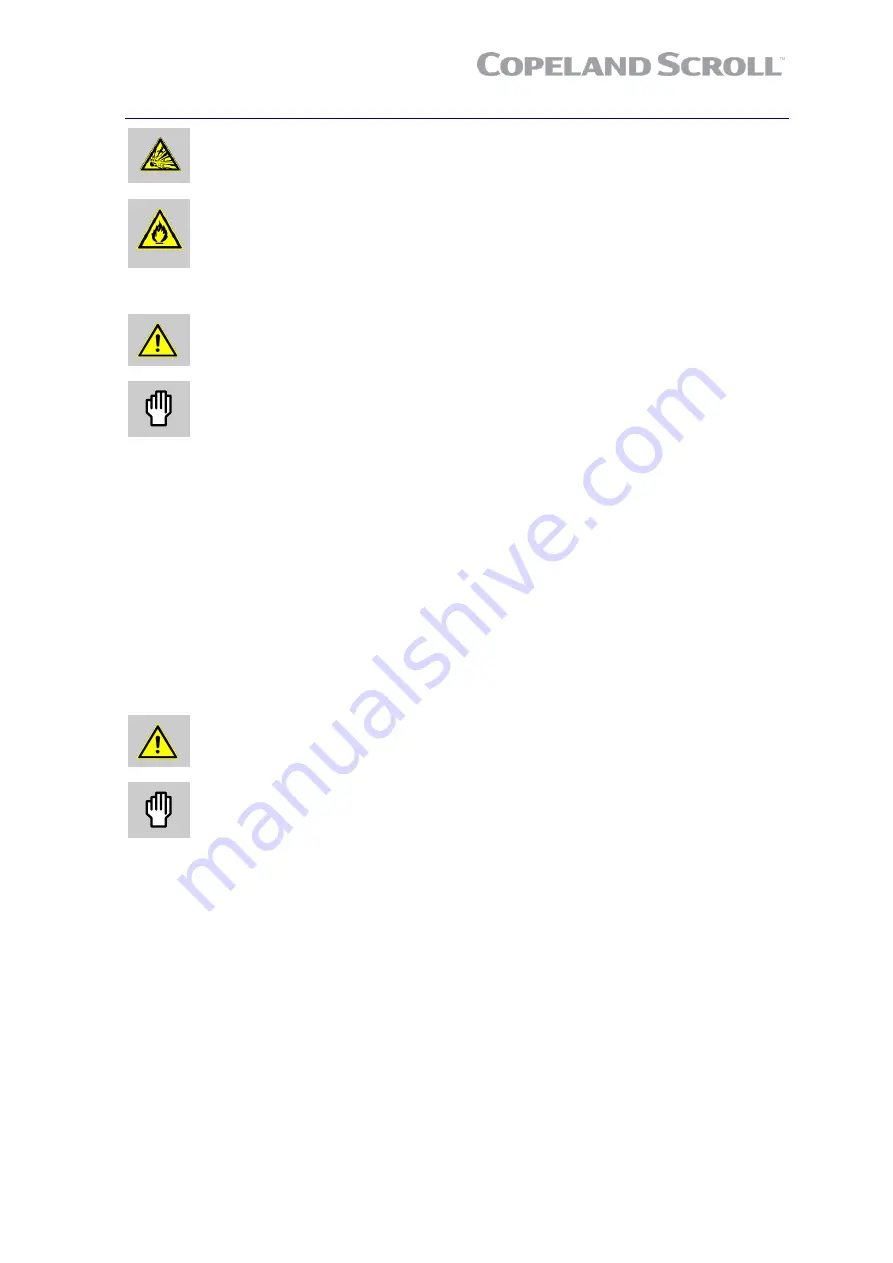
C6.2.38/0719/E
23
5
Start-up & operation
WARNING
Diesel effect!
Compressor destruction!
The mixture of air and oil at high
temperature can lead to an explosion. Avoid operating with air.
WARNING
Air/flammable refrigerant mixture! Creation of a flammable atmosphere!
Make sure the atmosphere is non-flammable before starting the system.
Ensure that the system contains only refrigerant.
5.1 Strength pressure test
WARNING
High pressure! Personal injuries!
Consider personal safety requirements
and refer to test pressures prior to test.
CAUTION
System contamination! Bearing malfunction!
Use only dry nitrogen) for
pressure testing. DO NOT USE other industrial gases.
The compressor has been strength-tested in the Emerson factory. As the compressor complies with
EN 60335-2-34, it is not necessary for the manufacturer/installer to strength-test the compressor.
Since it is not possible to isolate the compressor from the rest of the system, system strength
pressure testing according to EN 378-2 should be carried out in two steps at two different test
pressures, the high-side test pressure HPT and the low-side test pressure LPT:
▪
First, apply for a short time the HPT in the high-pressure section of the system up to the
compressor discharge stub. The compressor check valve automatically closes to isolate the low-
pressure side. During that test, make sure that the low-pressure side of the system does not
exceed the compressor maximum standstill pressure, ie, the compressor low side PS.
▪
Then, test the low-pressure section of the system by applying the LPT not exceeding the low side
PS.
5.2 Compressor tightness test
WARNING
High pressure! Personal injuries!
Consider personal safety requirements
and refer to test pressures prior to test.
CAUTION
System contamination! Bearing malfunction!
Use only dry inert gases (for
example nitrogen) for leak testing. DO NOT USE other industrial gases.
The compressor has been leak-tested in the Emerson factory. As the compressor complies with
EN 60335-2-34, it is not necessary for the system manufacturer/installer to leak-test the compress
Never add refrigerant to the test gas (as leak indicator).
Any modification to compressor connections can have an impact on the compressor tightness.
Always leak-pressure test the compressor after opening the system or modifying the connections.
5.3 System evacuation
Before the installation is put into commission, it has to be evacuated with a vacuum pump. The
vacuum pump and all tools have to be approved for A3 refrigerant/air mixture. The installation should
be evacuated down to 0.3 mbar. Proper evacuation reduces residual moisture to 50 ppm. During the
initial procedure, suction and discharge shut-off valves on the compressor remain closed. The
installation of adequately sized access valves at the furthest point from the compressor in the suction
and liquid lines is advisable. The pressure must be measured using a vacuum pressure gauge on
the access valves and not on the vacuum pump; this serves to avoid incorrect measurements
resulting from the pressure gradient along the connecting lines to the pump.
Evacuating the system only on the suction side of a scroll compressor can occasionally result in a
temporary no-start condition for the compressor. The reason for this is that the floating seal could