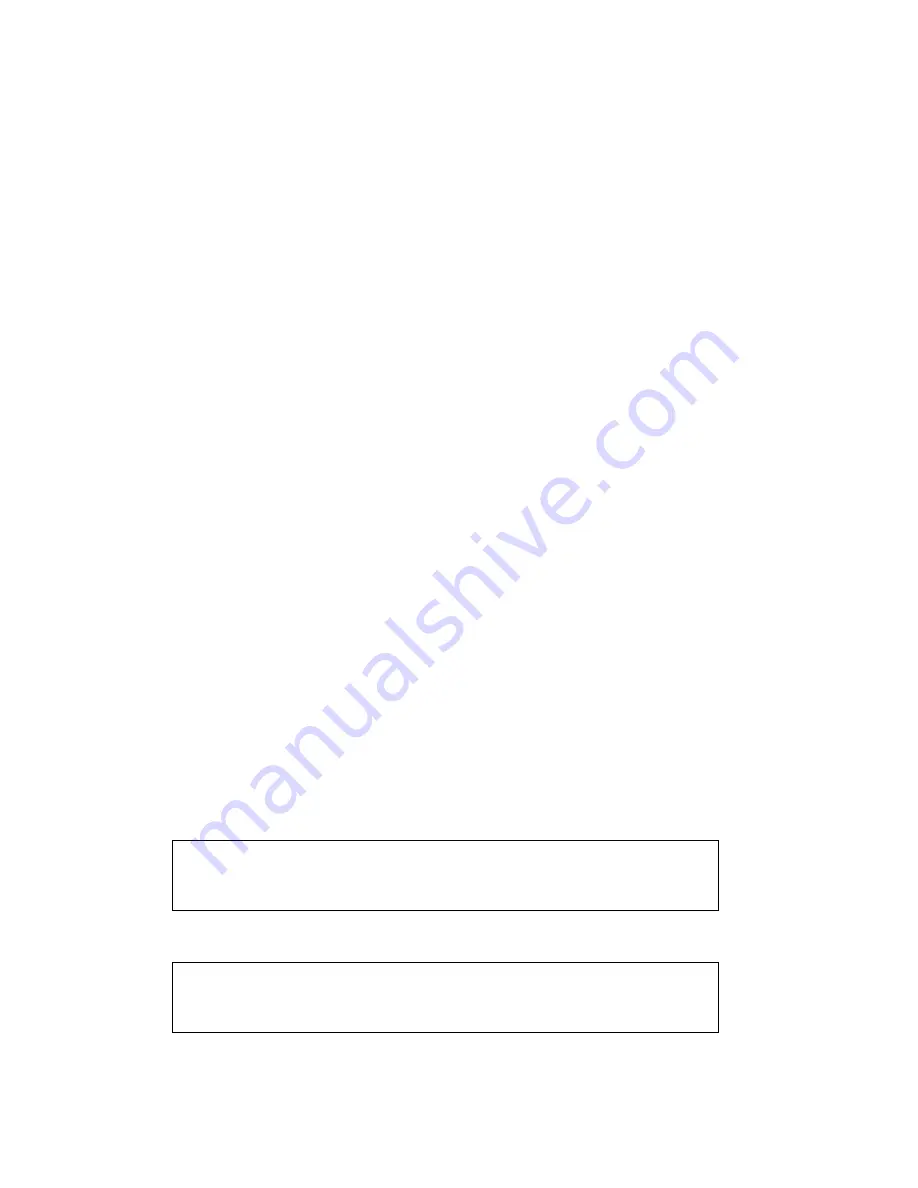
Revision 1
28
6/27/2017
Section 3
Operation
3.1
Overview
The 943-TGS analyzer system is designed to operate automatically with a minimum need for
human intervention. Once installation, commissioning and initial start-up have been
completed, the only human intervention required is when the system indicates a problem or
when routine preventative maintenance is scheduled.
The user interaction program is described in Chapter 4.
The analyzer system computer automatically performs all of the normal operational
procedures including sample flow initiation, analysis, on-line calibration, range sensitivity
selection, fault detection, temperature zone control and fail-safe back purge (should a fault
occur). Operators are alerted to an abnormal state or fault occurrence through indicators on
the display on the front panel and the output alarm contact closures.
The only manual adjustments to system controls (not through the computer) are the flow
control of various instrument air streams.
Flow adjustment valves for the zero/purge gas flow rate, the aspirator drive air flow rate and
the sulfur condenser air flow rate are provided and located according to Oven Cabinet
Component Locations drawing. All valves are clearly labeled according to their title and
function. The Flow Diagram drawing provides a schematic of the flow streams in the analyzer
system. Isolation on/off block valves are provided in the oven compartment to do the sample
probe steam-out procedure, if required.
3.2
Flow Control Settings
The flow control settings govern system operation. Once the system has been commissioned
and the flow rates have been set, only occasional adjustments should be required. Flow
settings will be checked and verified when doing the recommended routine preventative
maintenance procedure. The flow control valves can be located using the diagrams in
Section 9.
3.2.1 Cabinet Purge Air Flow Adjust Valve
943-TGS-CE
The pressure control (needle) valve on the purge controller is set for an
enclosure pressure of 1.07mbar as read on the purge controller display.
943-TGS-CE
The rapid purge minimum duration is 5 minutes at a minimum flow rate of
0.14m
3
/min.
Содержание 943-TGS
Страница 23: ...Revision 1 23 6 27 2017 Figure 2 3 Potted Fixture Figure 2 4 Control Cabinet Fiber Optics Entries ...
Страница 50: ...Revision 1 50 6 27 2017 Figure 4 14 Network Sub Panel ...
Страница 94: ...Revision 1 94 6 27 2017 Figure 9 1 Mounting Detail ...
Страница 95: ...Revision 1 95 6 27 2017 Figure 9 2 Oven Cabinet Detail ...
Страница 96: ...Revision 1 96 6 27 2017 Figure 9 3 Control Cabinet Detail ...
Страница 97: ...Revision 1 97 6 27 2017 Figure 9 4 Power Air Steam Requirements and Input Output Detail ...
Страница 98: ...Revision 1 98 6 27 2017 Figure 9 5 Control Cabinet to Oven Cabinet Interconnect Detail ...
Страница 99: ...Revision 1 99 6 27 2017 Figure 9 6 AC Wiring Detail ...
Страница 100: ...Revision 1 100 6 27 2017 Figure 9 7 DC and Signal Wiring Detail ...
Страница 101: ...Revision 1 101 6 27 2017 This page intentionally left blank ...