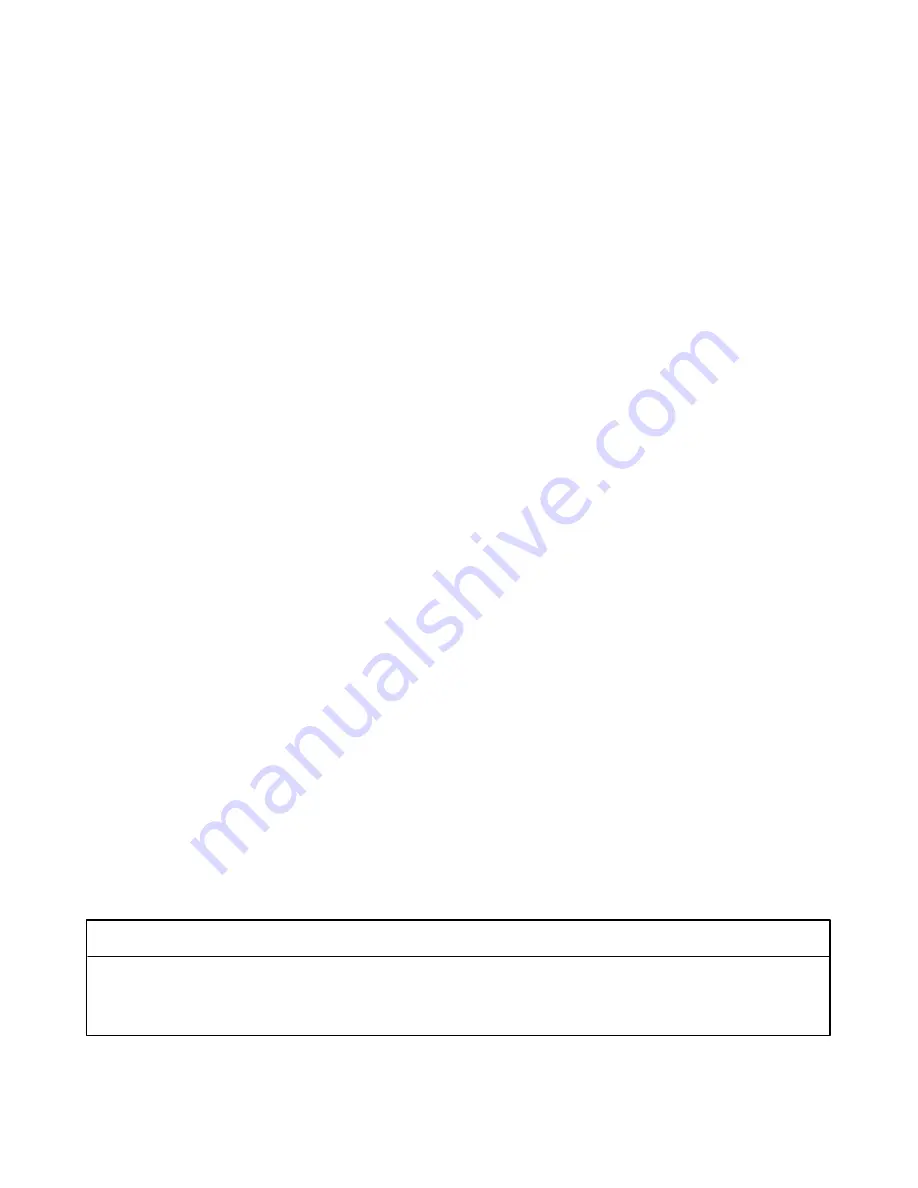
13–10–613 SP Page 12
Water–Cooled Machines (FIGURE 2–4, page 10) –
On water–cooled machines with aftercooler, the mois-
ture separator and condensate drain are shipped loose
and must be installed by customer. Customer must fur-
nish and install all water piping required.
INSTALLATION FOR COLD WEATHER OPERA-
TION – It is recommended that the unit be installed in-
side a shelter that will be heated to temperatures above
freezing (32
_
F, 0
_
C). This will eliminate many of the
problems associated with operating units in cold cli-
mates where freezing rain, drifting snow, freezing con-
densate and bitter cold temperatures are encountered.
Refer to Engineering Data Sheet 13–9–411 for the ad-
vantages of using the heat recovered from rotary com-
pressors. This heat recovery could easily pay for an ad-
equate shelter for the unit.
