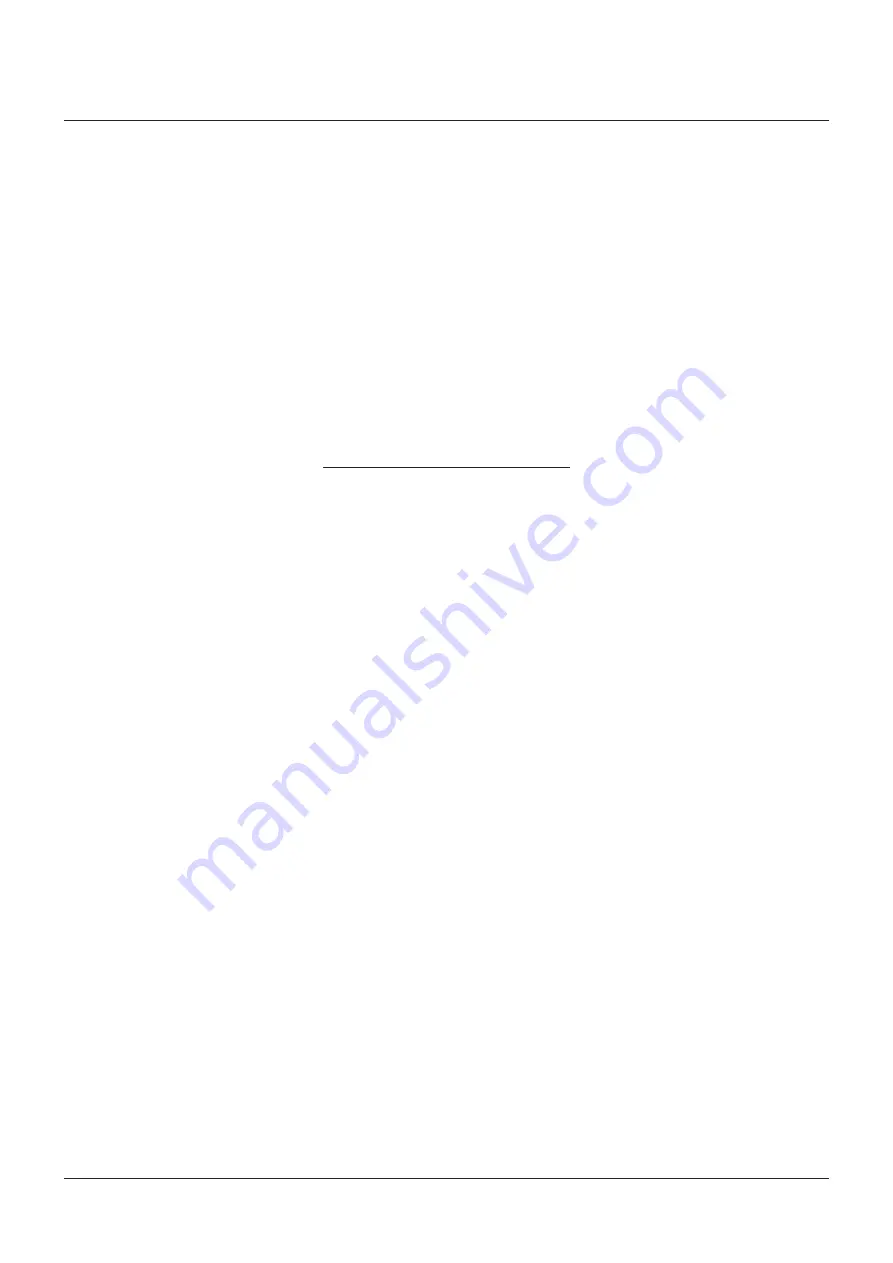
22
Crosby
STylE JOS-E, JBS-E, JlT*-JBS-E, JlT*-JOS-E ValVES
InstallatIon and MaIntenance InstructIons
10.1.2 Distortion from piping strains
Valve bodies can be distorted by
excessive piping loads causing seat
leakage� Both inlet and discharge
piping must be supported properly and
anchored so that high bending loads are
not transmitted to the valve body�
10.1.3 Operating pressure too close to set
pressure
a carefully lapped metal-to-metal
seated valve will be commercially
tight at a pressure approximately ten
percent under the set pressure or 5 psi,
whichever is greater� Consequently, this
minimum pressure differential should be
maintained between set and operating
pressure to avoid seat leakage problems�
10.1.4 Chatter
Oversized valves, excessive pressure drop
in the inlet lines, restrictions in the inlet
line, too great a build up of back pressure
or pulsating inlet pressure will cause
instability to the pressure relief valve� In
such installations, the pressure under the
valve disc may be great enough to cause
the valve to open but, as soon as flow is
established, the pressure drops allowing
the valve to close immediately� This cycle
of opening and closing sometimes occurs
at very high frequency causing severe
seat damage, sometimes beyond repair�
Proper valve selection and installation
techniques are paramount to reliable
valve performance�
10.1.5 Incorrectly adjusting lifting gear
a space of
1
/
16
inch minimum should
always be provided between the lifting
device and the spindle lift nut� Failure to
provide sufficient clearance may result in
inadvertent contact causing a slight shift
in the opening pressure�
11 eMerson field serViCe and rePair
PrograMs
Emerson field service provides on-site, in line
testing and repair capability for all types of
pressure relief devices�
11.1 Parts
Emerson will help you establish the right mix of
on-site spares with Emerson’s own distribution
and manufacturing support�
11.2 Training
Emerson offers intensive factory or on-
site seminars to improve maintenance and
application skills�
11.3 Testing
Emerson has the capability to evaluate
pressure relief valve operability either in the
field or at various Emerson facilities� Special
qualifications programs may also be conducted
in our laboratories�
11.4 Contract management
Emerson will combine a group of services to
satisfy your special maintenance needs�
Warning
The product is a safety related component
intended for use in critical applications.
The improper application, installation or
maintenance of the product or the use of parts or
components not manufactured by Emerson may
result in failure of the product. The advice of a
qualified engineer should be sought prior to any
