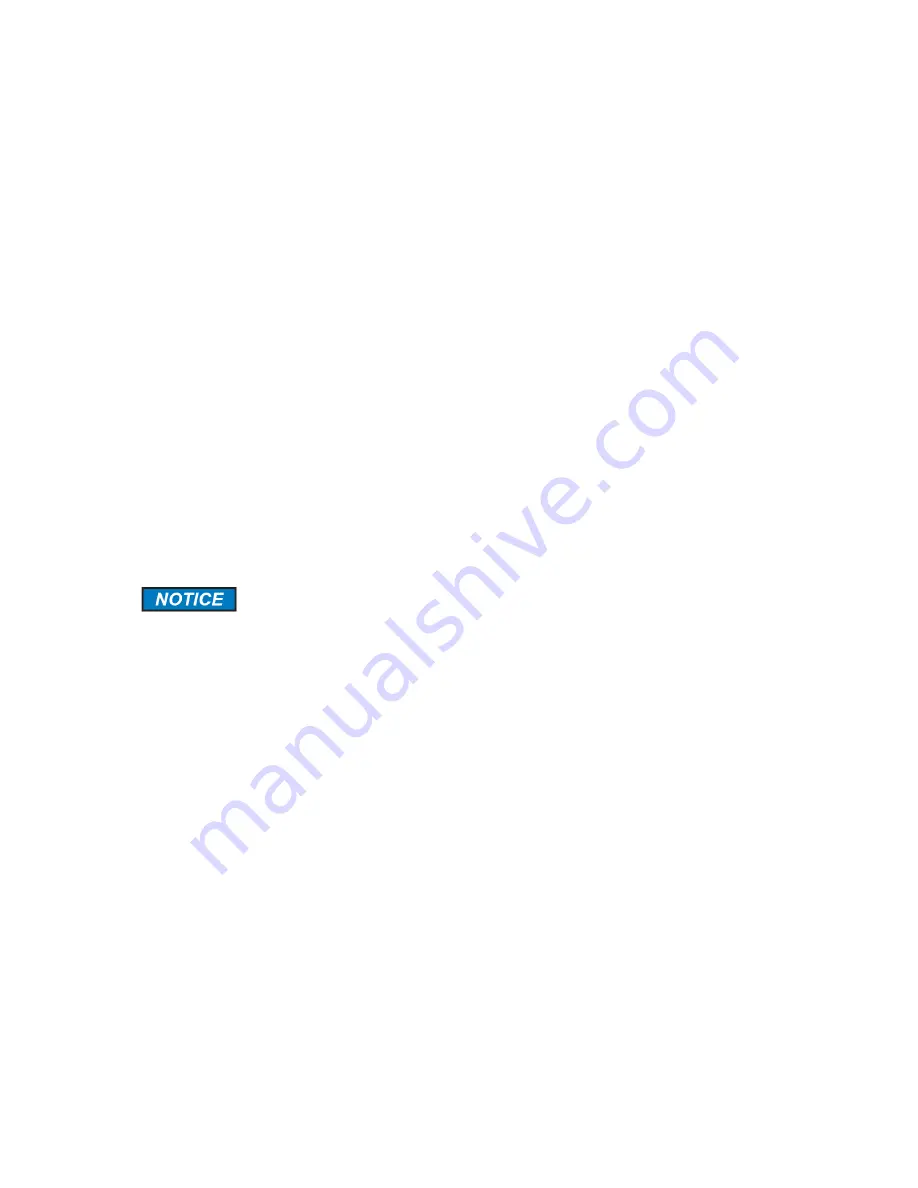
Revision 1
29
6/27/2017
3.2.2 Condenser Cooling Air Flow Adjust Valve
The system provides on/off control of the probe cooling air via a solenoid operated valve. The
Condenser Cooling Air Flow Adjust Valve
is a coarse flow rate adjustment of air used to cool
the condenser section of the sample probe. The sample probe contains an internal surface,
exposed to the process sample gas path, which can be cooled by the introduction of
instrument air. Sulfur condensing on this surface is hydrostatically returned to the process
stream.
The concentration of sulphur vapour in the process sample gas exiting the probe is measured
and displayed on the computer Front Panel as
Sulphur Vapour.
The
Condenser Cooling Air
Flow Adjust Valve
is opened to reduce the
Sulphur Vapour
. There is normally a long time
constant associated with this adjustment. Several factors can impact the temperature of the
gas exiting the probe. These factors include:
•
changes in process gas temperature
•
changes in cooling air temperature
•
changes in the process gas sample aspiration rate and elapsed time since and the duration
of a probe back purge.
During a calibration sequence or back purge operation, instrument air is forced into the
sample probe from the oven. The indicated sulphur vapour concentration during and
immediately after a back purging operation is NOT the sulphur vapour concentration in the
process sample gas.
The desired situation is that the concentration of the sulphur vapour in the
process sample gas exiting the sample probe is lower than with the probe
cooling air off without causing plugging of the sample probe.
3.2.3 Zero Air Flow Adjust Valve
The
Zero Air Flow Adjust Valve
(controls the flow rate of air used in the zeroing and back
purging operations (the analyzer ‘zero’ is adjusted under back purge conditions). Under
normal operating circumstances, the
Zero Air Flow Adjust Valve
is adjusted to provide
sufficient air flow to obtain a 2-5 second stabilized zero response time from a ‘sampling’ state.
The stabilized zero response is ascertained by monitoring the time required for the analyzer
gas concentration outputs to stabilize at a near zero level once the analyzer has been
switched from a sample to zero (back purge) mode. Excessive zero air flow rates will overly
cool oven components. A deficient zero air flow rate may not provide adequate flushing of the
measurement cell before a zero adjustment is made. In extraordinary circumstances, during
sample system clogging (liquid accumulation), the
Zero Air Flow Adjust Valve
may be opened
wide to provide a solid back purge pressure. Alternately, the
Zero Air Flow Adjust Valve
may
be turned down to a trickle for an extended period (20-30 minutes) allowing the heat of the
oven to re-liquefy any solid accumulation (plugging) before increasing the back purging
pressure to clean out the plumbing.
Содержание 943-TGS
Страница 23: ...Revision 1 23 6 27 2017 Figure 2 3 Potted Fixture Figure 2 4 Control Cabinet Fiber Optics Entries ...
Страница 50: ...Revision 1 50 6 27 2017 Figure 4 14 Network Sub Panel ...
Страница 94: ...Revision 1 94 6 27 2017 Figure 9 1 Mounting Detail ...
Страница 95: ...Revision 1 95 6 27 2017 Figure 9 2 Oven Cabinet Detail ...
Страница 96: ...Revision 1 96 6 27 2017 Figure 9 3 Control Cabinet Detail ...
Страница 97: ...Revision 1 97 6 27 2017 Figure 9 4 Power Air Steam Requirements and Input Output Detail ...
Страница 98: ...Revision 1 98 6 27 2017 Figure 9 5 Control Cabinet to Oven Cabinet Interconnect Detail ...
Страница 99: ...Revision 1 99 6 27 2017 Figure 9 6 AC Wiring Detail ...
Страница 100: ...Revision 1 100 6 27 2017 Figure 9 7 DC and Signal Wiring Detail ...
Страница 101: ...Revision 1 101 6 27 2017 This page intentionally left blank ...