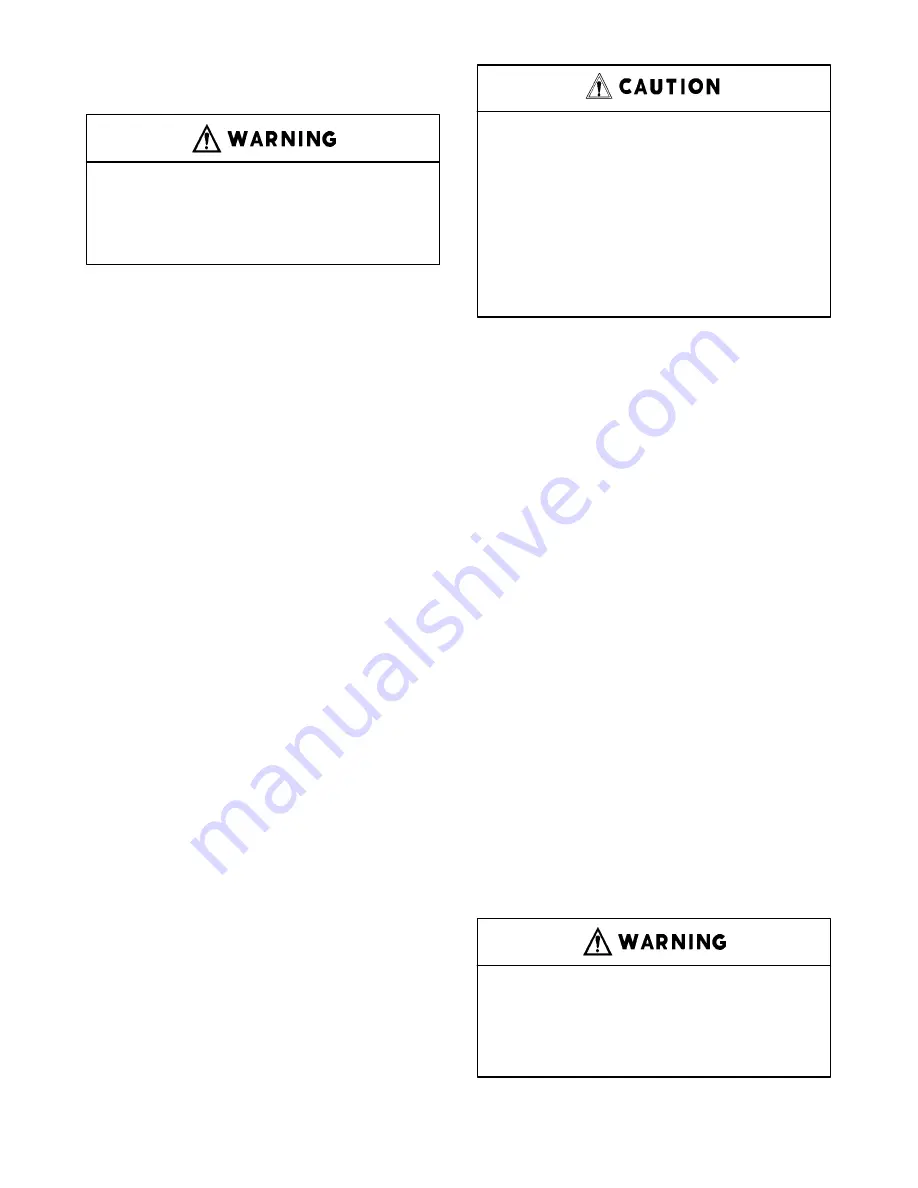
13–10–613 SP Page 14
nections are located in the unit base flange on the left
side of the unit.
It is mandatory that any water cooled
unit be installed in a shelter heated to
temperatures above freezing (32
_
F.,
0
_
C).
The water source should be capable of supplying up to
the maximum flow shown in FIGURE 2–6, page 12,
and FIGURE 2–7, page 13, at a minimum pressure of
40 PSIG; maximum allowable water pressure is 150
PSIG. The water flow rates shown in FIGURE 2–6,
page 12, are approximate and a guide to sizing piping,
cooling tower and other water system equipment.
