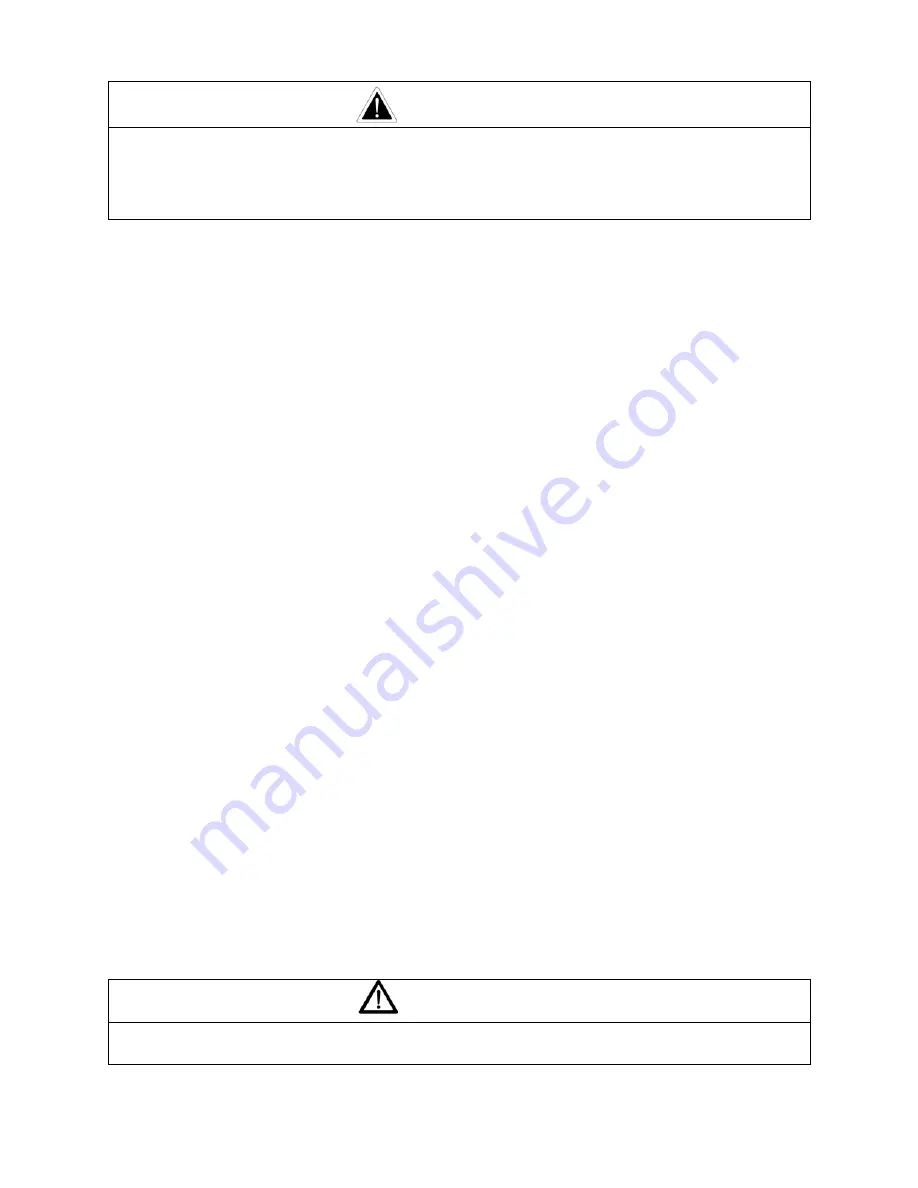
13-8-639 Page 36
DANGER
Air/oil under pressure will cause severe personal injury or death. Shut down
compressor, relieve system of all pressure, disconnect, lockout and tagout
power supply to the starter before removing valves, caps, plugs, fittings, bolts
and filters.
Inlet Valve
– The inlet valve opens and closes to control delivery and closes to unload the compressor.
At shutdown, the inlet valve closes to prevent the back flow of air.
The inlet valve position is controlled by air pressure, which is controlled by the AIRPILOT ELECTRONIC
CONTROLLER, through the inlet valve solenoid. When the discharge pressure reaches the unload
pressure programmed into the controller, the inlet solenoid valve de-energizes, allowing system pressure
below the inlet valve piston, through the shuttle valve, closing the inlet valve, The compressor runs
unloaded for the pre-set time programmed into the controller or until the system pressure reaches the
load pressure. When the system pressure reaches the load pressure programmed into the controller, the
inlet solenoid valve is energized. After a 2 second delay, the inlet valve solenoid allows pressure out from
below the inlet valve piston. A partial vacuum is formed in the inlet line, the inlet valve opens and the
compressor runs loaded.
The inlet valve does not require adjustment. If the valve fails to function, check the valve for dirt or burrs,
and if the o-rings or seals are worn. See the Parts List for a listing of the kits available for rebuilding or
replacing the valve. The seals will need to be replaced periodically. The interval will depend on the
environment and the operating conditions. Repair kits are available from your local authorized Gardner
Denver distributor.
Inlet Valve Solenoid
(Figure 4-4, page 37) – This valve controls the position of the inlet valve in
response to signals from the controller. When the inlet solenoid valve is energized, after a delay of 2
seconds, it allows the pressure to escape from below the inlet valve piston. A partial vacuum is formed in
the inlet line, the inlet valve opens and the compressor runs loaded. When the inlet solenoid valve is de-
energized, it allows system pressure under the inlet valve piston, through the shuttle valve, closing the
inlet valve.
Blowdown Solenoid Valve
(Figure 4-4, page 37) – This valve is normally used for control functions, but
also serves to relieve air/oil reservoir pressure following a shutdown. The blowdown solenoid valve de-
energizes, opening the blowdown line from the air/oil separator housing, whenever the inlet valve
solenoid de-energizes and closes the inlet valve or whenever the machine is shutdown. The blowdown
solenoid valve energizes to close the blowdown valve when the inlet solenoid valve opens the inlet valve.
Shuttle Valve
(Figure 4-4, page 37) – This valve, also known as a double check valve, is a device which
will take two (2) supply signals and allow the one with the highest pressure to pass through. The shuttle
valve is used to provide control air pressure from either the reservoir or plant air system, as required
during different operating conditions.
Isolation Switch for Motor Power
– This switch disconnects power to the motor if the side panels and
the top panels are not in place.
The control circuit will remain energized.
WARNING
Electrical shock can cause injury or death. Open main disconnect switch,
lockout and tagout before working on control box.
Содержание INTEGRA EFA99F
Страница 15: ...13 8 639 Page 15 Figure 2 2 OUTLINE UNIT PACKAGE 300EFA804 A Ref Drawing ...
Страница 39: ...13 8 639 Page 39 WIRING DIAGRAMS 3 PHASE ...
Страница 40: ...13 8 639 Page 40 WIRING DIAGRAMS 3 PHASE ...
Страница 41: ...13 8 639 Page 41 WIRING DIAGRAMS 3 PHASE ...
Страница 42: ...13 8 639 Page 42 WIRING DIAGRAMS 1 PHASE ...
Страница 43: ...13 8 639 Page 43 WIRING DIAGRAM 1 PHASE ...
Страница 44: ...13 8 639 Page 44 WIRING DIAGRAM 1 PHASE ...