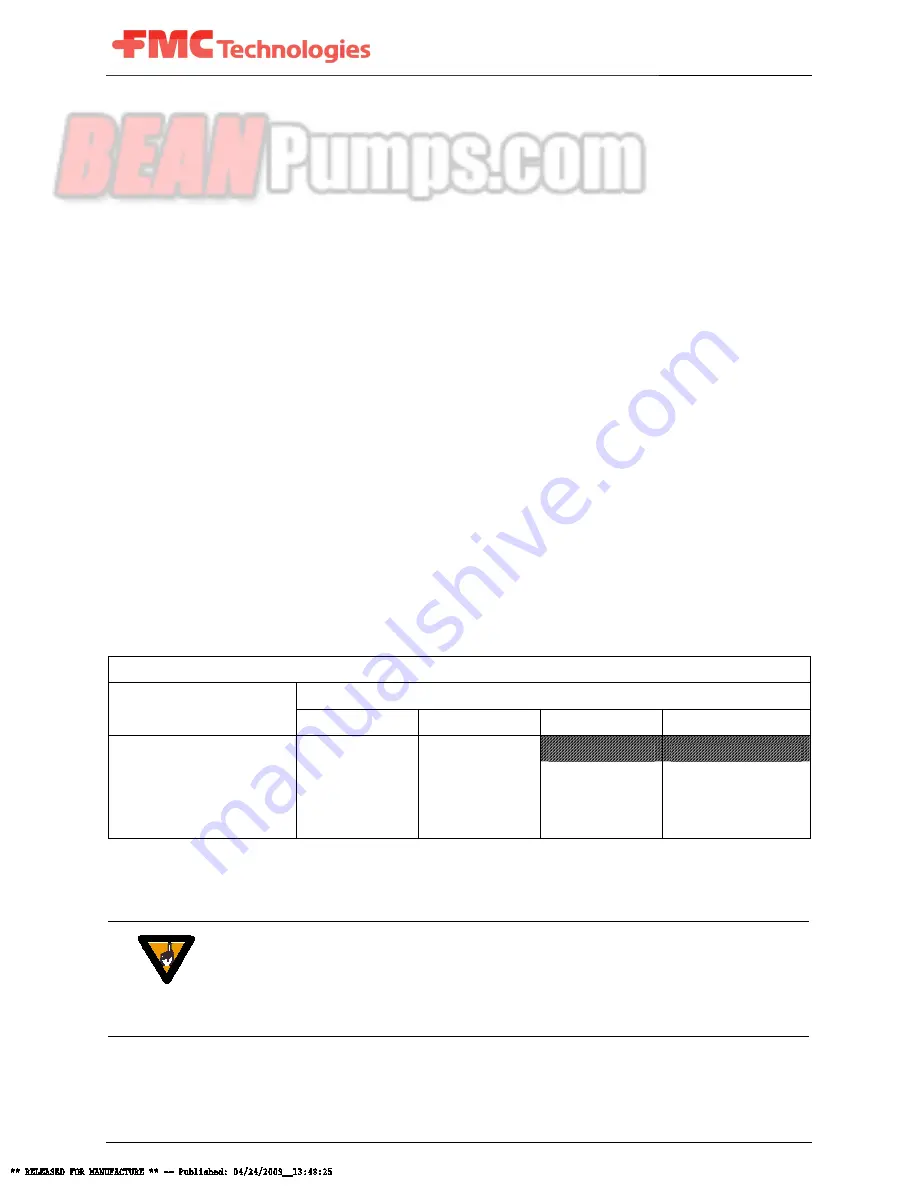
Doc No: OMM50001254
Rev: A Page 12 of 47
Subject to contractual terms and conditions to the contrary, this document and all the information contained herein are the confidential and exclusive
property of FMC Technologies, and may not be reproduced, disclosed, or made public in any manner prior to express written authorization by FMC.
The suction line must be configured so there are no high spots in the line where air
pockets can collect. These pockets may make the pump difficult to prime and cause
rough, erratic operation. A drain valve or plug should be installed at the low point of the
suction line to allow for draining before freezing conditions or for maintenance.
FMC recommends that all piping be supported independently of the pump. By
supporting the piping this way, vibrations are reduced and stress on the pump is kept to
a minimum. The use of elbows, nipples, unions, or other fittings should be minimized.
Make sure that all joints and connections are airtight. Air leaks reduce the capacity of
the pump and can result in cavitation, rough operation, and/or loss of prime. To help
isolate mechanical and hydraulic vibrations, FMC recommends the use of flexible pipe
couplings or hose connections between the pump and any rigid piping.
Always ensure that calculated system Net Positive Suction Head available, NPSHa,
exceeds pump Net Positive Suction Head required, NPSHr, by at least 5 feet (1.5
meters) of water for proper operation of the pump. NPSH requirements for each pump
model are provided on the product data sheets available through FMC or your
authorized FMC reseller. FMC does not recommend using the pump in static lift
conditions without prior factory approval.
3.4
Discharge Piping Recommendations
1. Route the discharge piping in as short and direct a route as possible. Use the
same pipe size as the outlet of the pump. In installations where the discharge
piping is in excess of 50 feet (15 meters) it is suggested to use the next larger
size pipe to minimize friction losses downstream of the pump.
Table 1: MAWP for Steel Pipe
Allowable Working Pressure For Steel Pipe (PSI @ 100F)
Pipe Schedule Number
Pipe Size (inches)
40
80
160
XX
3/8
1,700
3,800
1/2
2,300
4,100
7,300
12,300
3/4
2,000
3,500
8,500
10,000
1
2,100
3,500
5,700
9,500
14.5 psi = 1 Bar
CAUTION
Always use pipe or hose that is designed for your particular pressure requirements.
Inadequate pressure ratings can allow hose or pipe to fail, resulting in equipment damage
and possibly personal injury. Normal hose pressure ratings are clearly marked on the
outer surface of the hose. Working pressure ratings for steel pipe can be obtained from
the manufacturer or from the chart shown tin Table 1.