When an outside installation must be made, the pre-
cautions required will depend on the severity of the en-
vironment. The following are general guidelines for
outside installations:
Cold Weather (Down To +10
_
F)
1.
Be sure all drains, traps, and control lines, includ-
ing pressure transducer lines are heated to avoid
freezing of condensate. Heat tape with thermo-
stat control is generally satisfactory for this pur-
pose and can be obtained at various local plumb-
ing or hardware outlets at nominal cost.
2.
If an air–cooled aftercooler is to be used, provi-
sions to bypass the aftercooler must be made.
Since cold air contains very little moisture, suc-
cessful operation can be achieved without the af-
tercooler. Successful operation down to +15
_
F
can be accomplished by reversing fan flow, but
cooler bypass should still be provided should it be
required.
3.
Provide at least some simple shelter such as a ply-
wood windbreak to protect against drifting snow.
4.
Use only Gardner Denver
R
AEON
t
9000 SP lu-
bricant.
5.
Monitor the unit carefully during start–up and op-
eration to be sure it is functioning normally.
6.
Specify NEMA 4 enclosure for electrical devices.
Extreme Cold Weather Operation (Down To –40
_
F,
–40
_
C) – In addition to the above, the following should
be provided:
1.
A temperature switch to control the fan should be
provided for better starting and quicker warm–up.
This switch can be provided from the factory and
will delay fan start–up until discharge temperature
reaches approximately 150–160
_
F.
2.
It will probably be necessary to provide shutters or
to block off part of the cooler in some manner
since the cooler is greatly oversized for operation
in these low temperatures. Shutters are not a fac-
tory option.
3.
Auto operation should not be used in extreme en-
vironments.
4.
Coolers should be located as close to the unit as
possible. Long lines to and from the cooler only
further complicate the circulation of oil flow on cold
starts. Heat tape and insulation may be required
on oil lines.
5.
Some means of providing heat to the oil reservoir
and cooler during shutdown should be provided.
There are various methods to accomplish this, but
since openings are not provided for sump heaters,
the use of radiant heaters is recommended. The
heaters should be sized to provide at least a
+10
_
F environment for coolers, motor and sump.
FIGURE 2–5, page 11, shows how these might be
located in a typical installation and sizes required.
Remember unsheltered (outside) installations should
be avoided where possible. Installation next to a
heated building where enough heat can be used to
keep the compressor room above freezing will save
many complications in the operation and installation of
the unit.
MOISTURE SEPARATOR/TRAP – Since the unit is
equipped with a built–in aftercooler, a combination
moisture separator and trap is furnished with the unit.
A means of draining condensate will need to be pro-
vided for.
INLET LINE – Where an inlet line is used between the
air filter and the compressor, it must be thoroughly
Length of Inlet Line
Diameter of Pipe Size
0 to 10 Feet
Same as Compressor Inlet Opening
. . . . . . . . . . . . . . . . . . . . . . . . . . . . . . . . . . . . . . . . . . . . . . . . .
10 to 17 Feet
One Size Larger Than Inlet Opening
. . . . . . . . . . . . . . . . . . . . . . . . . . . . . . . . . . . . . . . . . . . . . . . .
17 to 38 Feet
Two Sizes Larger Than Inlet Opening
. . . . . . . . . . . . . . . . . . . . . . . . . . . . . . . . . . . . . . . . . . . . . . .
FIGURE 2–6 – INLET LINE LENGTHS
Содержание ELECTRA-SAVER EAYQ E
Страница 15: ...13 10 613 SP Page 6 DECALS 206EAQ077 212EAQ077 218EAQ077 211EAQ077 207EAQ077 ...
Страница 16: ...13 10 613 SP Page 7 DECALS 216EAQ077 217EAQ077 222EAQ077 221EAQ077 208EAQ077 ...
Страница 31: ...13 10 613 SP Page 22 FIGURE 4 2 FLOW CHART FOR SET UP PROGRAMMING ...
Страница 45: ...13 10 613 SP Page 36 FIGURE 4 10 CONTROL SCHEMATIC COMPRESSOR AT FULL LOAD 204EAY797 Ref Drawing ...
Страница 48: ...13 10 613 SP Page 39 FIGURE 4 13 WIRING DIAGRAM 202EAY546 Ref Drawing ...
Страница 75: ......