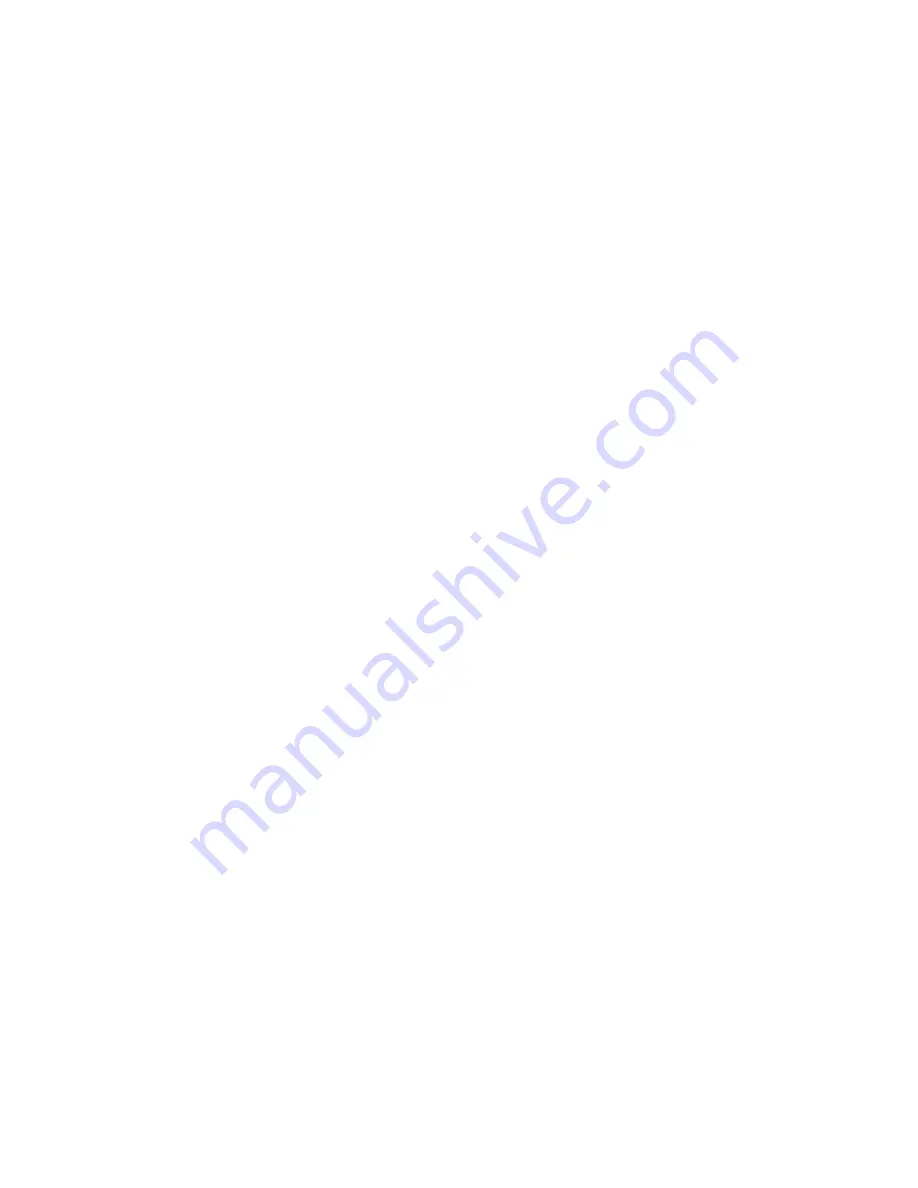
7
I. TROUBLESHOOTING:
1. To assist in becoming familiar with the function and usage of
the valve, please refer to Figures 6 and 7.
2. Check electrical operation of valve. Make certain pushbutton
control station is in correct working order. Check spool valve
for "clicking" sound which indicates operating solenoids.
3. Make certain that pilot pressure has been correctly set, or
can be adjusted, and that the valve has been checked for
external oil leakage.
4. Inability to obtain any pressure may be the result of
damaged connector seals, failed relief valve components
(items 9,14,15), sticking solenoid spool (item 48), or the pilot
pressure setting is too low (less than 500 psi [34 bar]).
5. Pressure leaks that are consistent and increase proportionally
with increasing pressure ranges are usually the result of
leaking gaskets or threaded surfaces such as NPTF fi ttings
or plugs.
6. Ball seat leakage is often erratic and intermittent and is
caused by contaminants trapped on the sealing edge. Over
time, as wear occurs, these seats need to be replaced.
