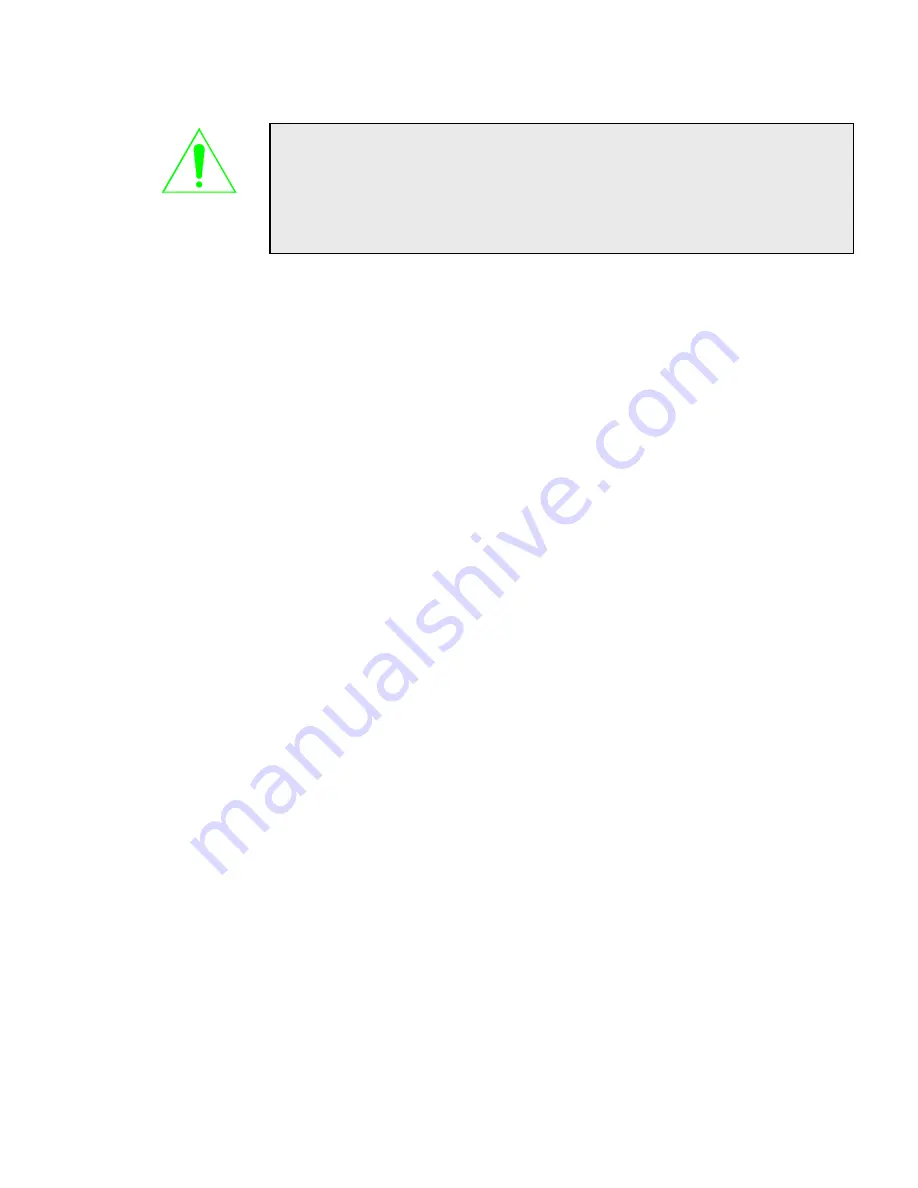
Electrostatic Technology, Inc
FlexiCoat
®
Model 300 Coater
34 Serial
#20158
12.3 COATING
BED
(continued)
CAUTION:
THE UNIFORM POROSITY OF THE POROUS
PLATE IS VERY IMPORTANT TO PROPER
COATING. DO NOT SCRAPE OR EVEN TOUCH
IT WITH A HARD OR SHARP OBJECT. NEVER
POINT AN AIR GUN DIRECTLY AT THE PLATE.
Clogging of the pores of the plate is the most common cause of failure. Once the
Porous Plate has been removed, inspect it to determine which of the following
reasons caused clogging:
•
Leaving powder unused in the bed for an extended period of time during humid
conditions.
•
Oil or water in air supply system.
•
Damage from scratching, gouging or denting the plate.
•
Blowing compressed air directly at the surface of the plate.
•
Correct the cause of plate failure and avoid conditions in the future which may
have lead to it. Order a new Porous Plate and gasket material from ETI and
carefully install.
12.3.1 Porous Plate Replacement
Step 1 -
Turn Power and Air Supply to Coating Machine "OFF".
Step 2 -
Disconnect the Powder Level Sensor Hose, and both the Powder
Feed Hose and the Exhaust Hose from the Powder Feed Chamber
above the Coating Bed. Remove the Tooling Plate (8)
Thumbscrews and lift the Tooling Plate from the Coating Bed.
Step 3 -
Vacuum all the powder from the bed using a soft brush fitting or
rubber nozzle on the end of a vacuum hose.
Step 4 -
Remove the (20) hex head bolts securing the Porous Plate Ring to
the Ionization Chamber flange. Carefully remove the Porous
Plate Ring.
Step 5 -
Remove the Porous Plate and discard it.
Step 6 -
Clean electrostatic powder out of the charging media chamber and
off the charging media if required. Note that the Porous Plate
must not have been properly sealed if there is powder in the
charging media chamber.