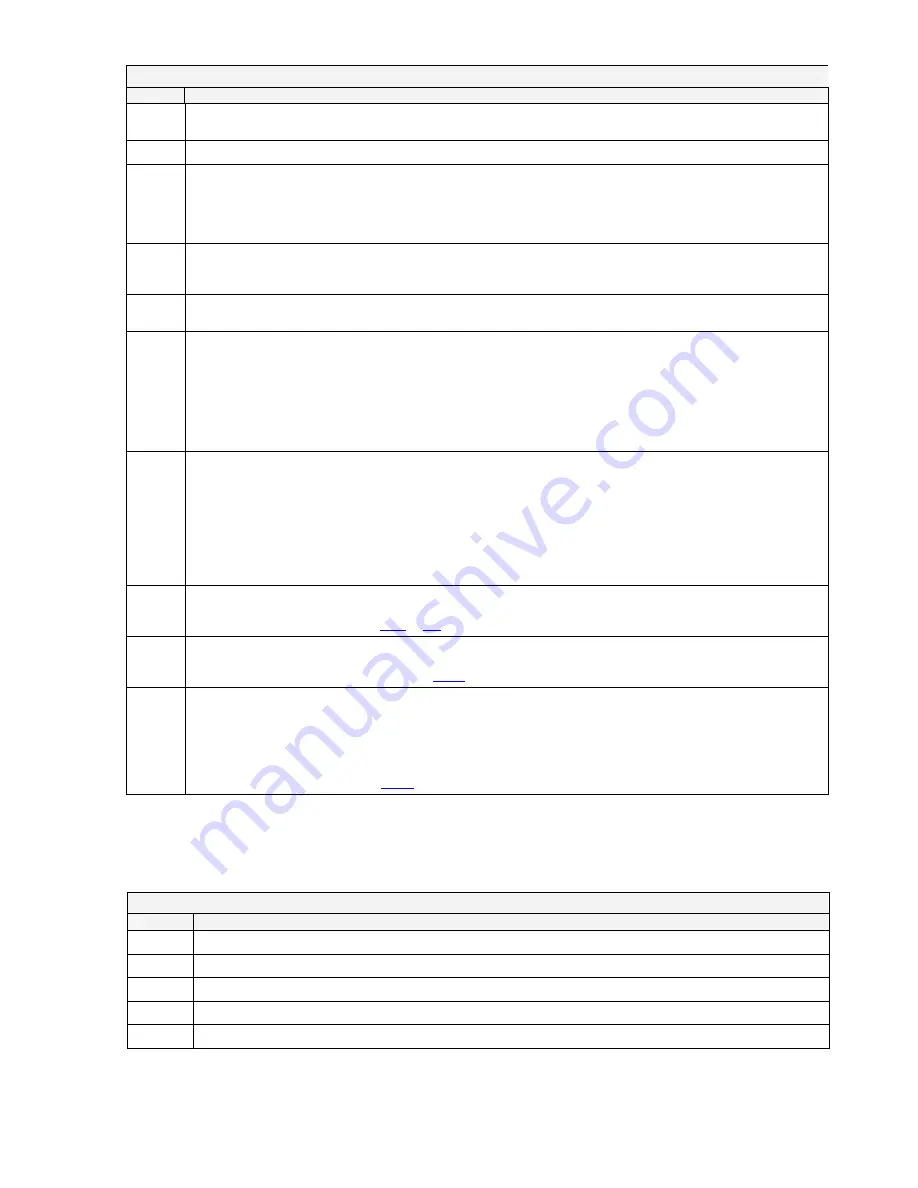
Product Specification
Page 18 of 18
1303090MS01
LA-309 Controlled Atmosphere Infrared Furnace
April 15, 2009
Table 17-1. Optional Equipment
KEY
DESCRIPTION
RTL
Right to Left:
Belt moves from the right to left as viewed from the operator console.
No cost option when specified
at time of order, available on all furnaces.
SBW
Special Belt Weave.
Custom belt in lieu of standard balanced weave design.
Option available on most furnaces.
SMEMA SMEMA
Lane
Control.
