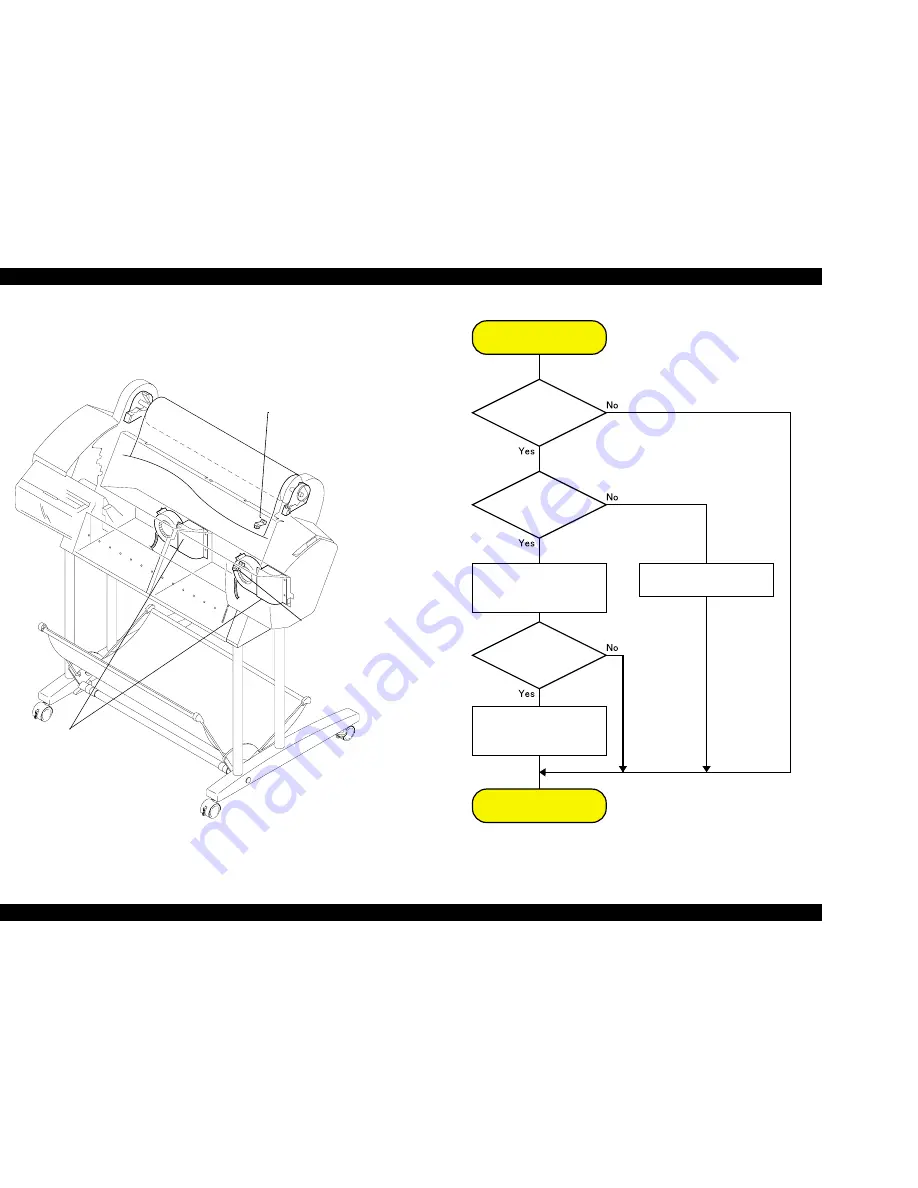
EPSON Stylus Pro 7500
Revision A
Operating Principles
Print Mechanism Components
66
(prevented from flying up) as it passes through the printer. The suction fans undergo air
flow control (fan rotation duty control), which is carried out by firmware control based on
the printer’s operating state (when paper is set and during printing, etc.) and the type of
paper used.
Figure 2-9. Paper Feed Mechanical Unit 2/2
The next page shows suction fan control during paper feed.
Figure 2-10. Paper Suction Fan Control
P-Rear sensor
P-Front sensor
paper suction fans
Is the
P_FRONT sensor on?
(Is paper present?)
Paper Suction
Fan Control
Paper Set
lever in released
(up) state?
Is the
P_REAR sensoron?
(Is paper present?)
Run the suction fans at
low speed and attract
the paper.
Stop the suction fans.
Run the suction fans
at high speed and
attract the paper.
End
Содержание Stylus Pro 7500
Страница 1: ...EPSONStylusPRO7500 Color Large Format Inkjet Printer SEIJ00005 SERVICE MANUAL ...
Страница 6: ...Revision Status Revision Issued Date Description Rev A August 31 2000 First Release ...
Страница 10: ...C H A P T E R PRODUCTDESCRIPTION ...
Страница 57: ...C H A P T E R OPERATINGPRINCIPLES ...
Страница 75: ...C H A P T E R TROUBLESHOOTING ...
Страница 95: ...C H A P T E R DISASSEMBLY ASSEMBLY ...
Страница 169: ...C H A P T E R 0 ADJUSTMENT ...
Страница 192: ...PSON Stylus Pro 7500 Revision A djustment Adjustment Steps 192 Figure 5 13 Adjustment Menu ...
Страница 235: ...C H A P T E R MAINTENANCE ...
Страница 241: ...C H A P T E R APPENDIX ...
Страница 258: ...PSON Stylus Pro 7500 Revision A ppendix Exploded View Diagram 258 Figure 7 2 Frame Assembly ...
Страница 259: ...PSON Stylus Pro 7500 Revision A ppendix Exploded View Diagram 259 Figure 7 3 Paper Feed Assembly ...
Страница 260: ...PSON Stylus Pro 7500 Revision A ppendix Exploded View Diagram 260 Figure 7 4 Head Assembly ...
Страница 261: ...PSON Stylus Pro 7500 Revision A ppendix Exploded View Diagram 261 Figure 7 5 Carriage Assembly ...
Страница 262: ...PSON Stylus Pro 7500 Revision A ppendix Exploded View Diagram 262 Figure 7 6 Frame Accessory ...
Страница 263: ...PSON Stylus Pro 7500 Revision A ppendix Exploded View Diagram 263 Figure 7 7 Maintenance Assembly ...
Страница 264: ...PSON Stylus Pro 7500 Revision A ppendix Exploded View Diagram 264 Figure 7 8 Ink Cartridge Holder Assembly ...
Страница 265: ...PSON Stylus Pro 7500 Revision A ppendix Exploded View Diagram 265 Figure 7 9 Cable Guide ...
Страница 266: ...PSON Stylus Pro 7500 Revision A ppendix Exploded View Diagram 266 Figure 7 10 Board Base Assembly ...
Страница 267: ...PSON Stylus Pro 7500 Revision A ppendix Exploded View Diagram 267 Figure 7 11 Cover Assembly ...
Страница 272: ......
Страница 273: ......
Страница 274: ......