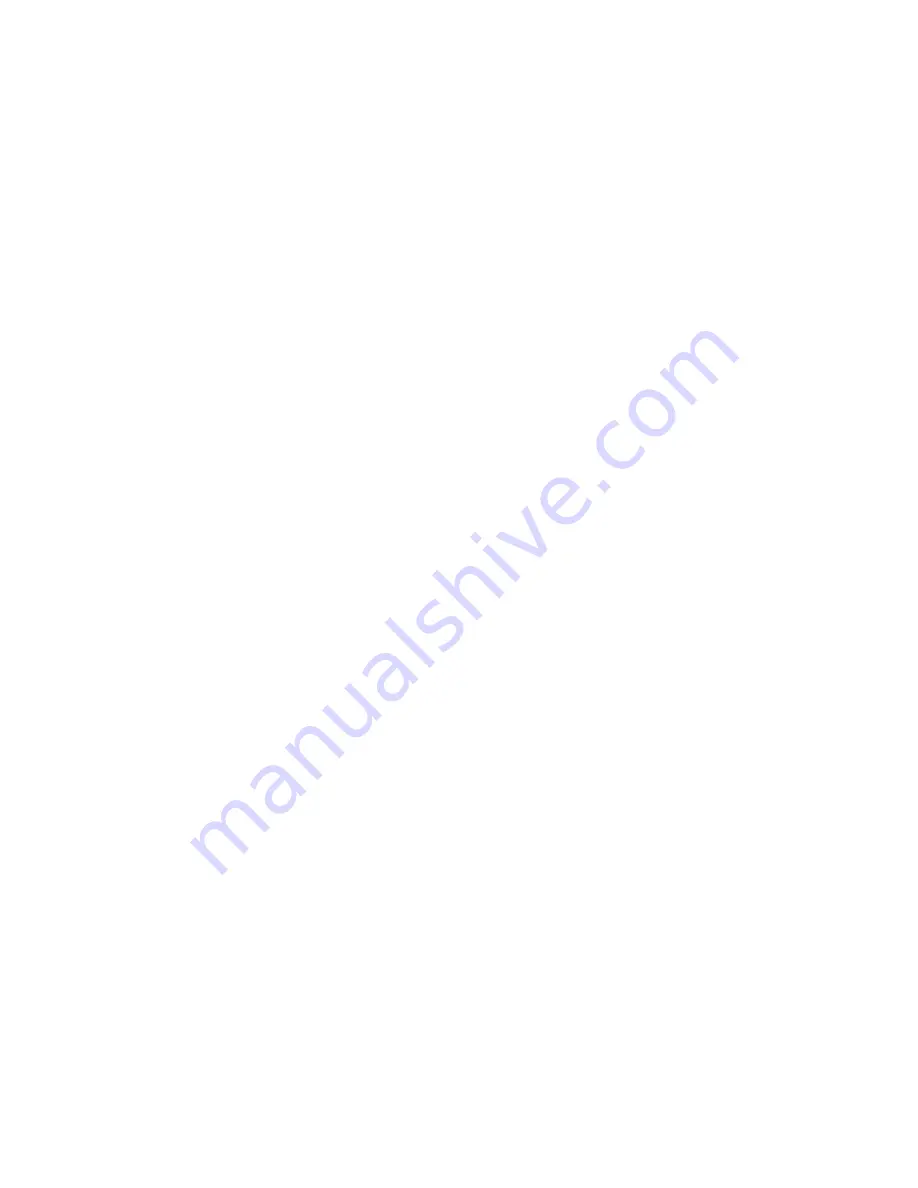
13-8-639 Page 67
SYMPTOM
POSSIBLE CAUSE
REMEDY
High discharge air
temperature
1.
Dirty or clogged cooler
face.
1.
Clean cooler.
2.
Insufficient cooling air
flow.
2.
Provide unrestricted
supply of cooling air.
3.
Clogged oil filter or cooler
(interior).
3.
Replace filter or clean
cooler.
4.
Low compressor oil.
4.
Add oil to proper level.
5.
Faulty temperature
sensor.
5.
Replace sensor.
6.
Thermostatic mixing valve
stuck open .
6.
Repair or replace valve.
7.
High ambient temperature
7.
Provide sufficient flow of
ambient air.
8.
Air guide for fan installed
wrong.
8.
Check concentricity of the
air guide & fan. Also the
distance from the fan to
the air guide is .04-.16
inches (1-4mm).
High Discharge Pressure
1.
Inlet valve solenoid valve
faulty.
1.
Replace solenoid valve.
2.
Air service valve closed.
2.
Open air service valve.
3.
Inlet valve plate seal is
leaking.
3. Replace
4.
Aftercooler is frozen.
4.
Thaw out. This machine
cannot operate in
temperature below 32
°
F
(0
°
C).
5.
Faulty blowdown valve
piston.
5. Replace
piston.
Excessive oil
consumption
1.
Oil carryover through
lines.
1.
See “Oil Carryover”, in this
section.
2.
Oil leaks at all fittings and
gaskets.
2.
Tighten or replace fittings
or gaskets.
3.
Shaft seal leaking.
3.
Replace shaft seal.
Oil carryover
1.
Overfilling the reservoir.
1.
Drain excess oil from
system.
2.
Clogged, broken or loose
oil return lines. Scavenge
line orifices or check valve
clogged.
2.
Tighten or replace faulty
lines, clean or replace
faulty orifice plate.
3.
Ruptured oil separator
element.
3.
Replace element.
4.
Oil separator clogged.
4.
Replace element.
5.
Loose assembly.
5.
Tighten all fittings and
gaskets.
Содержание INTEGRA EFA99F
Страница 15: ...13 8 639 Page 15 Figure 2 2 OUTLINE UNIT PACKAGE 300EFA804 A Ref Drawing ...
Страница 39: ...13 8 639 Page 39 WIRING DIAGRAMS 3 PHASE ...
Страница 40: ...13 8 639 Page 40 WIRING DIAGRAMS 3 PHASE ...
Страница 41: ...13 8 639 Page 41 WIRING DIAGRAMS 3 PHASE ...
Страница 42: ...13 8 639 Page 42 WIRING DIAGRAMS 1 PHASE ...
Страница 43: ...13 8 639 Page 43 WIRING DIAGRAM 1 PHASE ...
Страница 44: ...13 8 639 Page 44 WIRING DIAGRAM 1 PHASE ...