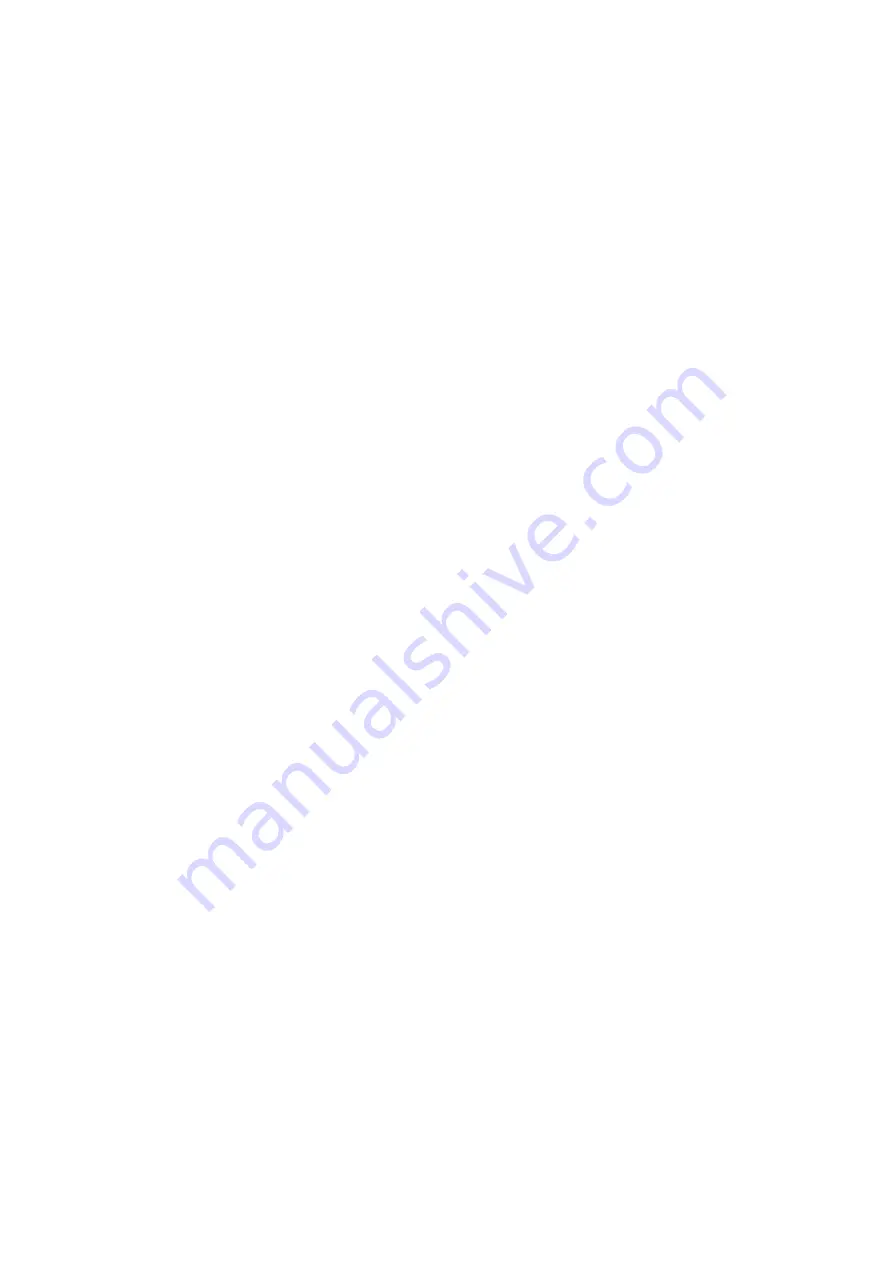
B. Glossary
134
Festo.P.BE-CMMS-ST-G2-HW-EN
1008NH
B.
Glossary
EMC
Electromagnetic compatibility (EMC) or electromagnetic interference (EMI) involves the
following requirements:
Interference
immunity
Sufficient interference immunity of an electrical system or electrical
device against external electrical, magnetic or electromagnetic
noise via lines or space.
Interference
emission
Sufficiently low interference emission of electrical, magnetic or
electromagnetic interference of an electrical system or an electrical
device on other devices in the environment via lines and space.