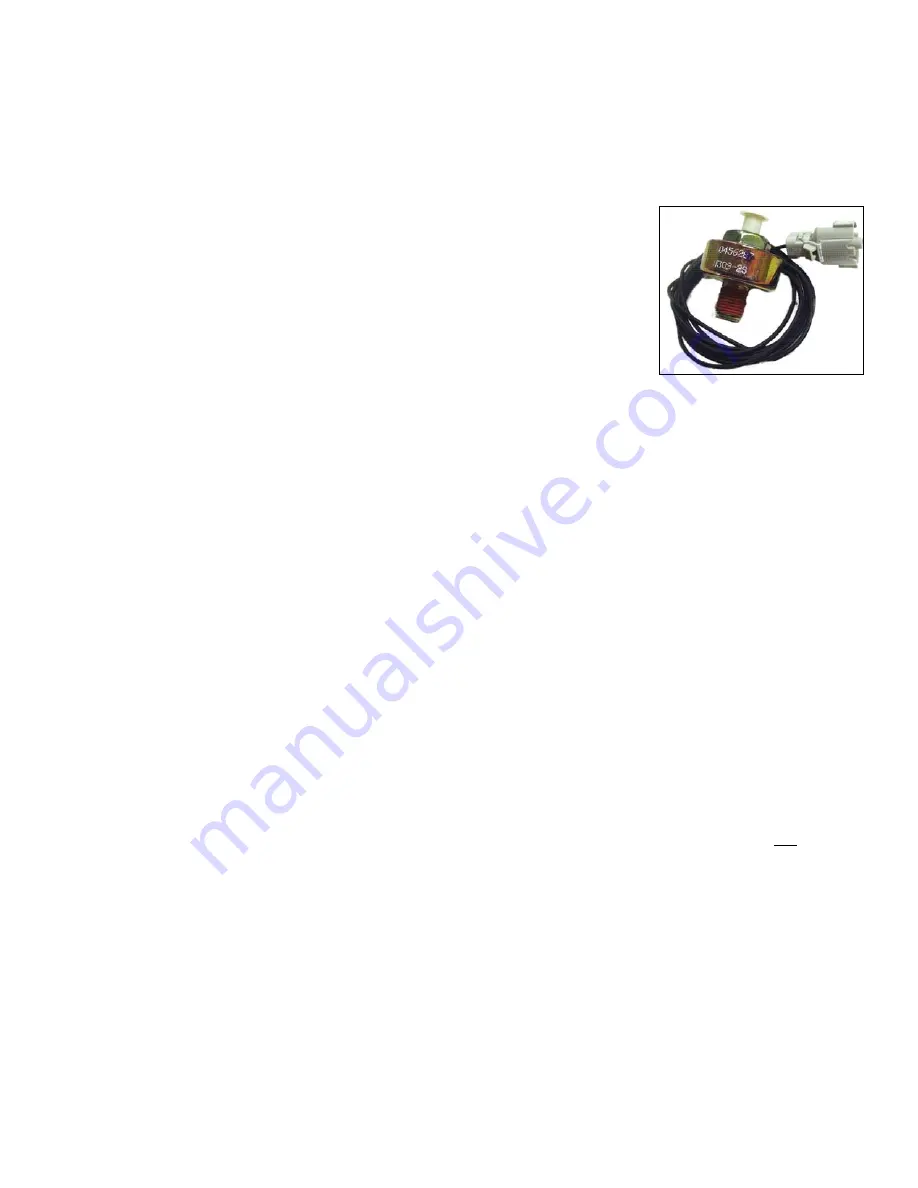
change the values, save your bin file and download it again to the
TECgt
. Turn the key off, and then back
on.
G.7. Knock Sensor
To compensate for poor fuel quality and other adverse engine operating conditions, the
TECgt
has
the ability to retard timing based on detonation. To perform this task, it uses a knock sensor to sense when
the engine is experiencing spark knock. Tuning of the knock sensor is
described in
Section B.9
of this manual.
The knock sensor circuitry in the
TECgt
is designed to sense
detonation
, not pre-ignition. Pre-ignition occurs when the air/fuel mixture
in the cylinder is ignited before the spark plug fires. This is generally the
result of a hot spot in the cylinder. When pre-ignition occurs, peak cylinder
pressure occurs after the piston has reached top dead center (TDC) of its
compression stroke, but too early to produce optimum power. Optimum
engine power generally occurs when the peak cylinder pressure is between
10 and 15 degrees after TDC compression. Thus, pre-ignition causes the cylinder pressure to peak before
the ideal 10-15 degrees after TDC compression, and in extreme cases, the peak cylinder pressure may occur
before
TDC.
Detonation
is often referred to as “pinging” or “spark knock.” On many engines, the human ear
can easily hear the sound made by detonation, since it occurs in the audible range (typically around 5000
cycles/sec). The knock sensor can hear the onset of pre-ignition as well, but better than our ears.
Detonation is defined as a pressure shock wave that develops in a cylinder as a result of a slow-
burning flame front. Typically, detonation is caused by ignition timing that is too advanced, poor fuel
quality (low octane), or poor combustion chamber design. Engines with large combustion chambers and
poor air-swirl characteristics are especially prone to detonation. During detonation, the spark plug initiates
the flame front, but the flame front moves so slowly that there is time to compress and heat the unburned
mixture to the point of
spontaneous ignition
. This results in a pressure shock wave that is akin to beating
the upward-moving cylinder with a downward-moving hammer! It also results in a noise resonance
through the engine block, just as a noise would resonate through the block if you hit the piston with a
hammer. Piston, ring, and rod bearing damage is typical when an engine is detonating too much.
To obtain an accurate reading, the knock sensor must be screwed into the engine block. A plugged
hole in a coolant passage is an ideal location, since the knock sensor is threaded for a 1/4" NPT hole. The
knock sensor is essentially a microphone that is designed to be very sensitive to the frequency of
detonation.
When
the
TECgt
senses detonation from the knock sensor, it will begin to retard the timing on all
subsequent spark events. Once knock has dropped a sufficient amount, the timing will then begin to
increase to the desired advance setting. When the
TECgt
starts to increase the advance, it will not add any
more timing than what is set in the Ignition Advance table.
Since engines are more likely to experience detonation at lower RPM’s with medium or high loads,
it is advisable to turn the knock sensor on for these conditions. On the other hand, since engines are less
likely to experience detonation at higher RPM’s (since the flame front is moving too fast for detonation to
occur), AND most engines will increase their mechanical noises that can false-trigger the knock sensor
(like valves hitting their seats), it is advisable to turn the knock control off at high RPM’s. Mechanical
noise can be identified by datalogging a light-load, high-RPM driving situation. If no detonation is heard
during the drive, but the datalog indicates that there was knock in the upper rpm/light load area, mechanical
noise may be false triggering the knock sensor.
Rotary engines are generally unable to use the knock parameter as effectively as a piston engine,
since real detonation in a rotary will typically only occur one time…then the apex seals will be broken! It
______________________________________________________________________________________
TECgt Manual Version 2.0
- Page 96 -
©2008 Electromotive, Inc.