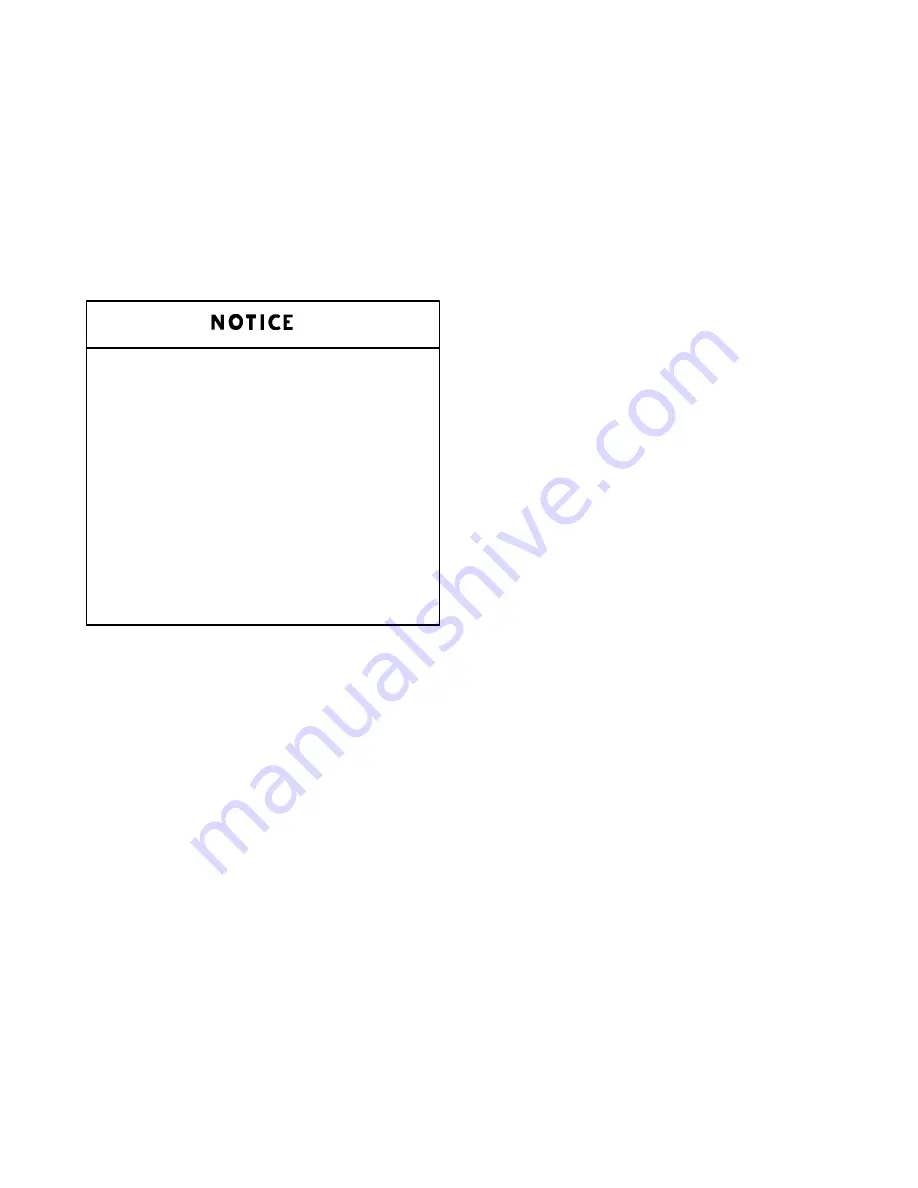
13–10–613 SP Page 27
control system will operate only as many compressors
as are needed to supply the CFM demand of the plant,
and to maintain the compressor system pressure be-
tween the SET and RESET pressures programmed
into the controllers.
The ES+ controllers are completely set up to operate
this system. The only required additional part is the
cable which runs from controller to controller. A kit,
200EAP752, is available which contains all material
needed to sequence up to five compressors. This kit
contains 500 feet of cable, eight modular connectors,
and a crimping tool to install the connectors.
Though similar in operation and in–
stallation, this sequencing system is
designed to take advantage of all of
the internal features of the ES+ con-
troller. Communications cables should
not be connected to compressor units
with ES controllers part number
201EAP1173 or 202EAP1173. Multiple
compressors with each type control-
ler may be operated as independent
groups piped to the same plant de-
mand.
