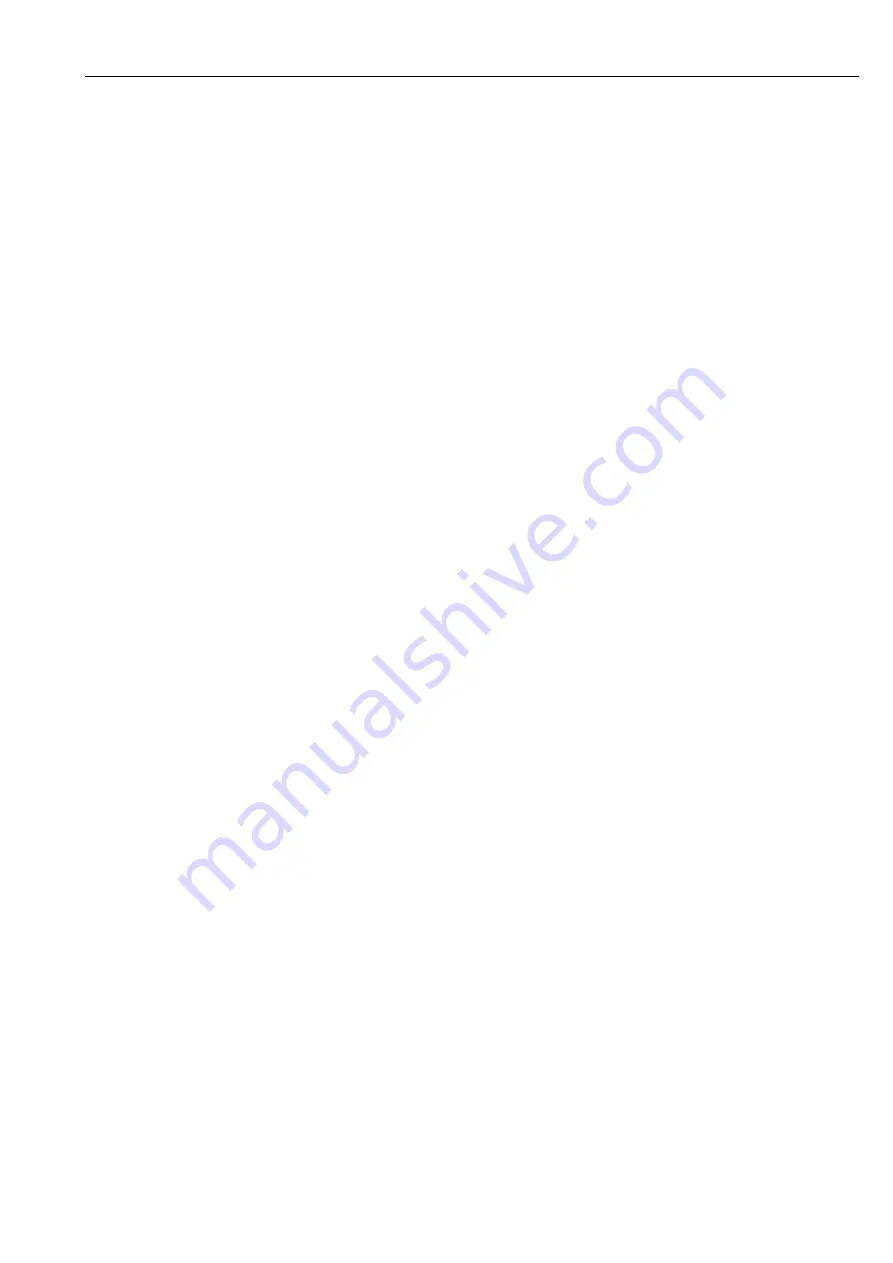
Levelflex M FMP43 with PROFIBUS PA
Operation
Hauser
47
5.5.5
Acyclic data exchange
Acyclic data exchange allows device parameters to be changed independently of the communication
between the device and a PLC.
Acyclic data exchange is used
• to transmit device parameters during commissioning and maintenance;
• to display measured values that are not acquired in cyclic traffic.
There are two types of acyclic data exchange:
Acyclic communication with a Class 2 master (MS2AC)
In the case of MS2AC, a Class 2 master opens a communication channel via a so-called service
access point (SAP) in order to access the device. Class 2 masters are for example:
• ToF Tool
• FieldCare
• PDM
Before data can be exchanged via PROFIBUS, however, the Class 2 master must be made aware of
the parameters contained within the field device. This can be done by:
• a device description (DD)
• a device type manager (DTM)
• a software component within the master, which accesses the parameters via slot and index
addresses.
!
Note!
• The DD or DTM is supplied by the device manufacturer.
• The number of Class 2 masters that can simultaneously access a device, is determined by the
number of SAPs that the device can provide.
• The use of a Class 2 master increases the cycle time of the bus system. This must be taken into
consideration when the control system or PLC is programmed.
Acyclic communication with a Class 1 master (MS1AC)
In the case of MS1AC, a Class 1 master that is already communicating cyclically with a device opens
a communication channel via SAP 0x33, a special access point for MS1AC. As is the case for a Class
2 master, the parameter is read or written via the slot and index.
!
Note!
• At the time of writing, there are only a few PROFIBUS masters that support this type of
communication.
• Not all PROFIBUS field devices support MS1AC.
"
Caution!
Permanent writing of parameters, e.g. with every cycle of the application program, must be avoided,
since this can drastically reduce the life of the device.
Acyclic write parameters are stored electrically in the RAM (EEPROM, Flash...). The RAM modules
are design for a limited number of write operations only. In standard operation without MS1AC, i.e.
during parametrisation of the device, the number of write operations is negligible when compared
to the limit. If the application program is badly designed, however, this limit can be reached quickly,
and the RAM will fail
The Levelflex M supports MS2AC communication with two SAP´s.
The Levelflex M does not support MS1AC communication.
Содержание Levelflex M FMP43
Страница 4: ...Brief overview Levelflex M FMP43 with PROFIBUS PA 4 Endress Hauser...
Страница 104: ...Appendix Levelflex M FMP43 with PROFIBUS PA 104 Endress Hauser...
Страница 106: ...Levelflex M FMP43 with PROFIBUS PA Index 106 Endress Hauser...
Страница 108: ...www endress com worldwide BA358F 00 en 07 07 No 71041163 CCS FM SGML 6 0 ProMoDo 71041163...