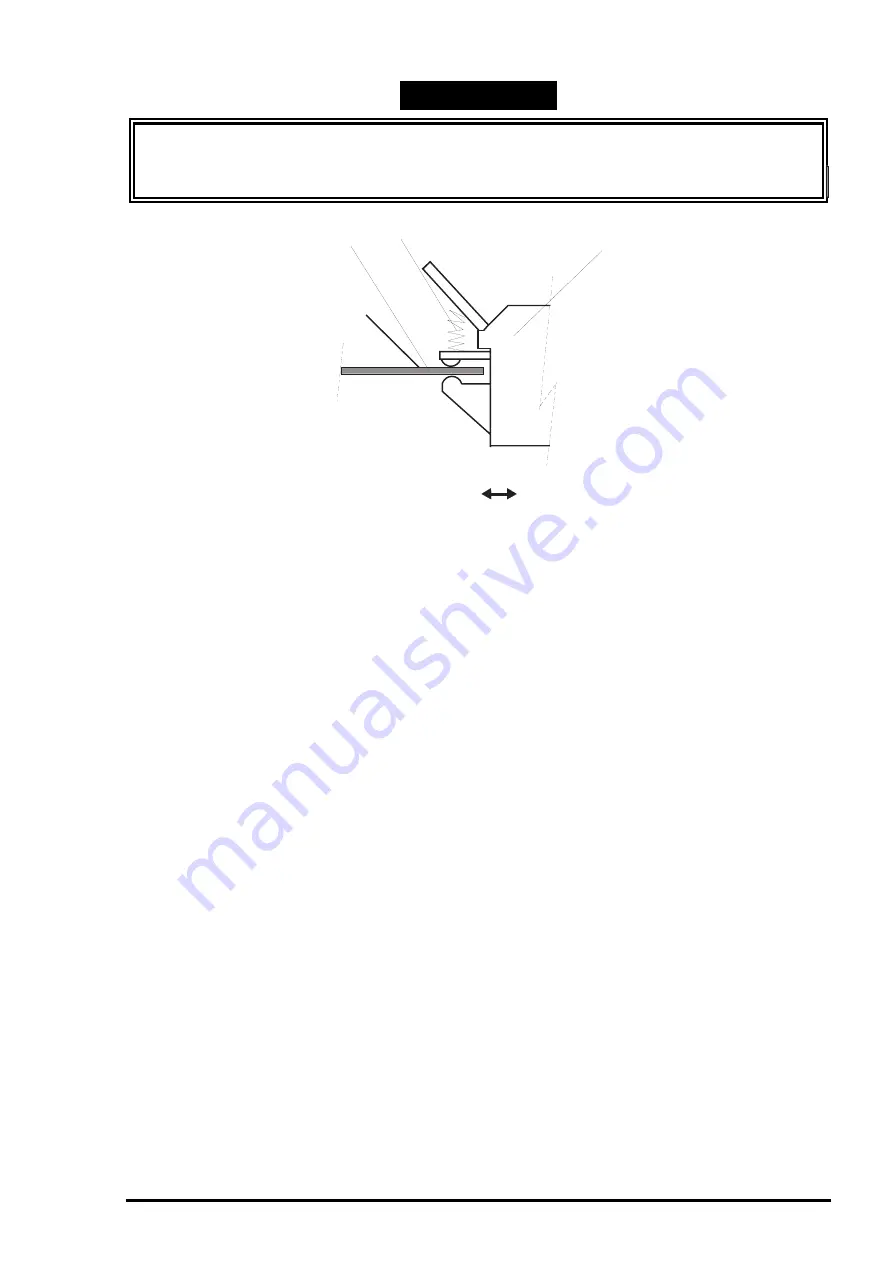
EPSON Stylus COLOR 3000
Rev. A
3-25
WORK POINT
When installing the edge guide unit to the printer mechanism unit, engage the edge guide
unit with the main bottom frame, as shown in Figure 3-22.
Be sure to fix the flange nuts with the specified adhesive. (See Chapter 6.)
Bottom Main Frame
Edge Guide Unit
Spring
Front
Rear
Figure 3-22.
Joining the Edge Guide Frame and Bottom Main Frame
Содержание Stylus COLOR 3000
Страница 5: ......
Страница 126: ......
Страница 127: ......
Страница 150: ...EPSON Stylus COLOR 3000 Rev A 6 5 1 1 1 2 3 4 4 4 4 4 4 Figure 6 1 Lubrication Points 1 ...
Страница 151: ...Maintenance Rev A 6 6 9 9 9 9 9 9 9 9 6 7 Figure 6 2 Lubrication Points 2 ...
Страница 152: ...EPSON Stylus COLOR 3000 Rev A 6 7 CR Motor 1 CR Motor Fan Indent side facing outside 2 2 Figure 6 3 Adhesive Points ...
Страница 161: ...EPSON Stylus COLOR 3000 Rev A A 8 ...
Страница 162: ...Appendix Rev A A 9 A 2 Circuit Diagrams Figure A 2 C203 MAIN B Board Circuit Diagram 1 2 ...
Страница 163: ...EPSON Stylus COLOR 3000 Rev A A 10 ...
Страница 164: ...Appendix Rev A A 11 Figure A 3 C203 MAIN B Board Circuit Diagram 2 2 ...
Страница 165: ...EPSON Stylus COLOR 3000 Rev A A 12 ...
Страница 169: ...EPSON Stylus COLOR 3000 Rev A A 16 A 3 Component Layout Figure A 7 C203 MAIN B Board Component Layout 1 ...
Страница 170: ...Appendix Rev A A 17 Figure A 8 C203 MAIN B Board Component Layout 2 ...
Страница 171: ...EPSON Stylus COLOR 3000 Rev A A 18 Figure A 9 C203 PNL Board Component Layout ...
Страница 172: ...Appendix Rev A A 19 Figure A 10 C172 PSB Board Component Layout ...
Страница 173: ...EPSON Stylus COLOR 3000 Rev A A 20 Figure A 11 C172 PSE Board Component Layout ...
Страница 174: ...Appendix Rev A A 21 A 4 Exploded Diagrams Figure A 12 Stylus 3000 Exploded Diagram 1 ...
Страница 175: ...EPSON Stylus COLOR 3000 Rev A A 22 Figure A 13 Stylus 3000 Exploded Diagram 2 ...
Страница 176: ...Appendix Rev A A 23 Figure A 14 Stylus Color 3000 Exploded Diagram 3 ...
Страница 177: ...EPSON Stylus COLOR 3000 Rev A A 24 Figure A 15 Stylus Color 3000 Exploded Diagram 4 ...
Страница 180: ...EPSON SEIKO EPSON CORPORATION ...