use of the product.
Any installation, maintenance, adjustment,
repair or test performed on the product must be
done in accordance with the requirements of all
applicable codes and standards.
The information, specifications and technical data
(the 'Specifications') contained in this document
are subject to change without notice. Emerson
does not warrant that the specifications are
current and assumes no responsibility for the use
or misuse thereof.
The purchaser should verify that there have been
no changes to the specifications prior to use.
10.1.6 Other causes of seat leakage
Improper alignment of the spindle, too
much clearance between the valve spring
and the spring washers, or improper
bearing contact between the adjusting
bolt and the spring washers, spindle
and disc holder or spindle and lower
spring washer may cause seat leakage
problems� Spindles should be checked
for straightness and springs and spring
washers should be fitted properly and
kept together as a spring assembly�
10.1.7 Corrosion
Corrosion may result in pitting of valve
parts, failure of various valve parts, build
up of corrosive products and general
deterioration of the valve materials�
generally, corrosive attack is controlled
through selection of suitable materials
or by employing a bellows seal to isolate
the valve spring, adjusting bolt, spindle
and guiding surfaces from the corrosive
attack of the process fluid�
Environmental corrosion attacks all
exposed surfaces, including studs and
nuts� In general, the materials required
for a particular service are dictated
by the temperature, pressure and the
degree of corrosion resistance required�
Neither Emerson, Emerson automation Solutions, nor any of their affiliated entities assumes responsibility for the selection, use or maintenance of any product�
Responsibility for proper selection, use, and maintenance of any product remains solely with the purchaser and end user�
Crosby is a mark owned by one of the companies in the Emerson automation Solutions business unit of Emerson Electric Co� Emerson automation Solutions, Emerson
and the Emerson logo are trademarks and service marks of Emerson Electric Co� all other marks are the property of their respective owners�
The contents of this publication are presented for informational purposes only, and while every effort has been made to ensure their accuracy, they are not to be construed
as warranties or guarantees, express or implied, regarding the products or services described herein or their use or applicability� all sales are governed by our terms and
conditions, which are available upon request� We reserve the right to modify or improve the designs or specifications of such products at any time without notice�
Emerson�com/FinalControl