In spite of the fact that it is a standard feature and its
inherent installation simplicity, the sequencing function
of a multi–compressor “AUTO SENTRY–ES+” system
is the most fully–featured, functionally–complete avail-
able today.
Compressor System – A proper sequencing installa-
tion requires two or more Gardner–Denver rotary air
compressors complete with “AUTO SENTRY–ES+”
controllers, piped into a common air system, intercon-
nected as described above. For best performance,
connect the units directly to a common header and re-
ceiver, without any intervening dryers, filters, or other
restrictions. If any equipment must be installed on indi-
vidual compressors, select equipment with minimum
pressure drop. If filters are installed, establish a mainte-
nance procedure to prevent clogging filters from upset-
ting the system. There should be no check valves or
other devices which isolate a member from the air sys-
tem. During operation, be sure that any unit is taken out
of the sequence mode before closing its service valve.
The receiver should also be sized to prevent excessive
drops or rapid rises in pressures during the operation
as described below. Note that “receiver” really applies
to the entire storage volume of a physical receiver and
the volume of the air distribution throughout the plant.
Modulating systems work best when the receiver is at
least one gallon for the rated CFM of a member com-
pressor in the system (the largest if they differ). If the
system is operated load–unload, larger volume or wid-
er differential may be needed to prevent unnecessary
starts or rapid compressor cycles. Note that when de-
mand exceeds the capacity of the running unit(s), there
will be a delay until the next unit starts and delivers
additional air. The stored air serves the plant during
this period. With a properly sized receiver, pressure
changes on a receiver gauge should be very slow and
gradual.
All standard practices common to sound air compres-
sor installations such as proper sizing of piping, proper
electrical supply and conductor sizing, and grounding
are to be observed. Run the compressors in the sys-
tem in Automatic mode for at least one week to evalu-
ate system performance.
Sequencing Installation – Once the compressor sys-
tem is set up, sequencing compressors with the AUTO
SENTRY–ES+ controller is as simple as plugging in a
telephone to a wall jack. The only item required to
make the system functional is a cable similar to a
phone cable. The cable and connectors used in kit
200EAP752 have been specially selected to meet the
needs of an industrial application. One less cable than
the number of compressors to be sequenced is re-
quired. For example, to sequence four compressors,
three cables are required.
The serial communications interface meets RS–485
standards, the most widely used interface in harsh, in-
dustrial environments today. However, the commu-
nications cables should be routed through metallic con-
duit to provide them with both mechanical protection
and electromagnetic shielding. Do not run the commu-
nications cable in a conduit with other wiring.
Each controller has two modular jacks which accept
RJ–12 telephone plugs. One jack is vacant, the other
has a short pigtail plugged into it. To interconnect two
compressors, plug the cable into the vacant jack on
each controller. For installations of more than two
units, the pigtail plug must be disconnected on all con-
trollers except the two at each end of the communica-
tions line. The order of interconnection has no effect on
the system operation. The following conditions are
necessary and sufficient for proper operation:
1.
Every compressor must have a cable connecting
it to another compressor. One less cable than the
number of units sequenced must be used.
2.
Each board that has only one cable connected to
it must have its pigtail plugged into the unused
jack. All installations will have two such units.
Содержание ELECTRA-SAVER EAYQ E
Страница 15: ...13 10 613 SP Page 6 DECALS 206EAQ077 212EAQ077 218EAQ077 211EAQ077 207EAQ077 ...
Страница 16: ...13 10 613 SP Page 7 DECALS 216EAQ077 217EAQ077 222EAQ077 221EAQ077 208EAQ077 ...
Страница 31: ...13 10 613 SP Page 22 FIGURE 4 2 FLOW CHART FOR SET UP PROGRAMMING ...
Страница 45: ...13 10 613 SP Page 36 FIGURE 4 10 CONTROL SCHEMATIC COMPRESSOR AT FULL LOAD 204EAY797 Ref Drawing ...
Страница 48: ...13 10 613 SP Page 39 FIGURE 4 13 WIRING DIAGRAM 202EAY546 Ref Drawing ...
Страница 75: ......