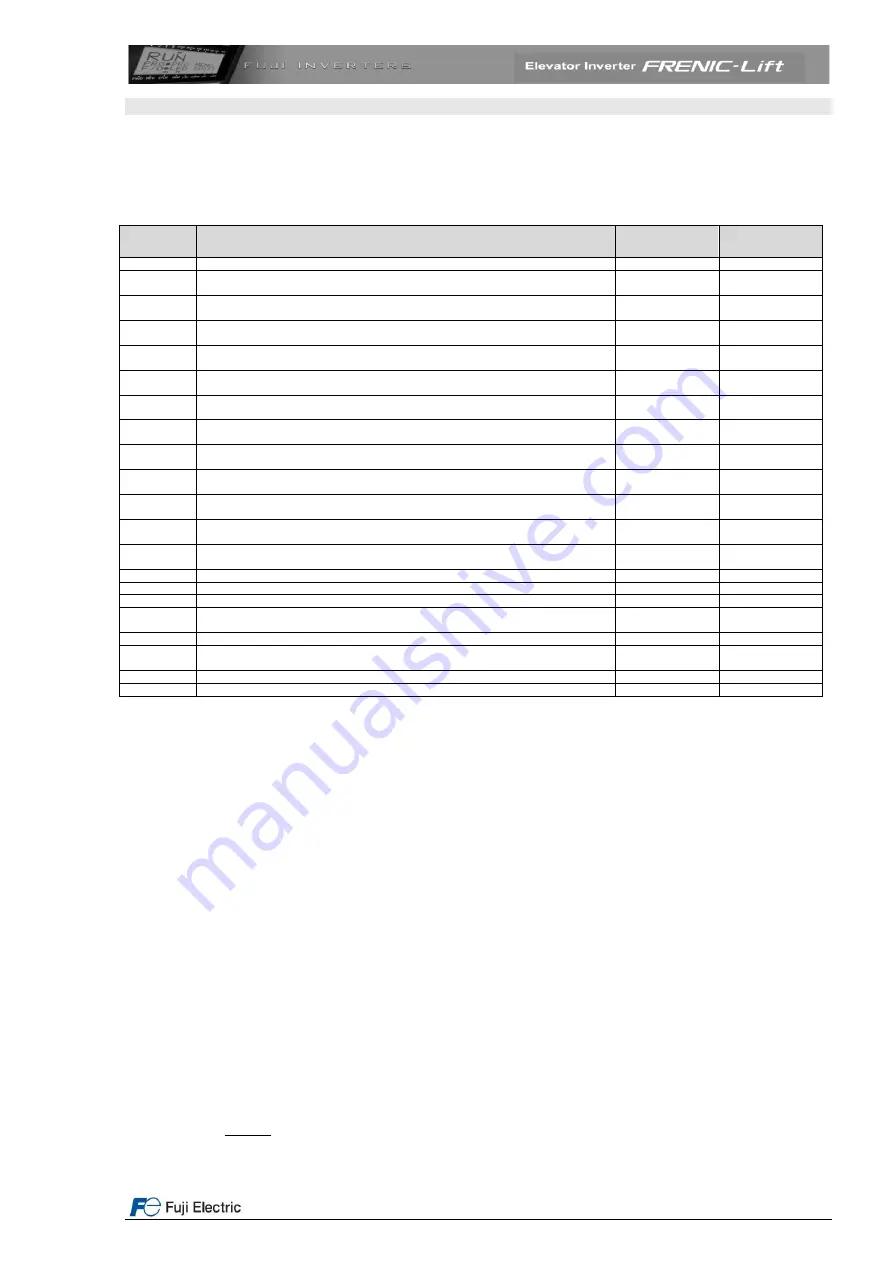
Page
27
of
42
Fuji Electric Europe GmbH
n
n
V
L
I
L
33
,
4
05
11. Settings
11.3 Specific settings for permanent magnet synchronous motors
For permanent magnet synchronous motors pole tuning has to be performed before the first travel. The brake stays
applied. To do so, the parameters described in the table below must be set.