Product tracking sensors at entrance and exit which provide SMEMA 1.1 busy/board
available signal generation to coordinate product handling from upstream and downstream equipment. The on-
screen tracking feature counts the number of product units travelling through the furnace. The tracking feature sets
off an alarm if the exit sensor does not detect the arrival of an expected product unit at the unloading station.
Option
available on most furnaces.
SP1 Critical
Spares
Kit.
Increases furnace availability. Package includes critical parts, such as fuses, SCR, PLC I/O
modules and lamps that may be needed to restore full operation of the furnace. An itemized list of included spare
parts shall be available.
Option available on all furnaces.
SPP Special
Paint.
Customer specified color in lieu of standard Sherwin Williams Stone Gray, P/N F63TXA-0382-2322
Polane-T Texture or equal.
Option available on most furnaces.
UC
Ultrasonic Cleaner.
An ultrasonic belt cleaning system to remove particulate and fines that accumulate on the belt
during normal furnace operation. Includes ultrasonic generator, heated tank, pumped water recirculation system, and
compressed air blow-off of water droplets. As the belt is drawn through a tank of water, ultrasonic energy removes
particulate matter and contamination from the belt. Tank water levels are automatically maintained. As the belt exits
the tank, a flow of facility-supplied CDA blows water droplets from the belt to aid belt drying through evaporation. Start
of ultrasonic cleaning and its duration are set by the user in the OI. The ultrasonic tank water is automatically filled,
heated, and drained at the end of cleaning. The system requires plant clean water supply and drain.
Same as UCD
option, but without electric heater/blower drying system.
Option available on most furnaces.
UCD
Ultrasonic Cleaner with Dryer.
An ultrasonic belt cleaning system to remove particulate and fines that accumulate
on the belt during normal furnace operation. Includes ultrasonic generator, heated tank, pumped water recirculation
system, and an electric heater/blower system to provide automatic cleaning and drying of the belt. As the belt is
drawn through a tank of water, ultrasonic energy removes particulate matter and contamination from the belt. Tank
water levels are automatically maintained. As the belt exits the tank, a flow of facility-supplied CDA blows water
droplets from the belt and then completely dried by an electric heater/blower system. Start of ultrasonic cleaning and
its duration are set by the user in the OI. The ultrasonic tank water is automatically filled, heated, and drained at the
end of cleaning. The system requires plant clean water supply and drain.
Same as UC option, but with electric
heater/blower system.
Option available on most furnaces.
UCF
UCD Water Filter, External, Quick Disconnect.
Filter for UC or UCD ultrasonic cleaner tank recirculation system.
Allows the filter, enclosed in a stainless steel filter housing mounted outside furnace cabinet, to be replaced without
opening furnace panels.
Requires
, option available on most furnaces.
UPSC
Un-interruptible Power Supply, Computer.
Short term battery backup for emergency power when facility power
fails. Provides instantaneous protection to computer system from input power interruptions and power surges. Does
not provide power for furnace operation (see
option).
Available on most furnaces.
UPSF
Un-interruptible Power Supply, Furnace.
Short term battery backup for emergency power when facility power fails.
Provides necessary power to run the belt, fans, and control system for at least twenty minutes during a power outage.
The transport belt continues to run at set speed which minimizes product loss during brief power failures. The unit
automatically switches from standby to PROCESS START upon restoring power if the lower alarm temperature limit
has not been reached. The control software includes modification to add automatic reset without using the normal
power up and screen menu selection process, so that immediate restart is available after power interruption. Includes
power for computer operation (see
option for computer UPS only).
Available on most furnaces.
18.0 ALTERNATE MATERIALS
Many furnace components can be manufactured of alternate materials, if requested at the time of
order. Key for alternate materials.
Table 18-1. Alternate Materials
KEY
DESCRIPTION
-AL Aluminum.
Standard material for many furnace components.
-SS Stainless
Steel.
Fabricated from stainless steel, various grades.
-304 Stainless
Steel.
Fabricated from 304 and 304L stainless steel, and 316 and 316L as available.
-316 Stainless
Steel.
Fabricated from 316 and 316L stainless steel.
-PTFE Teflon.
Components of Polytetrafluoroethylene (PTFE) - manufactured by DuPont as Teflon® or equal.
[end of specification]
Содержание LA-309
Страница 5: ...10 004 676 110000 v WARRANTY Warranty goes here ...