The heat exchanger system is designed to operate with
water inlet temperatures from 60
_
to 90
_
F and a water
outlet temperature not to exceed 110
_
F. If water cooler
than 60
_
F is used, high water outlet temperatures
(over 110
_
F) will be experienced along with shortened
heat exchanger life caused by tube fouling and corro-
sion. If water warmer than 90
_
F is used, higher com-
pressor oil inlet temperatures and high water usage will
result.
Most water systems will require control of impurities:
filtration, softening or other treatment. See “Compres-
sor Oil Cooler – Water–Cooled Heat Exchanger” for
more information on the water system.
Aftercooler – Heat Exchanger Water Piping
(FIGURE 2–4, page 10, and FIGURE 2–6, page 12,
and FIGURE 2–7, page 13) – If an aftercooler is used
and piped in series with the heat exchanger, install the
water flow control valve and magnetic water shutoff
valve, if used, downstream of the exchanger. Pipe the
aftercooler water outlet to the heat exchanger water in-
let on the compressor unit.
If the aftercooler is piped in parallel with the heat ex-
changer, provide a manual valve between aftercooler
outlet and heat exchanger outlet after the water control
valve to adjust aftercooler water flow for discharge tem-
perature required and most economical water use;
separate water inlet lines are piped to the aftercooler
and heat exchanger.
If the standard factory built–in aftercooler is used, the
maximum allowable water flow through the aftercooler
is 100 gallons per minute on all 350 – 500 HP units and
the maximum water inlet pressure is 150 PSIG. If
another aftercooler is used, consult the manufacturer
for operating limits.
When an aftercooler is piped in series
with the oil cooler, the maximum
allowable flow rate through the
oil/aftercooler system is the max-
imum allowed by the aftercooler. If
the oil cooler requires more water flow
than the maximum allowed by the
aftercooler, a parallel water piping
system must be used.
The water control valve MUST be used to maintain
discharge temperatures approximately 10
_
F. over the
dew point for expected ambient (FIGURE 5–7, page
47). See Section 5 for adjustment instructions and
maximum allowable oil temperature.
ELECTRICAL WIRING – The Electra–Saver
R
unit is
furnished with the compressor motor enclosure as spe-
cified by the user. If unit has an air–cooled oil cooler,
this fan motor is a totally enclosed “air–over” or “fan–
cooled type” and is complete with starter and enclosure
as specified by the user. Allow 42” deep and 30” wide
clear space to the nearest obstruction in accordance
with Article 110–16(a), National Electric Code.
It is necessary to connect the compressor unit (and oil
cooler, if used) to a main starter of the correct size,
power characteristics, and enclosure for the applica-
tion. See Section 4 for typical wiring diagrams; howev-
er, use only the wiring diagrams supplied with the unit
for final connections.
Starter – The main starter is to be mounted at a loca-
tion selected by the user at the time of installation. The
first three feet of line from the motor conduit box to the
starter must be of flexible conduit to maintain effective
vibration isolation. Electrical connections to other parts
of the unit (instrument panel, fan motor, etc.) from the
starter do not require flexible conduit since the com-
pressor and motor are already isolated from these
parts. See Article 110–16(a) National Electric Code for
working clearance.
Electrical shock can cause injury or
death. Open main disconnect switch,
tag and lockout before working on
starter/control box.
Содержание ELECTRA-SAVER EAYQ E
Страница 15: ...13 10 613 SP Page 6 DECALS 206EAQ077 212EAQ077 218EAQ077 211EAQ077 207EAQ077 ...
Страница 16: ...13 10 613 SP Page 7 DECALS 216EAQ077 217EAQ077 222EAQ077 221EAQ077 208EAQ077 ...
Страница 31: ...13 10 613 SP Page 22 FIGURE 4 2 FLOW CHART FOR SET UP PROGRAMMING ...
Страница 45: ...13 10 613 SP Page 36 FIGURE 4 10 CONTROL SCHEMATIC COMPRESSOR AT FULL LOAD 204EAY797 Ref Drawing ...
Страница 48: ...13 10 613 SP Page 39 FIGURE 4 13 WIRING DIAGRAM 202EAY546 Ref Drawing ...
Страница 75: ......