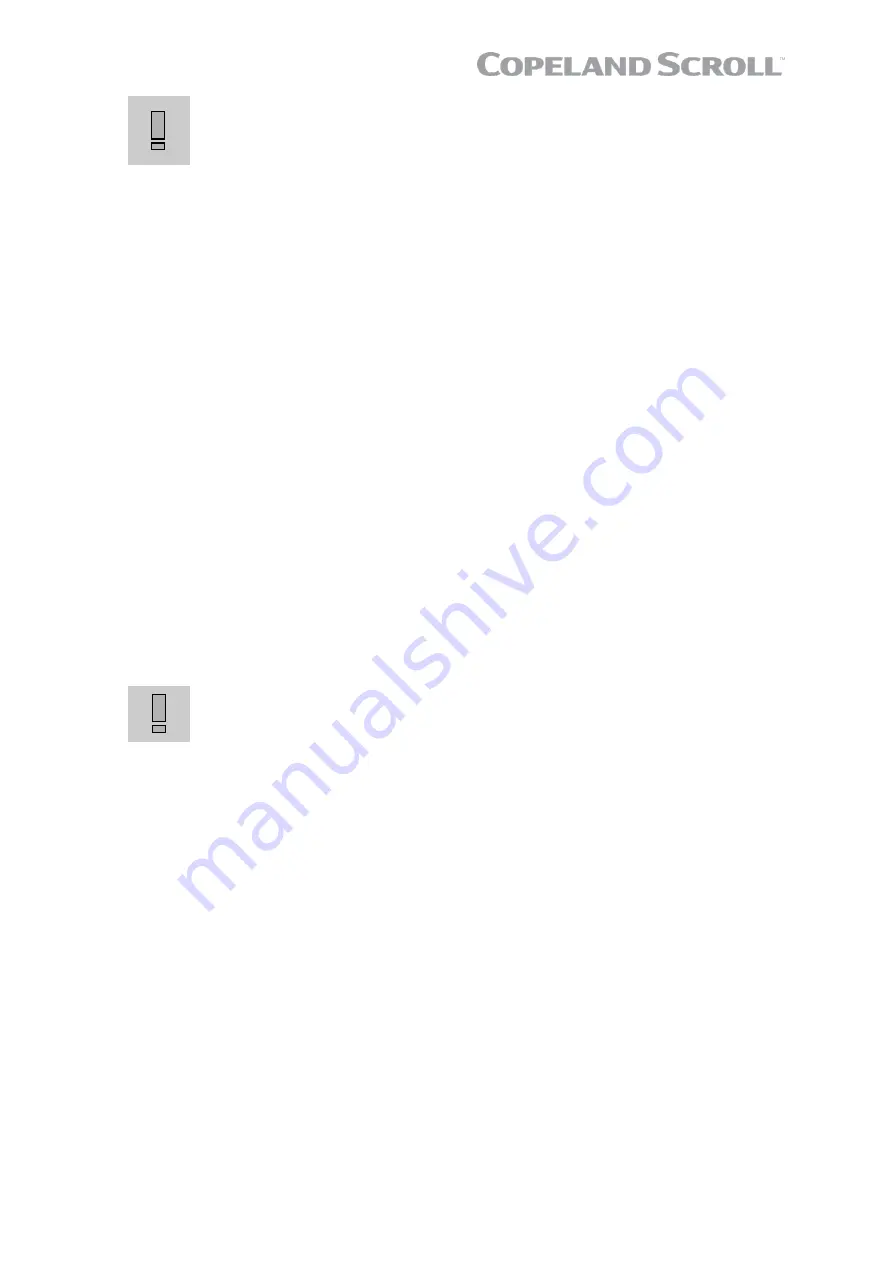
C6.2.38/0719/E
21
IMPORTANT
Operation outside the application envelope! Compressor breakdown!
A
low-pressure protection shall be fitted in the suction line to stop the
compressor when it operates outside the envelope limits.
Make sure that the pressure never falls below atmospheric pressure. If it does, immediately de-
energize the power supply of the compressor and check the cause of the low pressure before
restarting the compressor.
The minimum operating pressure could go below atmospheric pressure when observing the following
rules:
▪
valid only for hermetically sealed systems, according to the safety standards
▪
minimum absolute pressure above 0.5 bar.
▪
use temperature control on the discharge line to stop the compressor; the temperature shall never
exceed the value given in
Chapter 4.7 "Discharge gas temperature protection".
Systems in some instances must operate at low evaporating pressure because of the low ambient
temperatures, sometimes combined with a high level of relative humidity. Proper evaporator sizing
and adequate defrost strategy control will prevent the system from operating outside the operating
envelope published by Emerson, whatever the climatic conditions and the capacity demand.
However, in some extreme cases
– such as loss of system charge, extreme heat transfer restriction
at the evaporator, any defect or blocked flow control component (expansion valve, screens, etc.)
–
the evaporating conditions may be such that the compressor will operate outside the published
operating envelope limits. These conditions may result in compressor failure.
Therefore, Emerson requires that all YBVH compressors without exception be fitted with a low-
pressure protection in the suction line, meaning that no service valve between compressor and
pressure limiter is allowed. The mandatory inclusion of a low-pressure control will stop the
compressor operating outside the published envelope limits.
Customer shall follow all applicable regulations and standards to apply appropriate control to ensure
that the pressure is always above the required minimum limit.
4.7 Discharge gas temperature protection
IMPORTANT
Inadequate lubrication! Scroll set damage!
All YBVH* compressors must
be equipped with an external discharge gas temperature protection.
A good system control shall prevent the system from operating outside the published operating
envelope and acceptable superheat range, whatever the climatic conditions and the capacity
demand. However, under some extreme operating conditions (such as loss of charge or improper
control operation), the internal discharge gas temperature reached can cause compressor damage.
In order to guarantee positive compressor protection, discharge gas temperature protection is
required for any application with Copeland brand compressors. This protection must not be used as
an operating envelope controller but as a safety device. If not used, the warranty of the compressor
will be lost.
The maximum discharge gas temperature is 135°C for all YBVH* models. These compressors have
no internal discharge gas temperature protection. Therefore, an external discharge gas temperature
protector must be installed.
4.7.1 Excessive discharge gas temperatures
A few of the possible consequences are listed below:
▪
Since the oil circulates in the system with the refrigerant, it is subjected to high discharge gas
temperatures. If the discharge gas temperature becomes too high, the so-called "cooking" effect
will occur (heating of oil under exclusion of air). Carbon deposits can form at points of high
temperature, for example on the valves, oil channels, oil filters, etc. The oil lubricity will be reduced
and a progressive wear process will occur which will prematurely damage the compressor.
▪
The stability of the refrigerant can also be affected, particularly if traces of contaminant are
present.
▪
The problems listed under the first 2 points frequently occur simultaneously, particularly since the
chemical reaction time approximately doubles at every 10°C temperature rise. This directly leads