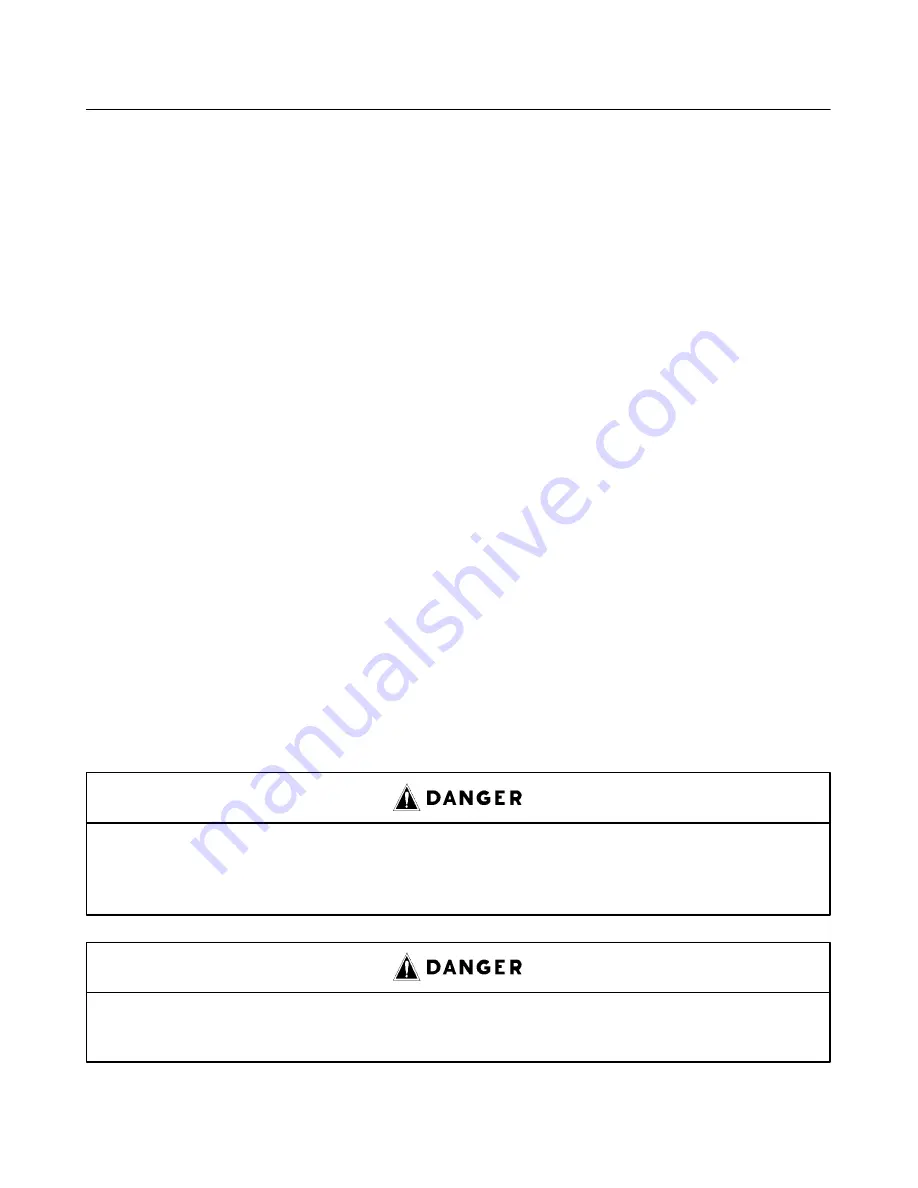
13–10–613 SP Page 56
SYMPTOM
POSSIBLE CAUSE
REMEDY
Compressor is low on
1.
Restricted air filter.
1.
Clean or replace filter.
delivery and pressure.
2.
Sticking inlet valve.
2.
Inspect and clean inlet
valve.
3.
Unload pressure adjusted
3.
Adjust the unload pressure.
too low.
See Section 4, page 33.
4.
Minimum pressure valve
4.
Disassemble and clean
stuck closed.
valve.
5.
Turn valve adjustment or
5.
Adjust turn valve per
malfunction.
Section 4, page 33.
High discharge air
1.
Thermostatic mixing
1.
Repair or replace valve.
temperature.
valve stuck open.
2.
Dirty or clogged cooler face.
2.
Clean cooler.
3.
Insufficient cooling
3.
Provide unrestricted supply
air flow.
of cooling air.
4.
Clogged oil filter or
4.
Replace filter or clean
cooler (interior).
cooler.
5.
Low compressor oil.
5.
Add oil to proper level.
Excessive Oil Consumption
1.
Oil carryover through lines.
1.
See “Oil Carryover”, below.
2.
Oil leaks at all fittings
2.
Tighten or replace fittings
and gaskets.
or gasket.
Oil Carry–Over
1.
Overfilling the reservoir.
1.
Drain excess oil from
system.
Air/oil under pressure will cause severe personal injury or death. Shut down com-
pressor, relieve system of all pressure, disconnect, tag and lockout power supply
to the starter before removing valves, caps, plugs, fittings, bolts, and filters.
Compressor, air/oil reservoir, separation chamber and all piping and tubing may
be at high temperature during and after operation.
Содержание ELECTRA-SAVER EAYQ E
Страница 15: ...13 10 613 SP Page 6 DECALS 206EAQ077 212EAQ077 218EAQ077 211EAQ077 207EAQ077 ...
Страница 16: ...13 10 613 SP Page 7 DECALS 216EAQ077 217EAQ077 222EAQ077 221EAQ077 208EAQ077 ...
Страница 31: ...13 10 613 SP Page 22 FIGURE 4 2 FLOW CHART FOR SET UP PROGRAMMING ...
Страница 45: ...13 10 613 SP Page 36 FIGURE 4 10 CONTROL SCHEMATIC COMPRESSOR AT FULL LOAD 204EAY797 Ref Drawing ...
Страница 48: ...13 10 613 SP Page 39 FIGURE 4 13 WIRING DIAGRAM 202EAY546 Ref Drawing ...
Страница 75: ......