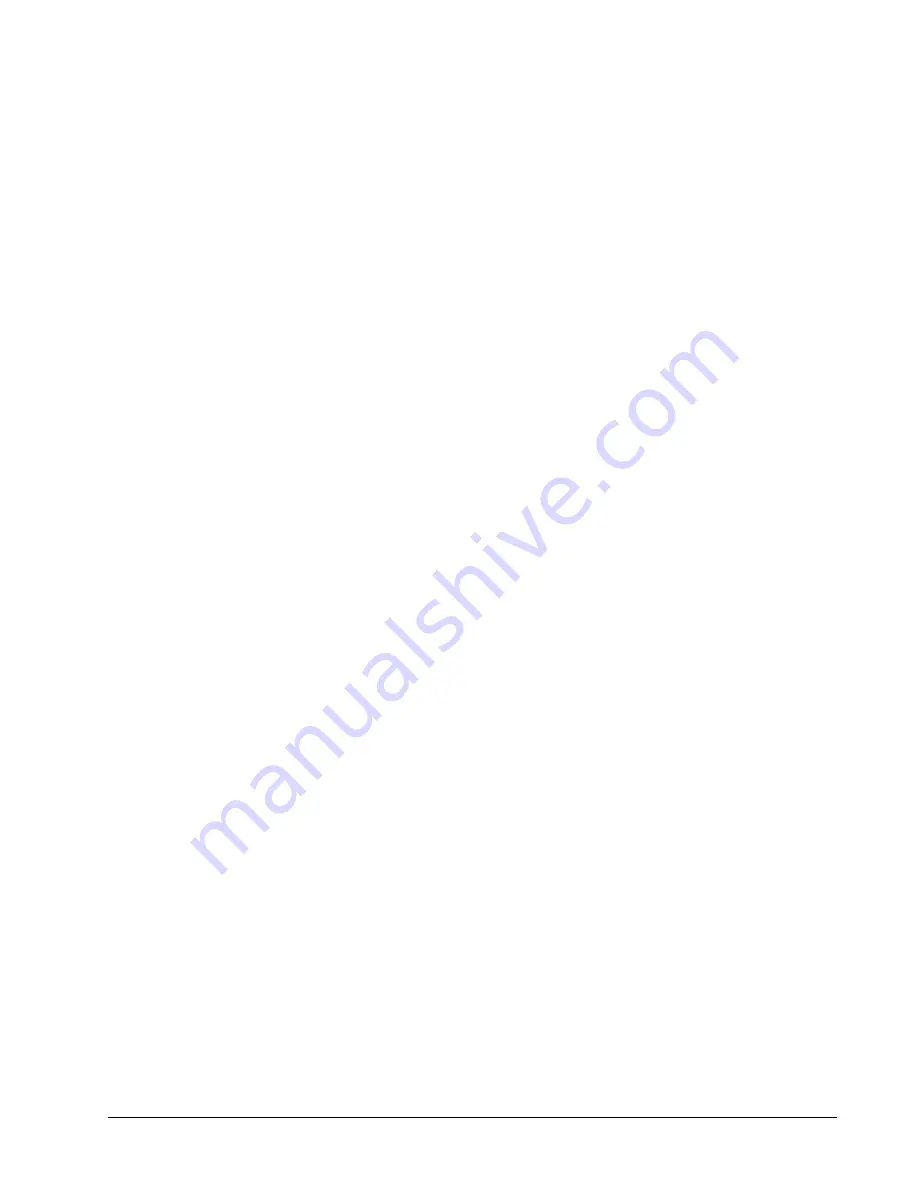
This is another way to limit the amount of current but can also maintain the resolution of the ±10V motor
command line.
Step B.
Set the Error Limit
When
ER
(error limit) and
OE
(off-on-error) is set, the controller will automatically shut down the motors when
excess error (|
TE
| >
ER
) has occurred. This is an important safety feature during set up as wrong polarity can cause
the motor to run away, see
Step C
below for more information regarding runaway motors.
NOTE:
Off-on-error (
OE
) requires the amplifier enable signal to be connected from the controller to the amplifier.
This is automatic when using Galil's internal amplifiers, see Step 10. Connecting External Amplifiers and Motors, pg
21 for external amplifiers
Step C.
Understanding and Correcting for Runaway Motors
A runaway motor is a condition for which the motor is rotating uncontrollably near it's maximum speed in a single
direction. This is often caused by one of two conditions:
1. The amplifier enable signal is the incorrect logic required by the amplifier
This is only applicable to external amplifiers
only
.
If the motor is in a
MO
state when the motor runs away, the
MO
command is toggling your amplifier
“on/enabled” and needs to be reconfigured. The motor is running away because the controller is registering
the axis is in an “inactive” and is not attempting to control it's movement. See Step 10. Connecting External
Amplifiers and Motors, pg 21 for configuring the amplifier enable signal.
2. The motor and encoder are in opposite polarity causing a positive feedback loop
Reversed polarity is when a positive voltage on the motor command line results in negative movement of the
motor.
This will result in a
positive feedback loop
and a runaway motor.
The following steps can be taken to detect reverse polarity, the A-axis is used as an example:
1. After connecting your servo motor using either Step 9. Wiring Motors to Galil's AMP-19540., pg 17 or
Step 10. Connecting External Amplifiers and Motors, pg 21 issue the following commands:
MO A
KIA= 0
KPA= 0
KDA= 0
SH A
2. Check your current position by issuing
TP A
.
3. Set a small, positive voltage on your motor command line using the
OF
command; use a high enough
voltage to get the motor to move. This will cause a runaway-like condition so have an appropriate
OE
set, see
Step B
. Example:
OFA= 0.5
4. If the motor has not been disabled by
OE
, disable it by issuing
MO A
.
5. Check the position again by using
TP A
.
6. If
TP
has increased, than the motor command line and encoder are in correct polarity. If
TP
has
decreased than the motor command line is in opposite polarity with the encoder.
If the system has reverse polarity, take the following steps to correct for it:
Brushed Motor
Choose
one
of the following:
1. Reverse the direction of the motor leads by swapping phase A and phase B
Chapter 2 Getting Started ▫ 16
DMC-42x0 User Manual
Содержание DMC-42 0 Series
Страница 85: ...Chapter 6 Programming Motion 81 DMC 42x0 User Manual Figure 6 14 ECAM cycle with Z axis as master...
Страница 195: ...ICM 2900 PCB Layout Appendices 191 DMC 42x0 User Manual...
Страница 205: ...CB 50 100 Drawings Appendices 201 DMC 42x0 User Manual...
Страница 206: ...Appendices 202 DMC 42x0 User Manual...
Страница 207: ...Appendices 203 DMC 42x0 User Manual...
Страница 208: ...Appendices 204 DMC 42x0 User Manual...
Страница 209: ...Appendices 205 DMC 42x0 User Manual...
Страница 210: ...Appendices 206 DMC 42x0 User Manual...
Страница 211: ...Appendices 207 DMC 42x0 User Manual...
Страница 214: ...CB 50 80 Drawing Appendices 210 DMC 42x0 User Manual...
Страница 215: ...Appendices 211 DMC 42x0 User Manual...