7. If the valve malfunction is identical in both directions, check
the pilot pressure setting by inserting a 0-5000 psi [0-344
bar] gauge in the port labeled “pilot pressure” on the side
of the valve. Advance or retract the valve and check that
the pilot pressure is between 1200-1400 psi [82-96 bar]
and adjust the pilot pressure adjustment screw (item 35)
accordingly to either increase or decrease the pressure
setting. If no improvement is noticed, replace the spring
(item 37), pilot seat (item 21) and copper gasket (item 20).
8. If the pilot setting cannot be adjusted down, it can indicate
the O-ring and backup are installed on the wrong side of
each other on item 38 or indicates a severe leakage in the
pilot ball seat (item 21) or a broken spring (item 22). Replace
immediately.
9. If the valve fails to build to maximum pressure in both
directions, the pilot pressure may be too low. Low pilot
pressure may be caused by leakage through the spool
valve or a leaking pilot relief valve ball seat in the valve body
(items 9,7), or the pilot setting is too low and needs to be
adjusted up (see paragraph 7 above).
10. If valve builds pressure simultaneously in both directions,
this may be the result of a broken pin in either one or both
of the directional piston assemblies (item 39) and /or the
pilot piston (item 38), or the pilot pressure setting (item 35) is
too low, or that the pilot spring (item 37) has broken. Either
readjust the pilot setting or replace parts immediately.
11. If the valve fails to change direction immediately, this may be
due to worn springs (item 19) between the ball directional
circuits, or a problem with the directional pistons (item 39),
either a broken pin or failed seal, replace.
12. If cylinder will not build pressure either in the advance
or retract position. Check the pilot pressure setting (set
between 1200-1400 psi [82-96 bar]. Another possible cause
is the upper seat and/or the pilot seat is worn and must
be replaced. If the cylinder creeps in the "Neutral" position
or "Hold" position (VE33 only), this may suggest a worn
upper or lower valve seat or spring, (Item 19), which must
be replaced.
13. The cylinder is hung-up in either the advance or retract
position. The problem is usually a symptom of contaminated
hydraulic oil. The system should be drained and refi lled with
fresh ENERPAC hydraulic oil. The spool valve should then
be centered manually by depressing the pin actuator on
either side of the spool valve. Now press the “up” arrow and
“down” arrow several times checking the valve operation
and cylinder movement. Another cause might be that the
pilot pressure setting is too high (greater than 1400 psi [96
bar]), in which case the pilot pressure relief valve must be
reset to 2200 psi [151 bar] ±200 psi [±14 bar].
II. DISASSEMBLY:
1. Remove solenoid assembly (item 48) by removing the 4
screws (item 49) and lockwashers (item 49A). Note: do not
disassemble solenoid valve!
2. Disassemble the valve assembly by fi rst removing the acorn
nut (item 47), lock nut (item 46), copper gaskets (item 45),
adjustment screw (item 35), 6 screws (item 43). Separate
cover (item 32) from body (item 7). Remove seals (items
42,41), directional springs (item 40) from bottom of cover.
Remove the pilot piston assembly (item 38), spring (item
37), and spacer (item 36). Inspect all seals for damage. If in
doubt replace with new items supplied with repair kit.
3. Disassemble the advance and retract directional pistons
(item 39).
4. Disassemble the pilot section by removing the pilot seat
(item 21), copper gasket (item 20), ball (item 18), spacer
(item 23), and spring (item 22). Disassemble the advance
and retract sections by removing the upper seats (item 21),
copper gasket (item 20), ball (item 18), spring and spacer
assembly (item 19), ball (item 18), lower seat (item 17). Use
special tool No. TXK200466-3, and copper gasket (item 16).
Discard used copper gaskets and replace with new items
supplied with repair kit.
5. Disassemble the pilot relief section by removing the plug
(item 13), adjustable screw (item 12), spring (item 11), guide
(item 10), and ball (item 9).
6. Disassemble the B port relief section by removing the plug
(item 13), adjustment screw (item 12), spring (item 15), ball
guide (item 14) and ball (item 9).
7. It is not necessary to remove the numerous pipe plugs found
on the cover and body unless contamination is trapped
within the parts and need to be fl ushed out. Replace with
new items supplied with repair kit.
8. Disassemble the port manifold (item 52) from the body (item
7) by removing the 4 screws (item 5). Inspect the seals (item
27,31) and replace if necessary.
9. Inspect the cover (item 32) and body (item 7), after cleaning,
for damage. Replace if necessary.
TROUBLESHOOTING AND REPAIR OF VE43/VE33/VE43-115/VE33-115 ELECTRIC VALVE
In diagnosing malfunctioning valves, certain symptoms may be common not only to valves, but often to hydraulic equipment in
general. Before repairing the valve, mount a VM32 on the pump and verify that the problem is not with the pump.