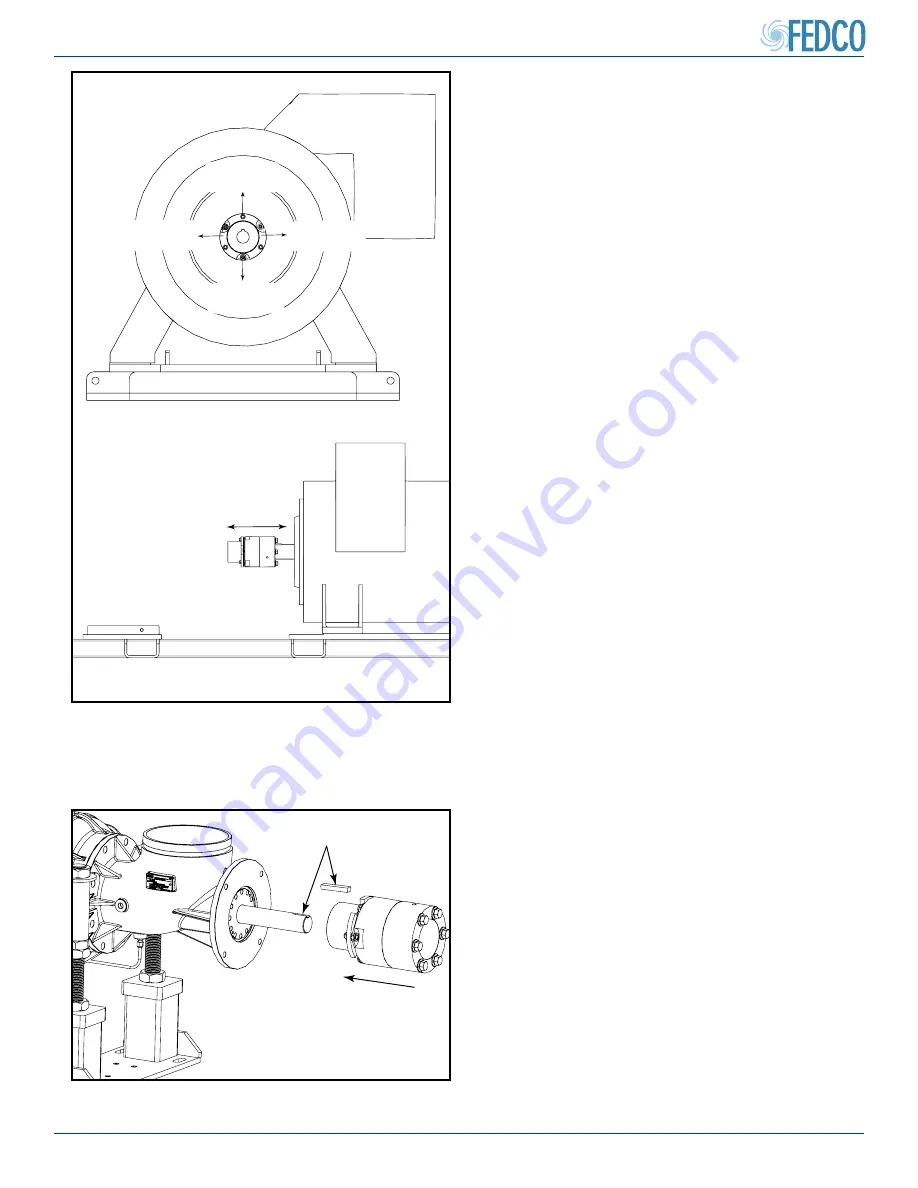
MSD
TM
Series
© Copyright 2018 Fluid Equipment Development Company | www.fedco-usa.com
-
23
-
Figure 34 - Install Dropout Coupling On Pump
Shaft
ANTI-SEIZE
8. Apply a system compliant anti-seize com-
pound and slide the dropout coupling over
the pump shaft with the pump shaft key.
NOTES:
The rounded end of the key must be
placed in the rounded end of the keyway.
Figure 33 - Check Dropout Coupling Fit On
Shaft
NO
MOVEMENT
NO
MOVEMENT
NO
MOVEMENT
NO
MOVEMENT
7. Inspect the dropout coupling’s radial and
axial fit. It should be tight with no visible
radial movement and slide smoothly on and
off the motor shaft
Pump Assembly Continued
SMOOTH MOVEMENT