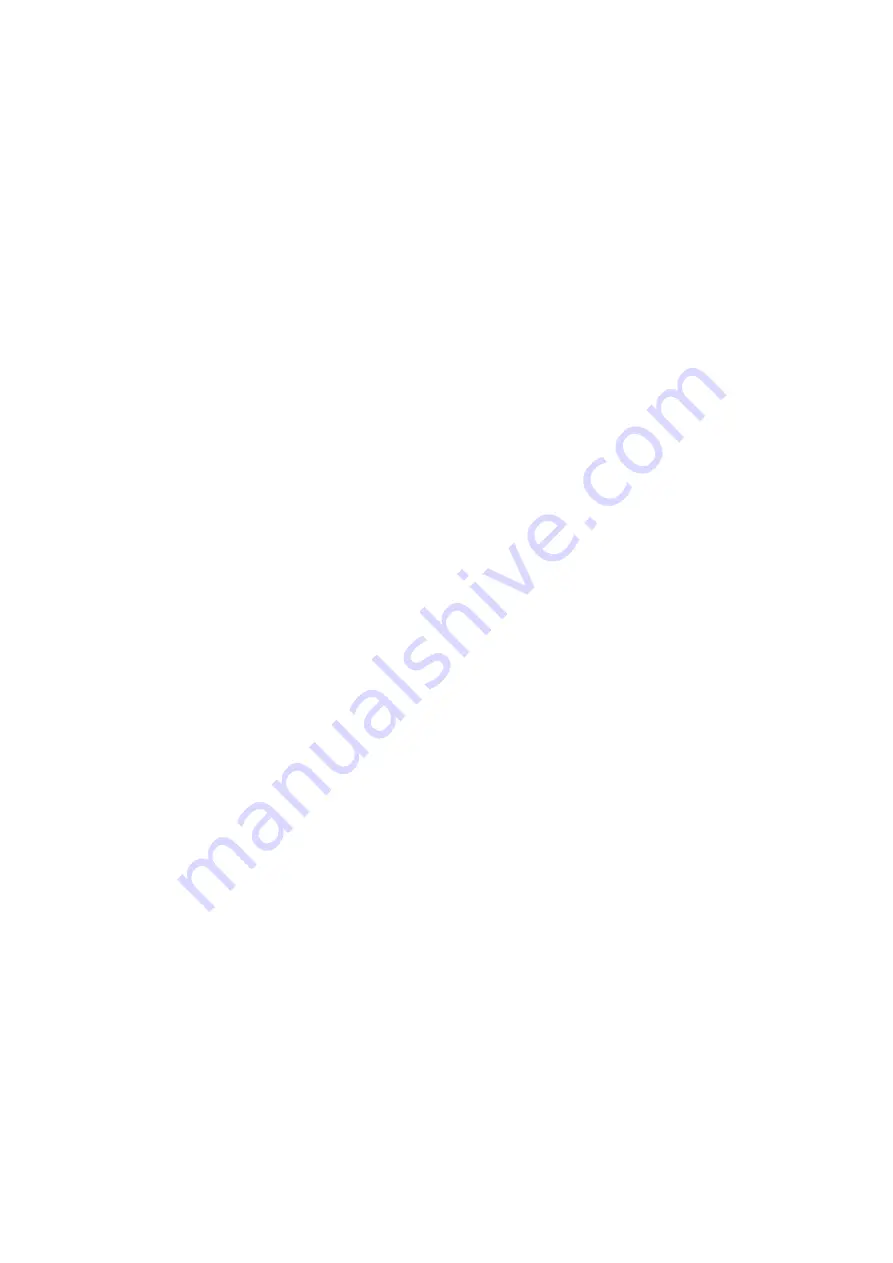
Parameter set transfer from one inverter to the other one
As an example, the copy of the basic internal user set
UI-0
from the source inverter to
the basic internal user sets
UI-0
of two other destination inverters is described in the
following steps :
a)
connect the control pod FRECON MINITERMINAL to the source inverter
b)
load (READ) the user set
UI-0
into the working area (active set)
c)
store (PROG) the active set into any external user set, for example into
UE-0
(the
copied set is now stored in EEPROM inside the control pod)
d)
disconnect the control pod from the source inverter and connect it to one of the
destination inverters
e)
load (READ) the external user set
UE-0
into the working area (active set)
f)
store (PROG) the active set into the destination internal user set
UI-0
g)
connect the control pod to the second destination inverter and repeat steps e) and f).
Factory sets
Factory sets contain the most common preset values of all functional parameters. The
user can use them or not. Any factory set can be loaded into the working area as active
set, there it can be eventuely modified and stored into any user set. Factory sets cannot
be overprogrammed.
The basic factory set
FA-0
contains the most frequently used setting of functional
parameters for the most common drives and loads with linear V/f characteristic. The
factory set
FA-1
contains the most frequently used setting of functional parameters for
the most common fans.
Initial setting of the active parameters in the working area
During the initialisation after the inverter is powered on, the data from the basic internal
user set
UI-0
are automatically loaded into the working area as active parameters,
independently on wheather the control pod is connected or not. This enables the user to
preset the initial setting of the drive.
If the user set
UI-0
is empty (not yet programmed), the contents of the basic factory set
FA-0
are automaticaly loaded instead of UI-0 during the initialisation.
10. Software compatibility
Since several versions of FIA-L control program has been already developed (standard
drives, high speed drives with output frequency up to 500Hz, drives with integrated PI-
regulators of speed dependent technological variables, etc.) and new and higher
software versions can occure in future, the two-level software compatibility checking is
used:
•
Software compatibility of an inverter and the connected control pod
This incompatibility is found out immediately after connecting the control pod to the
inverter as the error message
„Er.03“
is signalized on the display. This control pod
cannot operate with this inverter.
•
Compatibility of the control program and the parameter sets data format
The incompatible data format is found out when the user is trying to load the
incompatible parameter set into the working area. This failure is signalized by error
message „
Er.18
“ which indicates unusable data. This parameter set can be assumed
as an empty set.
12