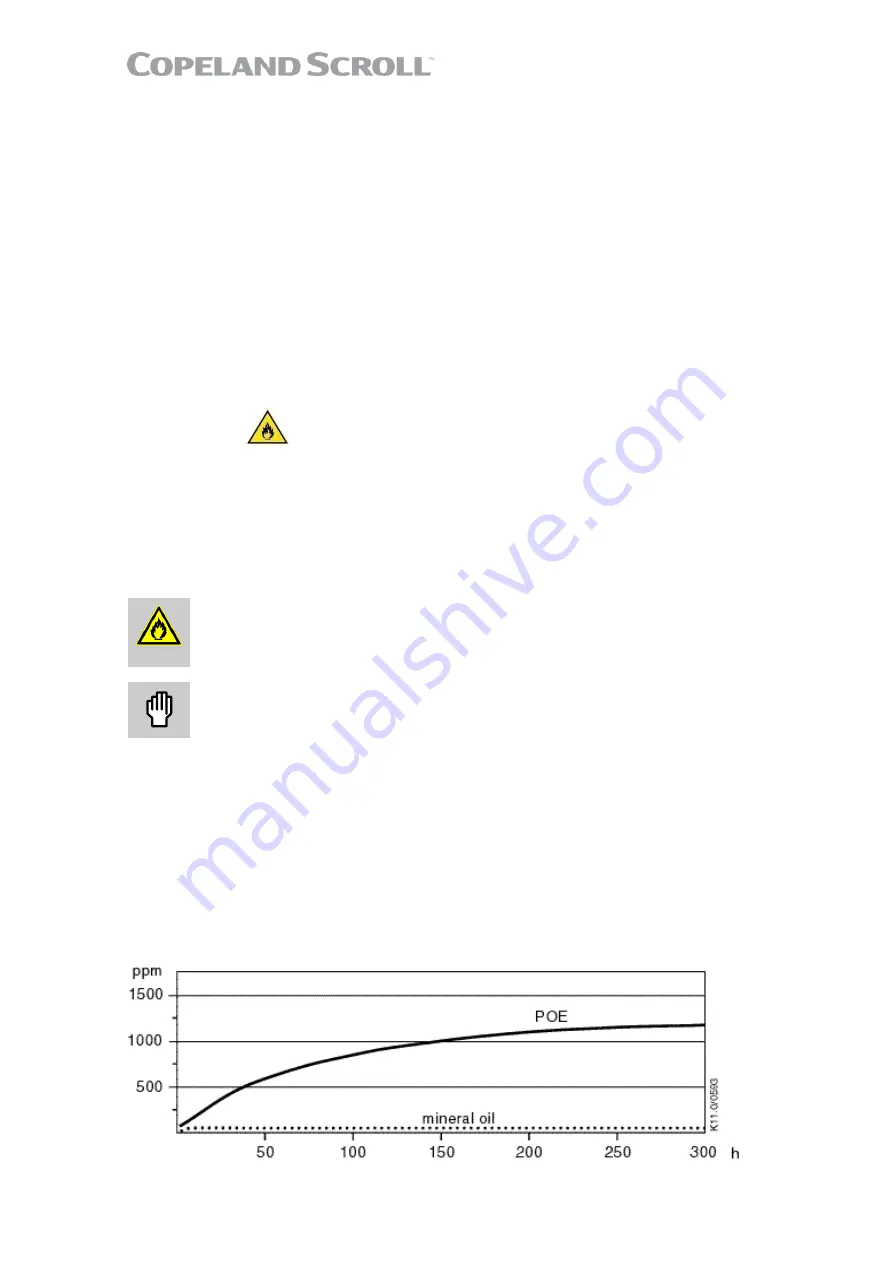
30
C6.2.38/0719/E
▪
Recover the refrigerant from the system using a suitable recovery unit. During this action the
compressor crankcase heater should be energized - immediately de-energize in case an
explosive atmosphere is detected.
▪
Do not allow the recovery unit to recover below atmospheric pressure. Make sure the low-
pressure switch that stops the recovery process is not set below 0.5 bar(g).
▪
At this pressure some refrigerant will still be in the system. Therefore, before opening the system,
pressurize to 1 bar(g) with dry nitrogen.
▪
Open the system with a cutting tool and flush the entire system with dry nitrogen.
▪
Disassemble the compressor with a cutting tool. Drain and recover compressor oil properly. Flush
the compressor with dry nitrogen for a few minutes.
▪
The compressor should be returned free of oil and with connections open - do not close
connections with plugs.
▪
Properly collect and secure the oil. Provide information about the quantity of oil drained from the
compressor and its colour. Ideally, send a good picture.
▪
Dispose of the oil according to local rules and regulations.
▪
Use a proper cardboard box package when preparing the compressor for shipment. Place
warning icons
on each side and on the top of the box. Mention the following message on
the box:
"Warning! Hydrocarbon compressor for analysis"
.
▪
The compressor shipment has to be kept in the upright position
– mark it accordingly.
▪
If more than one compressor has to be returned, each compressor has to be packed individually.
NOTE: Check with your transport company that all the requirements that apply to such
shipments are complied with.
6.7 Lubrication and oil removal
WARNING
Air/R290 refrigerant mixture in a potentially flammable atmosphere! Fire
hazard!
Use suitable recovery unit and recycling bottles also for oil disposal
as R290 refrigerant may still be solved in the oil.
CAUTION
Chemical reaction! Compressor destruction!
Do not mix up ester oils with
mineral oil and/or alkyl benzene.
The compressor is supplied with an initial oil charge. The standard oil charge for use with refrigerant
R290 is a polyolester (POE) lubricant. See nameplate for original oil charge shown in litres. A field
recharge is from 0.05 to 0.1litre less.
One disadvantage of POE is that it is far more hygroscopic than mineral oil
– see
Figure 21
. Only
brief exposure to ambient air is needed for POE to absorb sufficient moisture to make it unacceptable
for use in a refrigeration system. Since POE holds moisture more readily than mineral oil it is more
difficult to remove it through the use of vacuum. Compressors supplied by Emerson contain oil with
low moisture content, and it may rise during the system assembling process. Therefore, it is
recommended that a properly sized filter-drier is installed in all POE systems. This will maintain the
moisture level in the oil to less than 50 ppm. If oil is charged into a system, it is recommended to use
POE with moisture content no higher than 50 ppm.
Figure 21: Absorption of moisture in ester oil in comparison to mineral oil in ppm by weight at 25° C and 50% relative
humidity (h=hours)