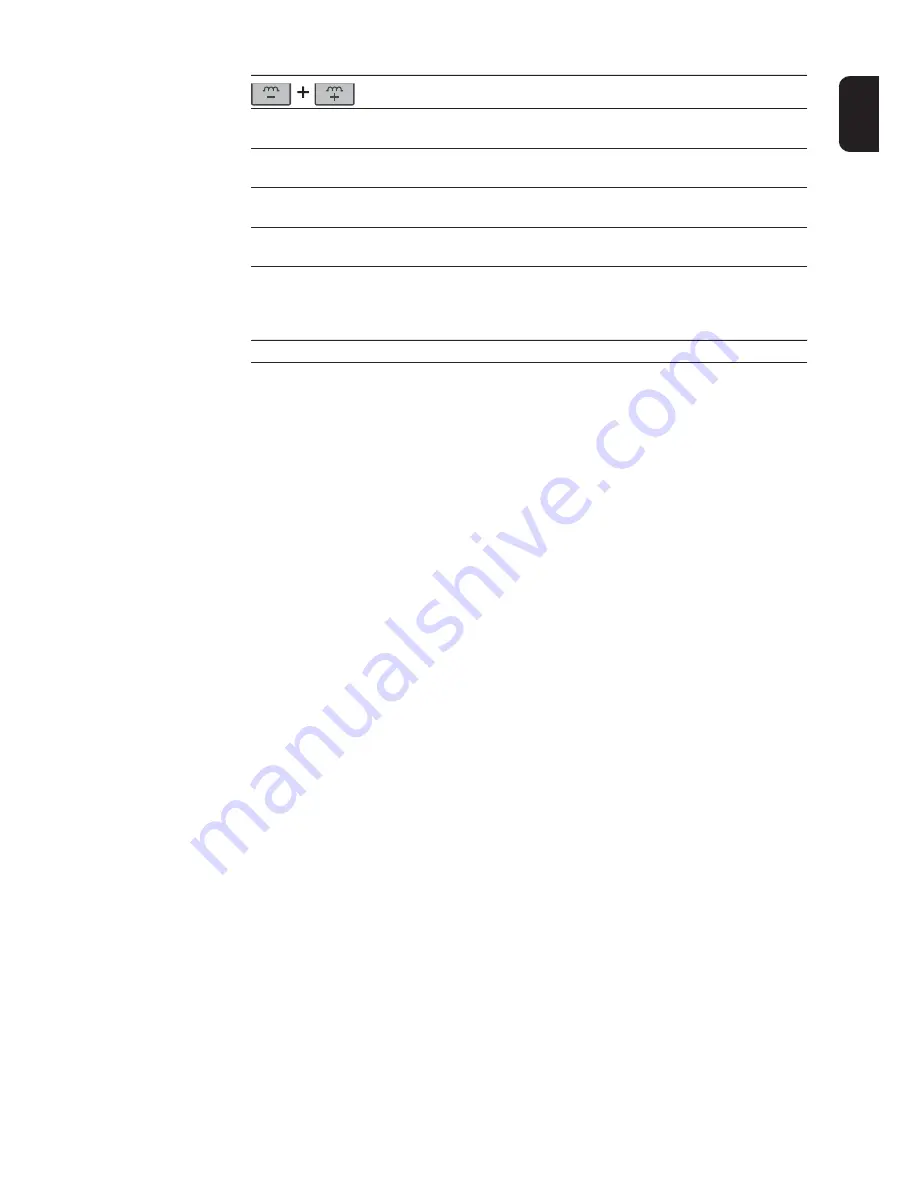
31
EN
Explanation
Example:
1.00 | 4.21
Firmware version
Example:
2 | 491
Welding program configuration
Example:
r 2 | 290
Number of the currently selected welding program
Example:
iFd | 0.0
Motor current for wire drive in A
The value changes as soon as the motor is running.
654 | 32.1
= 65,432.1 hours
= 65,432 hours 6 mins
Indicates the actual arc time since using for the first time
Note: The arc time indicator is not suitable as a basis for calcu-
lating hiring fees, warranty services, etc.
2nd
2nd menu level for service engineers
Содержание VR 5000 noSpool
Страница 2: ...2...
Страница 4: ...4...
Страница 19: ...General information...
Страница 20: ......
Страница 25: ...Control elements and connections...
Страница 26: ......
Страница 41: ...Installation and commissioning...
Страница 42: ......
Страница 44: ...44 The VR 5000 noSpool without an integrated wirespool holder may only be set up and op erated in closed areas...
Страница 51: ...51 EN 1 2 1 2...
Страница 54: ...54 1 Contact pressure standard values U groove roll ers Steel 4 5 CrNi 4 5 Tubular cored electrodes 2 3 1 1...
Страница 58: ...58...
Страница 59: ...Welding...
Страница 60: ......
Страница 76: ...76 Number 3 Number 4 Number 5...
Страница 77: ...Setup settings...
Страница 78: ......
Страница 92: ...92...
Страница 93: ...Troubleshooting and maintenance...
Страница 94: ......
Страница 105: ...Technical data and settings tables...
Страница 106: ......
Страница 123: ...Appendix...
Страница 125: ...125...
Страница 126: ...126 E Euro connection Connectors F Fronius connection FSC Fronius system connection TW Tweco connection...
Страница 127: ...127 8 8 8 8 5 5 5 Motor Plate Alu 4R s Connector Motor...
Страница 128: ...128...
Страница 129: ...129...
Страница 130: ...130...
Страница 131: ...131...