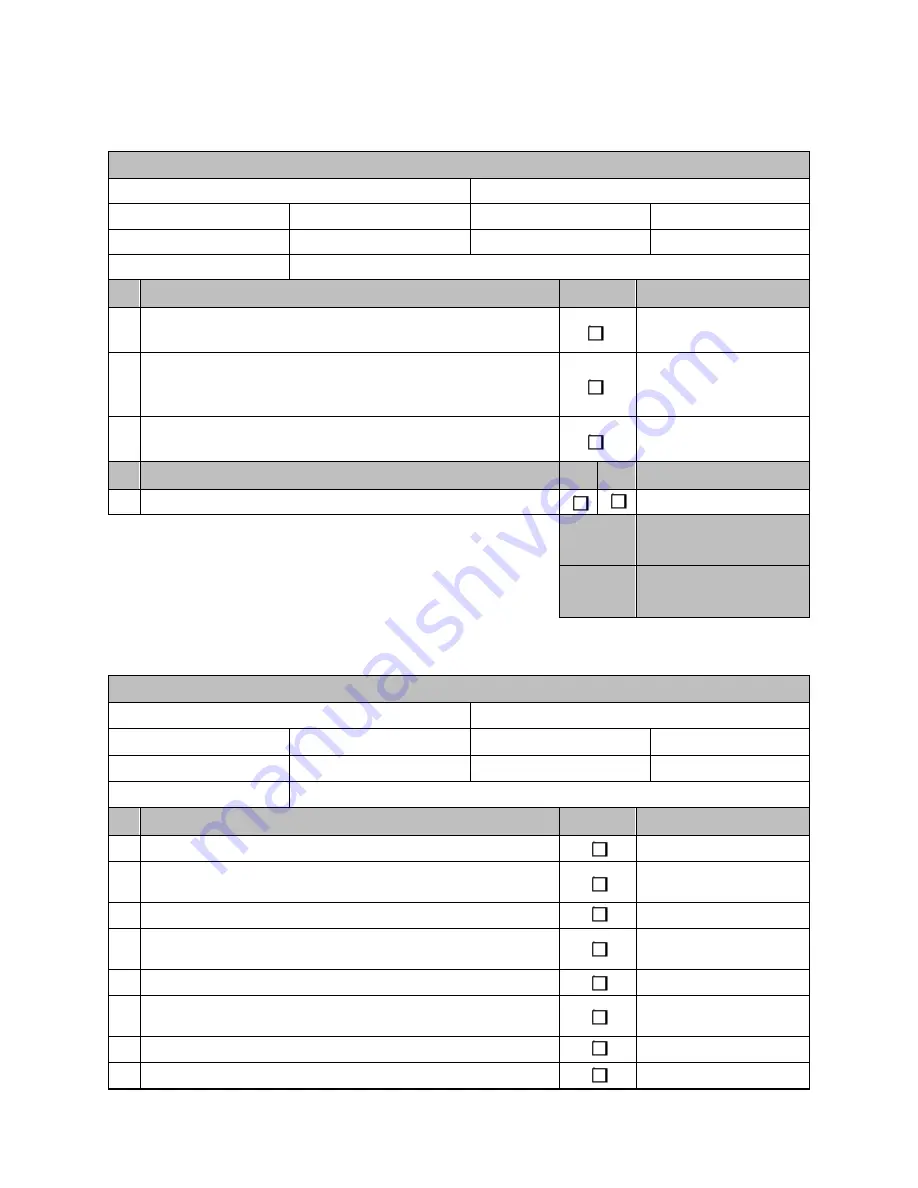
User Manual
Appendix B
GFK-2843A
Jan 2020
checklists
102
B-2.3
Startup
Checklist for startup of the safety module
Device type/equipment identification
Version: HW/FW/FW
Date
Author
Test engineer
Remark
No. Requirement (mandatory)
Yes
Remark
1
Was startup completed according to the specifications (specifications
from the planning phase or according to the user manual)?
2
During startup, is it ensured that any person starting hazardous
movements intentionally can only do so with a direct view of the danger
zone?
3
Have safety distances that must be observed been calculated according
to the response and delay times implemented?
No. Requirement (optional)
Yes No Remark
4
Date
Signature (author)
Date
Signature (test engineer)
B-2.4
Validation
Checklist for validating the safety module
Device type/equipment identification
Version: HW/FW/FW
Date
Author
Test engineer
Remark
No. Requirement (mandatory)
Yes
Remark
1
Have all the mandatory requirements for the "Planning" checklist been met?
2
Have all the mandatory requirements for the "Assembly and electrical
installation" checklist been met?
3
Have all the mandatory requirements for the "Startup" checklist been met?
4
Does the parameterization of the safe outputs correspond to the version and the
actual connection of the controlled device?
5
Has the assignment of the actuators to the safety logic outputs been checked?
6
Has a function test been performed to check all safety functions, in which the
module is involved?
7
Have measures been taken to achieve a specific Cat.?
8
Do all cables correspond to the specifications?