Table 20. Basic setting for synchronous motor
Function
Meaning
Factory
setting
Setting
H03
Initialization of factory settings for synchronous motors
0
2
L01
Encoder type: ECN 1313 EnDat 2.1 or ERN 1387 (or compatible) is possible. See
information from manufacturer data sheet or encoder name plate
0
4 for Endat 2.1
5 for ERN1387
Remove power supply from the inverter for a short time (ensure that Keypad is
completely off)
E46
Language setting (clear text function description)
1
Depends on the
country
C21
Speed selection units (C21=0: rpm, C21=1: m/min or C21=2: Hz)
0
Depends on the
installation
P01
Motor number of poles from manufacturer data sheet or motor name plate
Must be set before setting F03 value!
20
Depends on the
motor
F03
Motor’s maximum speed. The units are always rpm (not dependant on C21 setting).
Normally F03 is motor speed at nominal lift speed
60 rpm
Depends on the
motor
L31
Maximum linear (in m/min) speed corresponding to F03 value. Used as linearization
factor for speed settings
60.00
Depends on the
installation
F04
Motor’s rated speed (from motor’s name plate). The units depend on the setting of
function C21
60 rpm
Depends on the
motor
F05
Motor rated voltage from name plate (V)
380 V
Depends on the
motor
F11
Overload detection level
Depends on the
inverters capacity
Same as P03
P02
Motor rated capacity (power) from name plate in kW
Depends on the
inverters capacity
Depends on the
motor
P03
Motor rated current from name plate in A
Depends on the
inverter capacity
Depends on the
motor
P06
Motor no-load current in A (for synchronous motor set this function to 0)
0 A
0 A
P07
Motor stator resistance R1 in %
5%
5%
P08
Motor stator reactance X1 in %
10%
10%
L02
Encoder resolution (pulses per revolution) from manufacturer data sheet or name plate
2048 p/rev
Depends on the
encoder
L04
Offset angle obtained from pole tuning
0.00
Automatic
L05
Current loop controller (ACR) P gain
1.5
Depends on the
motor
L36
Speed loop controller (ASR) P gain at high speeds
2.50
2.00
L38
Speed loop controller (ASR) P gain at low speeds
2.50
2.00
Pole tuning procedure in 7 steps:
To perform the described procedure the enable (EN1&EN2) inputs must be active.
1. Are motor and encoder connected properly?
2. Apply power to the inverter
3. The functions mentioned in the table above must be set.
Check that the inverter receives the encoder pulses as following: in the keypad go to Menu
4. I/O Check
and
press the down arrow key until you reach the page that shows P1, Z1, P2 and Z2 (8/8). If the motor is not moving,
the display should show
+0 p/s
after P2. Open (release) the brake and turn a little bit the motor. In this moment
the display should show a number different than 0 (positive or negative depending on the rotation direction). If the
display shows
----p/s
(or
+0 p/s
meanwhile the motor is turning) means that no signal is coming from the encoder.
In this case please check the encoder cable and the connection of the signals.
4. Set function
L03 to 1
and press FUNC/DATA key.
5. Give RUN command to the inverter from the lift controller (normally in RESCUE or INSPECTION mode). The
main contactors will be closed and current will flow through the motor producing some acoustic noise. This
procedure will take some seconds. After the procedure was finished correctly the offset value is saved and
shown in function
L04
. Write down the displayed value. If Er7 is displayed check the motor and encoder cabling
and repeat steps 5 and 6.
6. If possible, open the brake and let the cabin move some centimetres.
7. Perform steps 5 and 6 again. The result in function L04 between different measurements must not differ more
than ± 15°.
L05: Current loop regulator (ACR) P gain calculation
L=Motor inductance (minimum value between Ld and Lq) [mH]
V
n
=Motor rated voltage [V] (F05)
I
n
=Motor rated current [A] (P03)