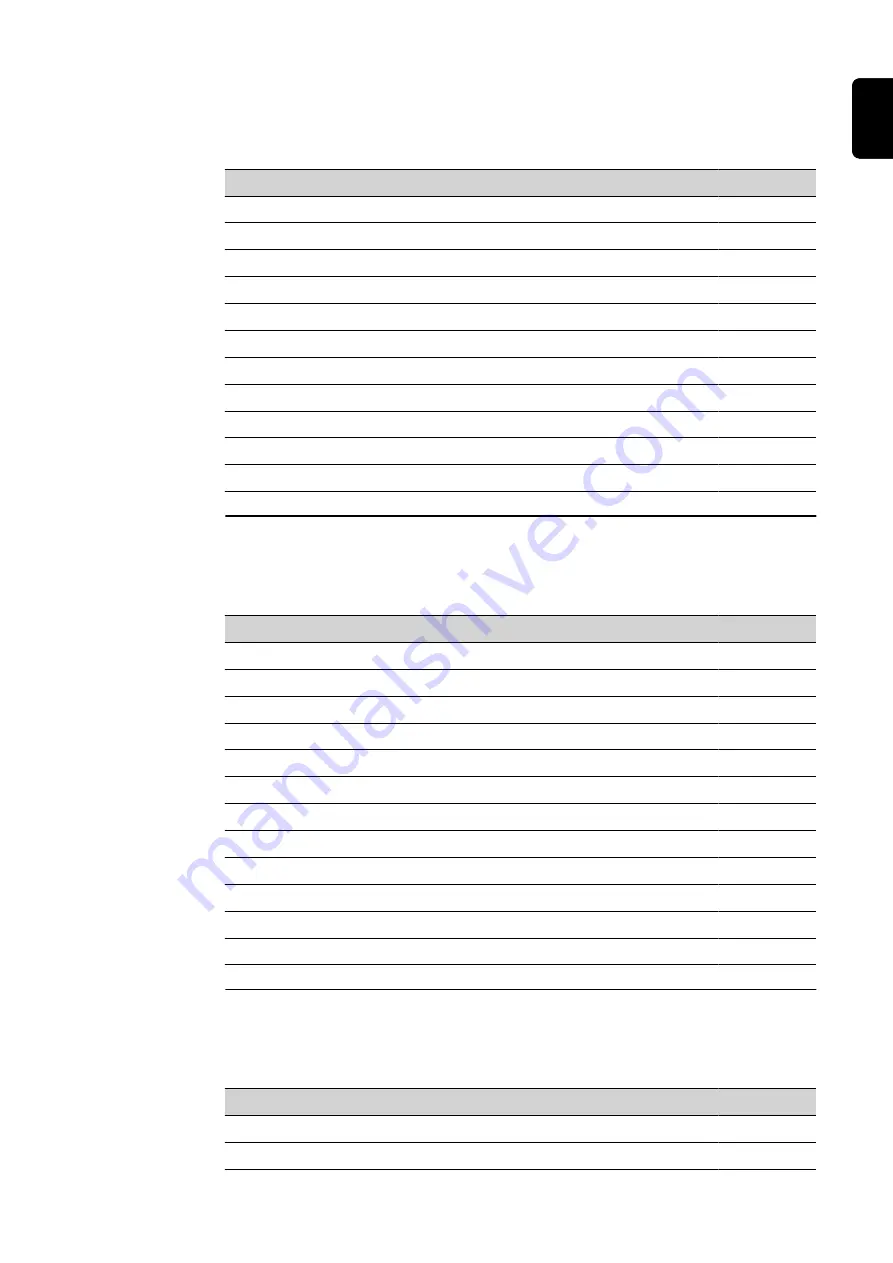
-
Shielding gas: CO
2
-
Material: G3 Si 1
-
Wire diameter: 0.8 mm (.3 in.)
-
Ignition current: 400 A
Sheet thickness
Wire feed speed
Welding voltage
Dynamic
0.8 mm (.03 in.)
1.5 m/min (59.06 ipm)
16 V
4
1 mm (.04 in.)
3 m/min (118.11 ipm)
16.8 V
4
1.5 mm (.06 in.)
5 m/min (196.85 ipm)
18.6 V
3
2 mm (.08 in.)
6.4 m/min (251.97 ipm)
19.5 V
3
3 mm (.12 in.)
9.5 m/min (374.02 ipm)
22.3 V
2
4 mm (.16 in.)
11.1 m/min (437.01 ipm)
23.1 V
2
5 mm (.2 in.)
15.2 m/min (598.43 ipm)
25.8 V
1
6 mm (.24 in.)
17.5 m/min (688.98 ipm)
26.1 V
1
8 mm (.31 in.)
20 m/min (787.40 ipm)
27 V
0
10 mm (.39 in.)
22 m/min (866.14 ipm)
28.5 V
0
12 mm (.47 in.)
25 m/min (984.25 ipm)
31.5 V
0
-
Shielding gas: CO
2
-
Material: G3 Si 1
-
Wire diameter: 0.9 mm (.035 in.)
-
Ignition current: 450 A
Sheet thickness
Wire feed speed
Welding voltage
Dynamic
0.8 mm (.03 in.)
1.4 m/min (55.12 ipm)
17.1 V
4
1 mm (.04 in.)
2.2 m/min (86.61 ipm)
17.4 V
4
1.5 mm (.06 in.)
2.7 m/min (106.3 ipm)
18.6 V
4
2 mm (.08 in.)
4 m/min (157.48 ipm)
19.2 V
4
3 mm (.12 in.)
6 m/min (236.22 ipm)
20.5 V
3
4 mm (.16 in.)
9 m/min (354.33 ipm)
21.5 V
3
5 mm (.2 in.)
10 m/min (393.7 ipm)
24 V
3
6 mm (.24 in.)
11.5 m/min (452.76 ipm)
24.9 V
2
8 mm (.31 in.)
13 m/min (511.81 ipm)
25.5 V
2
12 mm (.47 in.)
15 m/min (590.55 ipm)
29.5 V
1
15 mm (.59 in.)
17 m/min (669.29 ipm)
32 V
0
20 mm (.79 in.)
22 m/min (866.14 ipm)
34 V
0
-
Shielding gas: CO
2
-
Material: G3 Si 1
-
Wire diameter: 1.0 mm (.04 in.)
-
Ignition current: 500 A
Sheet thickness
Wire feed speed
Welding voltage
Dynamic
0.8 mm (.03 in.)
1.6 m/min (62.99 ipm)
16.7 V
3
1 mm (.04 in.)
2 m/min (78.74 ipm)
17.6 V
3
141
EN
Содержание TransSteel 3500 Syn
Страница 2: ......
Страница 18: ...18...
Страница 19: ...General information 19...
Страница 20: ...20...
Страница 29: ...Control elements and connections 29...
Страница 30: ...30...
Страница 38: ...38...
Страница 39: ...Installation and commissioning 39...
Страница 40: ...40...
Страница 61: ...Welding 61...
Страница 62: ...62...
Страница 83: ...The arc air gouging parameters are the same as the welding parameters for MMA welding see page 96 83 EN...
Страница 84: ...84...
Страница 85: ...Easy Documentation 85...
Страница 86: ...86...
Страница 91: ...Setup settings 91...
Страница 92: ...92...
Страница 103: ...10 Fit the gas nozzle back onto the welding torch 103 EN...
Страница 105: ...Troubleshooting and maintenance 105...
Страница 106: ...106...
Страница 119: ...Appendix 119...
Страница 120: ...120...
Страница 144: ......