Страница 6: ...vi LA 309 Owner s Manual ...
Страница 12: ...Contents xii LA 309 Owner s Manual ...
Страница 20: ...Section 1 1 8 LA 309 Owner s Manual ...
Страница 68: ...Section 3 3 28 LA 309 Owner s Manual ...
Страница 70: ...Section 4 4 2 LA 309 Owner s Manual ...
Страница 72: ...Section 4 4 4 LA 309 Owner s Manual ...
Страница 98: ...Section 5 5 2 LA 309 Owner s Manual ...
Страница 100: ...Section 5 5 4 LA 309 Owner s Manual ...
Страница 106: ...Section 5 5 10 LA 309 Owner s Manual ...
Страница 108: ...Section 5 5 12 LA 309 Owner s Manual ...
Страница 110: ...Section 5 5 14 LA 309 Owner s Manual ...
Страница 112: ...Section 6 6 2 LA 309 Owner s Manual ...
Страница 114: ......
Страница 115: ......
Страница 126: ...Section 7 1 Fiberfrax Cements MSDS 042006 Owner s Manual ...
Страница 139: ...MSDS 2 Fiberfrax Duraboard MSDS 042006 MATERIAL SAFETY DATA SHEETS ...
Страница 140: ...Section 7 2 Fiberfrax Duraboard MSDS 042006 Owner s Manual ...
Страница 153: ...MSDS 3 Fiberfrax Fibers MSDS 042006 MATERIAL SAFETY DATA SHEETS ...
Страница 154: ...Section 7 3 Fiberfrax Fibers MSDS 042006 Owner s Manual ...
Страница 167: ...MSDS 4 Fiberfrax Papers MSDS 042006 MATERIAL SAFETY DATA SHEETS ...
Страница 168: ...Section 7 4 Fiberfrax Papers MSDS 042006 Owner s Manual ...
Страница 181: ...MSDS 5 Magnaform MSDS 050406 MATERIAL SAFETY DATA SHEETS ...
Страница 182: ...Section 7 5 Magnaform MSDS 050406 Owner s Manual ...
Страница 183: ......
Страница 184: ......
Страница 185: ...Section 7 6 RTU Silicone Red Hi Temp 042006 Owner s Manual ...
Страница 186: ...MSDS 6 RTU Silicone Red Hi Temp 042006 MATERIAL SAFETY DATA SHEETS ...
Страница 189: ...Section 7 7 Kaowool Insulation MSDS 050406 Owner s Manual ...
Страница 190: ...MSDS 7 Kaowool Insulation MSDS 050406 MATERIAL SAFETY DATA SHEETS ...
Страница 201: ...Material Safety Data Sheets 7 15 Notes ...
Страница 202: ...Section 7 7 16 Owner s Manual ...
Страница 203: ...8 1 Section 8 APPENDIX A 8 1 TEC10 INTERFACE MODULE CALIBRATION 8 2 675 110001 FURNACE DRIVE MOTOR AND CONTROL ...
Страница 204: ...Section 8 Owner s Manual ...
Страница 206: ...Section 8 Owner s Manual ...
Страница 212: ...iv Operation and Troubleshooting ...
Страница 214: ...vi Operation and Troubleshooting ...
Страница 224: ...Page 10 Operation and Troubleshooting ...
Страница 231: ...9 1 Section 9 APPENDIX B 9 1 EC913 CALIBRATION REPORT 9 2 SERIES EC900 OXYGEN ANALYZERS ...
Страница 232: ...Section 8 Owner s Manual ...
Страница 233: ......
Страница 234: ...Section 8 Owner s Manual ...
Страница 276: ...EC900 Series Operation Manual V 4 1 www systechillinois com Page 39 Appendix 1 Drawing Number B900 176 ...
Страница 277: ...EC900 Series Operation Manual V 4 1 www systechillinois com Page 40 Appendix 2 Drawing Number B 920 043 ...
Страница 278: ...EC900 Series Operation Manual V 4 1 www systechillinois com Page 41 Appendix 3 Drawing Number B 900 180 ...
Страница 279: ...Section 8 Owner s Manual ...
Страница 281: ...MSDS MATERIAL SAFETY DATA SHEETS ...
Страница 282: ...16 Notes ...