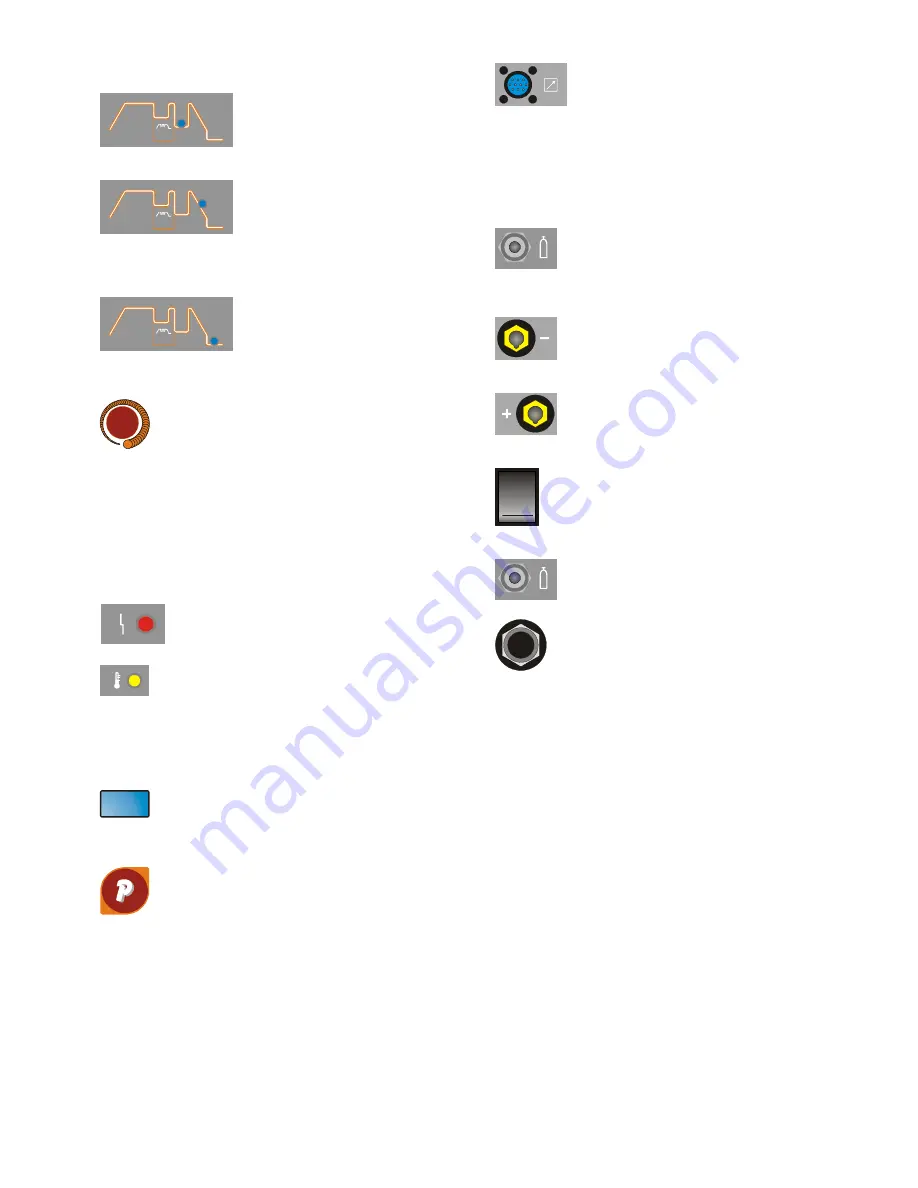
9
Pulse frequency (0.16 to 250 Hz).
The base and peak times are the same.
M LED
Second level of current in dual level mode.
N LED
Slope down. This is the time during which the current
reaches its minimum value and the arc is extinguished (0-10
sec.).
O LED
Post gas. Adjusts the gas flow time at the end of welding (0-
30 sec.).
P – Knob.
Adjusts the welding current –
G
LED.
In addition, combined with the
I
push-button, you may:
- adjust the "slope up"
H
- adjust the base pulse current
F
- adjust the pulse frequency
L
- adjust the second level of current in dual level
M
- adjust the "slope down"
N
- adjust the post gas
O
R LED – Welding machine block (see 2.3.2)
S
lights w
r
ercentage intermittence allowed for the machine and
simultaneously locks the current output.
N.B.
Un
es on cooling the
LED – Thermal protection.
hen the operator exceeds the duty cycle o
It
p
der this condition the fan go
power source.
Q – Display
Displays the welding current and the settings which were
elected via the
I
push-button and adjusted via the
P
knob.
s
W – Selector switch for programs in memory.
Selects and saves the programs in memory.
The welding machine can save nine welding programs
P01…..P09 and call them up via this button. A working
program
will flash, otherwise it remains
rm this, the program number on the
Q
display will
ing
PL
is also available.
Selecting
When this push-button is pressed briefly, the
Q
display
shows the program number next to the one in use. If this has
not been saved, the message
steady.
Saving
Once the program has been selected, hold down for more
than 3 seconds to save the data in memory.
To confi
stop flash
Y – 10-PIN CONNECTOR.
he following remote controls are to be connected to this
connector:
a) foot control
b) torch with
up/down
ol, etc.
T
start button
c) torch with potentiometer
d) torch with
e) remote contr
X – ¼ gas fitting.
his is where the gas hose of the TIG welding torch is to
be connected.
T
A1
Negative output terminal (-)
A2
Positive output terminal (+)
A3 – Switch.
Turns the machine on and off.
A4 – Gas intake fitting.
A
3.3. GENERAL NOTES
Before u
carefully read the
tandards CEI 26/9 - CENELEC HD 407 and CEI 26.11 -
make sure the insulation of the
ables, electrode clamps, sockets and plugs are intact,
for welding all types of
ectrodes, with the exception of cellulosic (AWS 6010)*.
0, then
onnect the welding cables, observing the polarity
ssing the button
C
:
e diameter of the
of joint to be
er to shut off the machine and
5 – Power supply cable.
sing this welding machine,
s
CENELEC HD 433. Also
c
and that the size and length of the welding cables are
compatible with the current used.
3.4 MMA WELDING (MANUAL METAL ARC)
- This welding machine is suitable
el
- Make sure that the switch
A3
is in position
c
required by the manufacturer of the electrodes you will be
using; also connect the damp of the ground cable to the
workpiece, as close to the weld as possible, making sure
that there is good electrical contact.
- Do NOT touch the torch or electrode damp
simultaneously with the earth clamp.
-Turn the machine on using the switch
A3
.
- Select the MMA procedure by pre
LED A
lit.
- Adjust the current based on th
electrode, the welding position and the type
made.
- Always rememb
remove the electrode from the clamp after welding.
Содержание TIG 1680
Страница 2: ...1 2 2...