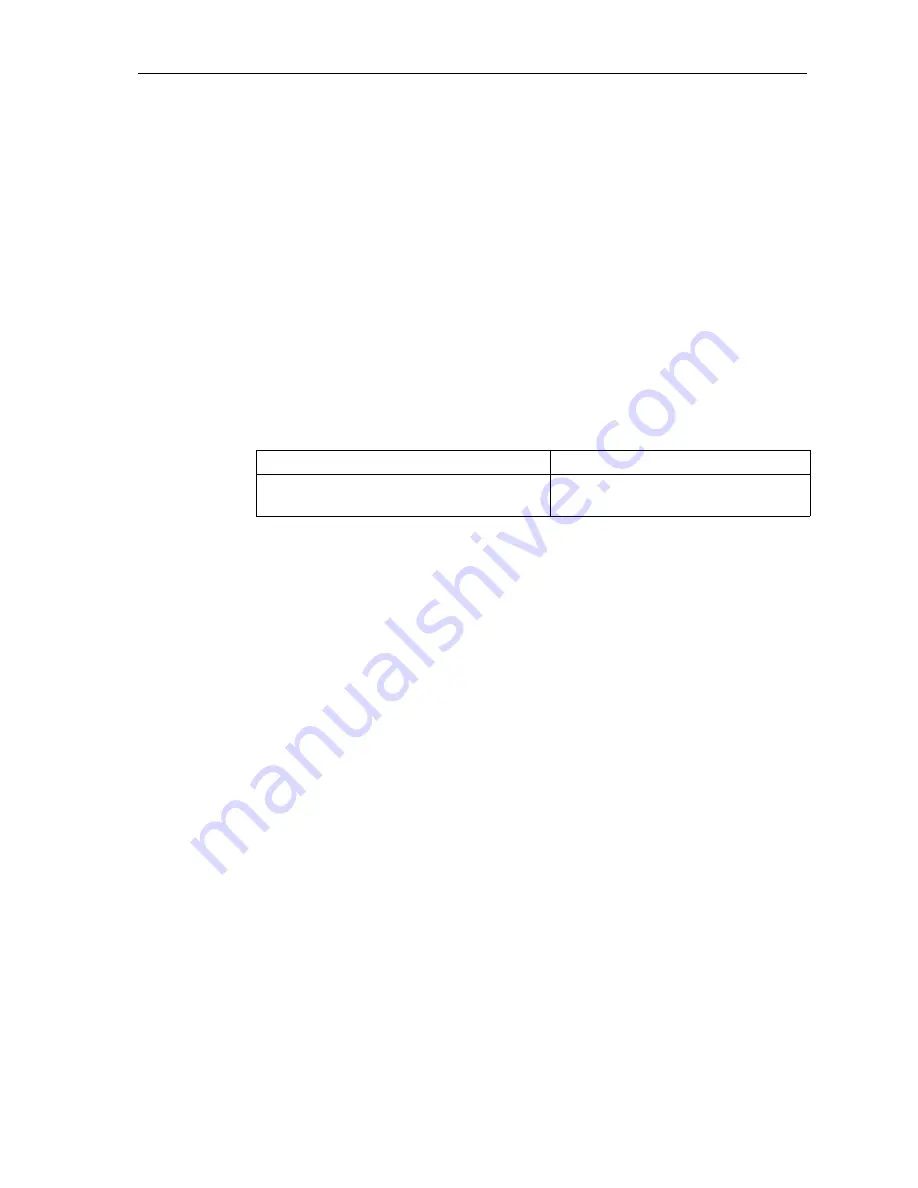
40
Entek IRD 6652 DSP Protection Monitor
Testing Calibration and Relays
Testing Calibration and Relays
To test the monitor’s calibration, you connect a known signal to the backplane of the
monitor and read the signal from the display on the front of the monitor. You can test the
relays by changing the input signal to cause a relay to change state.
Signal Inputs for Testing
When testing any of the 6600 protection monitors, you must use the correct input signal. For
example, most 6652 DSP configurations for use with an accelerometer expect a gap voltage.
If the input signal does not include the expected gap voltage, the monitor signals a
transducer fault. Please use the following guidelines when setting the input signal:
l
Set the input signal to a sine wave with a frequency of 100 Hz. This allows you to use
the transducer sensitivities in the table below.
l
Note that the sensitivity is given in mVRMS. This is the most common setting for
millivolt readings on a multimeter. Make sure your multimeter is set to read voltage in
mVRMS.
l
Calculate the full scale input amplitude using the following information. The menu
options are from the RANGE (page 26) and TX OK submenus (page 30).
Transducer type
________________
Programmed parameter
(UNITS 1)
________________
Programmed range
(SCALE 1)
________________
Gap voltage low
(TX LO 1)
________________
Gap voltage high
(TX HI 1)
________________
Use the following formula to find the input amplitude:
l
Set the input signal bias to halfway between the TX LO and TX HI settings (“TX OK
submenu” on page 30). You can get around the need for a gap voltage by setting TX LO
to -5.00 and TX HI to +5.00. If you do this, make sure you reset the TX LO and TX HI
values correctly before putting the monitor back into service.
Transducer
Sensitivity
403 and 1900 non-contact probes (peak to
peak)
70.7 mVRMS/mil (2.78 mVRMS/µm)
programmed range
transducer sensitivity (from table)
×
full scale input amplitude
=